With the above video, Ask Yourself the Following Questions;
- Why is this super hot looking stainless weld silver in color, what happened to the typical weld oxidation that occurs on thin stainless parts?
- Why is the weld so hot yet the Weld Heat Affected Zone (HAZ) so small?
- How is that spatter free, 1/4, (6 mm) TIP TIG fillet weld can being made at a weld travel rate more in common with a pulsed MIG weld?
- For those aware of the hazards of carcinogenic weld fumes generated when welding stainless chrome alloys, what happened to the weld fumes?
In an advertisement that I produced for TIP TIG USA, the USA company that my partner Tom O’Malley and I founded around 2009, I called TIP TIG “the EVOLUTION of TIG”. However while examining the TIP TIG process on a wide variety of weld applications over the next 11 years, the weld reality with this unique weld process as you will read at this site, is that TIP TIG is much more than an improved versions of the DC/AC GTAW and the Hot Wire GTAW process. Its a process that should be considered for all code quality welds.
FOR THE FIRST TIME IN 60 YEARS WE HAVE GONE FROM TWO TO THREE SEMI-AUTOMATED ARC WELD PROCESSES. Since the 1950’s, there has only been TWO SEMI-AUTOMATED cost effective arc weld processes available to the global weld industry, GMAW and Flux Cored. And the reality is with approx. 70 years of process and equipment development, both these processes as you will read at this site cannot be relied on to consistently produce welds subject to X-Rays, that will not require weld rework. Around 2009 in N.America, things changed, I introduced the semi-automated Plasch invented TIP TIG process to N. America.
Here we have a 2020, TIP TIG unit connected to a Miller Dynasty 400 amp TIG power source. Miller proudly claimed that with it’s use of sophisticated electronics in the Dynasty, that they were proud to announce to their customers who did TIG welds with the Dynasty, that in contrast to traditional DCEN TIG equipment, weld shops MAY anticipate around a 17% increase in hourly TIG weld productivity.
However when a TIP TIG Wire Feeder and Hot Wire power source is added to that Miller Dynasty unit, not only does the weld shop dramatically reduce the required TIG welders skills, they should also anticipate with the TIP TIG unit at least 200 to 400% more weld each hour. Also for the first time, the weld shop will attain the weld heat dissipation benefits of DCEN polarity, along with the numerous weld quality and metallurgical benefits that result.
Since the 1950’s, there has only been TWO SEMI-AUTOMATED cost effective arc weld processes available to the global weld industry, GMAW and Flux Cored. And with approx. 70 years of process, consumable and equipment development, both these processes as you will read at this site cannot be relied on to consistently produce welds subject to X-Rays, that will not require weld rework.
Around 2009, in N. America things changed, I introduced the semi-automated, Plasch invented, TIP TIG process to N. America, Australia and eventually to the largest oil company in China.
Two big developers of GTAW equipment in the 1950’s – 60s, were Union Carbide & Westinghouse. The reality is a DC GTA power source could be 60 years old, and in 2020, it would still enable the same DC GTA weld performance, quality and productivity and require the same welder skills and automated weld limits.
Of course the 2019 welder is now using an Inverter DC GTA power source loaded with electronics that maybe could enable DC pulsed frequency that will provide limited benefits, or it may provide AC variable polarity which is a real world weld benefit for aluminum welds. However as mentioned the benefits for DC GTA welds are few, and sophisticated inverter equipment can also makes these type of power sources less durable, and more costly to repair.
Yes the modern day welder below looks good with his fancy jacket, gloves, and weld helmet, however the reality for weld shops, is as they have been aware for approx. 70 years, the AC/DC TIG process when used on code quality welds has always provided the best possible arc weld quality, while also unfortunately requiring the highest arc welder skills and producing the lowest weld deposition rates. Deposition rates that also produce the slowest arc weld speeds that can create high weld heat input influencing both the weld and part properties.
2020 GTAW (TIG)
YOU WILL READ SOME REMARKABLE UNIQUE WELD FACTS AT THIS SITE, AND VIEW A DIFFERENT PERSPECTIVE ON AN INDUSTRY WHERE IN 2020, MOST OF THE STLS. & ALLOYS ARC WELD SPECIFICATIONS AND RESEARCH DATA IS OUTDATED OR INAPPROPRIATE. THE WELD EXPERTISE, EXPERIENCE AND APPLICATION DIVERSITY OF THIS UNPAID MESSENGER WHO REPRESENTS NO COMPANY OR PRODUCT, SHOULD BE RELEVANT TO THE READER SO HERE GOES.
Hello my name is Emily Craig, used to be Ed, but with a few plasma cuts I finally in the gender I belong. Many of you will know me by my twenty PLUS year weldreality.com web weld blog. Or perhaps you were one of thousands that attended my MIG and flux cored weld process control seminars in the 1980s. Maybe you were one of the 80,000 readers of the “Weld Design & Fabrication” magazine in which each month for almost 20 years, you read the monthly Weld QA column that I wrote. And for those of you that have a “Machinery Handbook” gathering dust on your shelf, I wrote the weld section, and was also the key technical writer of AWS MIG Gas Specifications.,
As a weld engineer, who has specialized in Weld Process Controls – Best Weld Practices for more than 5 decades, I spent the last 40 years working in 13 countries, where I was invited by hundreds of weld shops to resolve their weld quality and productivity issues. As for understanding weld equip. and consumables, I a weld product and weld training manager with Airgas – AGA – Linde / Praxair – Liquid Carbonic. As for automation expertise I was also the N. American Weld Manager for ABB Robots. I spent decades doing arc weld process, consumable and weld equipment evaluations from the world’s leading weld equip. and consumable companies.
A SUBJECT UNFAMILER TO MANY IN THE WELD INDUSTRY.. For decades, my focus was and still is on the simplification of arc weld process controls and the best weld practices required for weld process optimization. Some of you will have read one of my three books on the subject, or purchased my low cost self teach / training resources on the requirements of weld process controls – best practices. I believe that this focus and my 50 plus years of hands on experience on diverse applications and most industries provides me with the expertise and capability to critique our global weld industry, and to point out the unique attributes and detriments of each arc weld process, and how each of the common arc weld processes in 2020 compares with the TIP TIG.
With manual, automated or robot welds, my arc weld process control self teach / training programs, enable weld shops to provide the best possible weld quality at the lowest weld costs. These resources also enable front office weld decision makers the requirements for Weld Process Ownership, and eliminate the need for weld personnel to play around with weld controls when using manual MIG – robot MIG – Gas Shielded Flux Cored – Advanced TIG, and also the TIP TIG weld process.
TO UNDERSTAND TIP TIG, THE WELD DECISION MAKER FIRST HAVE TO BE AWARE OF THE PROCESS ISSUES GENERATED WITH THE TRADITIONAL DC GTA PROCESS.
TO DRAMATICALLY IMPROVE THE IMPORTANT DC GTA PROCESS, THERE HAD TO BE MAJOR PROCESS CHANGES, AND IT TOOK MORE THAN SIX DECADES TO ACHIEVE A “SEMI-AUTOMATED” GTA PROCESS THAT PROVIDES EXTRAORDINARY MANUAL AND AUTOMATED WELD BENEFITS.
There was always poor utilization of the traditional high temperature DC GTA plasma. 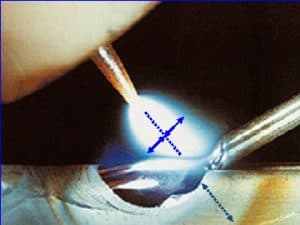
The traditional DC GTA ARC. Note the arc requirements to melt the oversize TIG wire, and also the GTA plasma energy distribution required to melt the tip of that wire and maintain to weld pool.
As the DCEN GTA process has for approx. 75 years provided the best manual arc weld quality for steels, alloys, and aluminum, it’s understandable that few weld decision makers will have given consideration to the DC or AC GTA weld issues generated by this important weld process.
The DC/AC TIG manual requirements to feed the lengths of weld wire into a short arc length, small rapid freeze weld area, influences the weld current capability and the wire melt energy and uniformity and continuity which of course will influence the weld quality, weld consistency attained between different TIG welders that are welding the same products. The manual feed requirements also will influence tungsten contamination and wear.
Many DC TIG manual welds, will as a result of the weld wire lengths utilized, have the weld requirement for frequent weld start and stops, which are common code quality weld defect locations. The starts / stops and very low deposition rates that result in very slow TIG weld speeds greatly influence the welded part heat input.
With the very low weld deposition rates attained, the DC TIG process has from a weld cost perspective, been poorly suited to many common global weld applications that required a good amount of weld metal.
The poor TIG deposition rates have on many weld applications, resulted in the weld shop requirement to use an additional, inferior, secondary weld process such as SMAW, Flux Cored or Pulsed MIG.
With the DC/AC TIG weld shop application limitations, the weld shop has had to acquire additional weld processes / weld equipment, weld consumables, and required different weld procedures, welder skills and weld practices.
Low DC GTA weld deposition rates not only affects the GTA weld speed capability, it also restricts the TIG weld current capability for the weld and this affects the weld fusion and weld porosity. Restricting current also influence the arc length sensitivity and that become especially notable with automated TIG applications.
The high TIG welder skill requirements, and the low TIG weld deposition rates, on many welds can create the Highest Weld Labor Costs.
- The DC TIG process that is “arc length sensitive,” not only adds to the manual welder skills and as also mentioned makes DC GTA poorly suited as a semi-automated process. If used with fully automated welds that require filler metal, DC GTA will often require costly, automated arc length correction equipment.
Carefully Examine the Traditional DCEN TIG Weld and Plasma Functions.
For almost 65 years, on most manual welds, the DCEN TIG process, was rarely able to fully utilize it’s full energy potential from it’s high temp. arc plasma, therefore this process also rarely enabled benefits that could have been attainable from the Electrode Negative Polarity Conductivity capability.
Examine the typical DCEN TIG weld as the large TIG weld wire is fed into the bottom portion of the plasma close to the weld pool. When melting the large TIG weld wire, as the wire gets close to the outer plasma, the wire tip melts and the DC TIG plasma is drawn slightly to the molten formation on the wire tip. The small fluid weld pool being generated by the restricted weld deposition attained is in reality a small “rapid freeze weld pool”. The DC TIG weld pool energy, and rapid weld solidification times, not only effects the TIG weld fusion potential and also porosity. The low deposition and restricted weld current also influences the weld arc stability and therefore arc length sensitivity. Take another close look at the above DC TIG plasma influence on the base metal, the weld, and the wire melt.
The multi – functions of the traditional DCEN TIG plasma and filler metal reactions.
So for almost 65 years, on most manual welds, the DCEN TIG process, has never been able to fully utilize it’s full energy potential from it’s high temp. arc plasma, therefore this process rarely enabled benefits that could have been attainable from the Electrode Negative Polarity Conductivity capability. Examine the typical DCEN TIG weld as the large TIG weld wire is fed into the bottom portion of the plasma close to the weld pool. When melting the large TIG weld wire, as the wire gets close to the outer plasma, the wire tip melts and the DC TIG plasma is drawn slightly to the molten formation on the wire tip. The small fluid weld pool being generated is restricted by the DC GTA weld deposition attained and the weld produced is in reality a small “rapid freeze weld pool”. The DC TIG weld pool energy, and rapid weld solidification times, not only effects the TIG weld fusion potential and also porosity. The low deposition and restricted weld current also influences the weld arc stability and therefore arc length sensitivity. Take another close look at the above DC TIG plasma influence on the base metal, the weld, and the wire melt.
So to compare DC GTA with DC TIP TIG weld personnel need to be aware that there are three prime multi-functions of the traditional DCEN TIG plasma and filler metal reactions.
- DC GTA…A portion of the traditional DC TIG plasma energy is being used to maintain the small fluid weld area behind the tungsten.
- DC GTA… portion of the plasma energy in front of the tungsten is required at the leading edge of the weld pool to provide sufficient energy to fully melt the large molten filler wire tip.
- DC GTA…An outer front portion of the DC TIG plasma energy is used to melt the tip of an over sized weld wire.
LARGE WIRE AND LOW CURRENT Note” that the typical DC GTA wire is a weld wire that is typically twice the diameter of a MIG wire. This large weld wire size while easy to feed in a timely manner into the weld pool, actually with the small deposition rates restricts both the weld current that could be used and potential weld deposition rates and weld travel rates that could be attained. Those low DC GTA weld deposition rates are often around a 1 lb/hr or less and so this produces very low weld travel rates that dramatically add to the DC GTA parts weld heat input. These weld process characteristics are the prime reasons the DC TIG process has for decades been highly restricted in it’s weld application potential.
2020. MANY COMPANIES LOOKING FOR GTAW WELDERS ARE SIMPLY NOT AWARE THAT SINCE 2010, IN N. AMERICA THE TRADITIONAL GTAW PROCESS HAS BEEN REPLACED WITH A MUCH EASIER TO USE PROCESS THAT DRAMATICALLY REDUCES ALL POSITION WELDER SKILLS:
For the few rare weld supervisors, managers or engineers that visit this site and can spend more than 10 minutes reading, please note. The regular DC/AC TIG process, has for decades required the highest welder skills. Those TIG welders have had to manually feed the weld wire and know when to feed and withdraw the wire. The TIG welder may be required to aggressively manipulate the torch, and also sometimes at the same time operate a foot amp control.
ARC LENGTH SENSITIVITY WITH DC GTA, HAS FOR SEVEN DECADES MADE THIS PROCESS POORLY SUITED AS A SEMI- AUTOMATED OR FULLY AUTOMATED PROCESS THAT REQUIRES FILLER METAL: As a result of the DC GTA short arc length requirements and resulting arc length sensitivity, and many of the other TIG weld issues and limitations as discussed in this section, the regular DC TIG process was not suited as a “manual Semi-automated” process, and poorly suited as a fully Automated arc weld process.
WHEN A COMPANY REQUIRES EXTENSIVE USE OF THE TRADITIONAL DC GTA WELDING PROCESS. When weld decision makers, select the DCEN GTA weld process, in 2020 they need to be aware that thanks to their weld management they are;
- requiring welders to use unnecessary high welder skills and practices, both of which influence weld quality, the weld uniformity and the weld labor costs,
- producing TIG welds that require unnecessary weld starts – stops, (typical defect locations),
- producing slow TIG welds that are providing unnecessary high welded part heat, an issue that affects distortion and mechanical – corrosion properties,
- when welding heat sensitive weld applications adding to unnecessary metallurgical considerations,
- using a process in which it’s difficult with a group of welders welding similar parts to create uniform welds, each hour ensuring that their welders are on average adding 200 – 400 % to their companies weld labor costs.
Rarely discussed in weld shops. DC GTA Weld Deposition rates and TIG Weld Costs.
Let’s say the manual DC GTA welder is welding pipe fill passes n the 5G position and using a common 3/32 steel or stainless TIG wire . The welder typically would feed around 8 to 10 inch ( 20 – 25 cm) of a 3/32 (2.4 mm) wire length each minute. That 8 inch/min of 3/32 wire delivers approx. 1 lb for each hour of arc on time. That manual DCEN TIG deposition of 1 lb/hr with an average arc on time of 20 min/hr, delivers approx. 0.03 to 0.4 lb/hr.
In contrast to a manual TIG welder, a TIP TIG welder welding the 5G fill passes on any steel or alloy steel pipe would average with an 0.035 0.9 mm MIG reel, about 180 inch/min of wire or approx. 2.5lb/hr. As TIP TIG is a Semi-automated or fully Automated TIG weld process, it would of course also increase the TIG arc on times dramatically.
While the manual DCEN TIG pipe welder is depositing 0.3 lb/hr, in contrast, with the manual TIP TIG pipe welds, and the increased arc on time of say 40 min/hr, the TIP TIG welders typically deposits on average about 1.6 lb/hr, this means the TIP TIG welder is depositing approx. 300% plus more TIG weld each hour than the regular TIG welder. You don’t have to be a rocket scientist, to figure out that this simple weld cost comparison between a manual TIP TIG and manual TIG welder would have major weld cost & hourly labor requirement ramifications for any company that bids on jobs that GTA is to be used or jobs in which concern for weld rework exists. Its important to also be aware in the 5G position, the fill pass weld speeds are relatively close to pulsed GMA and as for FCA, as no weld passes require weld cleaning with TIP TIG the weld time differences with 5G are minimal.
THIS HAS TO BE IMPORTANT TO ANY COMPANY. THE TIP TIG PROCESS THAT PROVIDES THE HIGHEST POSSIBLE ALL POSITION WELD QUALITY ALSO DRAMATICALLY ELIMINATES ALL POSITION WELDER SKILLS:
In contrast to GTAW and by the way also Pulsed GMA and gas shielded flux cored, when you examine the cost effectiveness of these processes, from root to fill weld passes, it would take less than 30 minute demo to prove that when using the manual or automated TIP TIG process, that the weld shop is not only using a superior process in which the continuous fed TIP TIG wire is fed always is in the plasma sweet spot and that this Electrode Negative process provides all position superior weld solidification that reduces all position welder skill requirements on any pipe or plate applications.
TIP TIG also of course eliminates many of the individual manual DC GTAW welder skills required such as feeding the weld wire or using an Amp Foot Control. Also TIP TIG, eliminates common concerns with learning optimum settings and practices required for the GTA – GMA – SMA and Flux Cored processes and the GMA – FCA weld influence from Wire Stick Out, (WSO) variations, that dramatically influences the weld energy produced with GMA and FCA.
A REASONABLE QUESTION IN 2020 WOULD BE..
When they have a choice and some dollars in the bank to purchase weld equip. why would weld decision makers select a weld process that, [a] requires higher welder skills, [b] produces inferior weld quality and part metallurgy, [c] with many welds GTA has to have an additional process such as MIG to complete the project. [d] creates welds with the highest labor costs?
AFTER 70 PLUS YEARS, ITS TIME TO CHANGE THE WAY INDUSTRY THINKS ABOUT CODE QUALITY AND ALLOY WELDS. I have been in many Aerospace, Defense and Medical companies that employed a group of DC TIG welders many making similar welded production parts. And the first thing I would often note on the weld shop floor, was apart from the usual, lack of management & engineering Weld Process Ownership, there also was a common LACK OF WELD QUALITY – WELD APPEARANCE UNIFORMITY on the production parts.
The common lack of GTA mfg. weld quality uniformity was greatly influenced by the fact that manual GTAW is not a Semi-automated weld process and the welder skills vary from welder to welder. Also what would be missing from not only the weld shop floor but also too often from the weld shop front office, was an evident lack of understanding or focus on the requirements for weld process controls and best weld practices.
The TIP TIG process was invented by “Plasch” in Austria.

In 2009, I found a process in Scotland called TIP TIG and while showing some early development issues with the equipment, during the 10 minute demonstration from my now friend Darren, I instantly became determined to introduce the TIP TIG process to N. America. This was no easy task, first like many weld engineers I was broke, and also in both the USA and Canada weld equipment sales are dominated by three weld equipment manufactures, Lincoln – Miller – ESAB and their weld distributor network is extremely loyal to their product lines. And also lets not forget in N. America, that most weld shops are reluctant to any major weld shop process change. I borrowed dollars, and established TIP TIG USA in 2009 with my friend Tom O’Malley. A year later, Tom and I also introduced TIP TIG to both Australia and China
AN EXTRAORDINARY WELD PROCESS. THE QUESTION IS, HOW MANY MORE DECADES WILL IT TAKE ENGINEERS TO FGURE OUT THE TIP TIG FEATURE BENEFITS?
A summary of why TIP TIG is a unique arc weld process:
Craig Notes..10-2019: The patented TIP TIG process changes that occur in the weld transfer, allows TIP TIG to provide a unique “wire to weld placement” which enables many weld benefits and allows for “more weld energy” than has been possible with the traditional DC/AC GTA welds, or with any manual arc welds. In contrast to traditional DC TIG wire to weld, note with TIP TIG the unique wire feed position at the top of the plasma, and the resulting rapid small weld drops and unique extended plasma and weld attributes that with this process allow the use continuous fed smaller wire diameters providing higher weld deposition rates that melt in the upper portion of the outer plasma periphery. That unique TIP TIG wire to plasma placement enables most of the TIP TIG plasma energy to be distributed over the weld pool. Another contrast to DC TIG, is the TIP TIG process is depositing already molten small weld drops into a now higher energy, more fluid weld pool.
As for the common tungsten changes with DC GTA , once the TIP TIG Best weld practices are learnt, the welder will likely have no more than one or two tungsten preps per-shift.
It’s important to emphasize the unique the consistent TIP TIG small wire to plasma placement at the upper outer plasma periphery sweet spot. Not only does this wire to plasma ensure gas protection for the continuous fed wire tip, (protection for easily oxidized weld wires) it also ensures “consistent, uniform wire to weld melt”, something that’s not possible with any group of manual GTA welders, this for the first time with aerospace, defense, power, medical and oil application welds, enables cost effective, uniform and consistent GTA weld quality that should be essential when a number of welders are welding similar parts.
Also remember that the TIP TIG unique wire to plasma placement enables all of the high arc temp. plasma energy over the weld pool surface. This plasma energy distribution allows the TIP TIG arc electron flow to be enhanced and will result in a wider, more dense, increased velocity plasma than that which is possible with regular GTAW filler wire welds. Combine this with the small molten weld drops that are delivered to the weld and this arc weld process is not only delivering the best consistent weld fusion potential but also the lowest possible weld porosity. Also the TIP TIG plasma improvement enables a slightly longer open arc length and therefore traditional GTAW arc length sensitivity is eliminated.
The GTA Arc Length Sensitivity has always been associated with both the regular DC/AC TIG manual welds, and also with the automated Hot and Cold Wire TIG process, which due to this sensitivity have not been suited as a manual semi-automated process.
Another major benefit from the TIP TIG plasma distribution over the high arc temp. is the increased and prolonged Weld Fluidity. Remember many alloys provide sluggish welds which will always decrease the weld fusion potential. Improving the weld fluidity also enables more TIP TIG Wire to be Fed into the weld pool. More weld wire enables more weld current to be used which further adds to the TIP TIG plasma and weld energy. The extensive changes to the traditional DC GTA plasma energy distribution and influence on the DC GTA weld dynamics dramatically adds to both the TIP TIG weld and part quality potential, and also in contrast to GTA, greatly enhances the TIP TIG weld application capability.
THE EASIEST PROCESS TO USE WITH ANY OPEN ROOT AND ALLOSITION WELDS. As you will note at this site, numerous weld benefits are being revealed and presented with this process. Another major weld shop benefit from this process is that on clean metals, from any all position, open root to fill on metals and any thickness, TIP TIG in contrast to both GTA and GMA is producing the best possible weld characteristics for Vert Up and Over Head welds and the best possible weld features for any open roots (no other arc process can deal with root gap dimension variations as TIP TIG can) Easy to learn as no more than 3 settings are required, and easy to use both as a manual, Semi-automated or fully automated process, and that includes and robot applications, and remember without the additional requirements for costly automated arc length sensing devices, as typical with the GTAW – Hot Wire and Cold Wire processes.
What makes TIP TIG UNIQUE, is not as many believe “the agitated weld pool” rather it’s the vibration effect on the weld wire that enables rapid weld drop detachment.
So as you see the continuous fed TIP TIG weld wire is fed through a set of patented wire feed drive rolls that go back and forth with a rapid velocity and this makes the wire vibrate like a plucked guitar string.
Craig Note.. 10-2019: The patented TIP TIG weld wire vibration enables rapid weld drop detachment, which in combination with the additional 80 to 120 amps in the wire delivered from an AC Hot Wire power source, preheats the weld wire. This produces a weld transfer mode with weld capabilities way beyond any pulsed GMA weld mode. The TIP TIG wire vibration, the use of regular size MIG wire, the rapid small fluid weld drop detachment. The improved wire to plasma placement that enables more plasma coverage on the weld surface. The increased deposition that enables more current producing the highest possible arc temperatures. In combination with the EN polarity and the inert gas, produce a weld process that should excite every weld decision maker and metallurgist that produces code quality welds.
Yes the wire vibration has a small influence on agitating the weld pool which could add micro seconds to the fluid weld solidification time however increasing current, changing the arc length and reducing weld travel speed has a similar effect.
SO WHAT MAKES TIP TIG UNIQUE?
[1] LOW WELD VOLTS. [2] INCREASED WELD SPEEDS. [3] EN POLARITY. [4] INERT GAS, ALL COMBINE TO ALWAYS ATTAIN THE HIGHEST WELD QUALITY AND LOWEST POSSIBLE ARC WELD / PART kJ/inch INPUT:
Craig 10-2019: The TIP TIG higher DC GTAW weld deposition rates of typically 200 to 400% than that attained with regular GTA dramatically influence both the weld speeds attained and therefore the welded part heat produced. That increased deposition also in contrast to GTA enables higher current than that which manual GTA welders typically use.
PROCESS CHANGE CAN BECOME ESPECIALLY DIFFICULT IN AN INDUSTRY WHERE PROCESSES ARE ENTRENCHED. That 200 to 400%, increase in the amount of DC TIP TIG weld produced each hour with a dramatic reduction in welder skills, you would think would get “many weld shop engineer, managers and supervisors exited”. You know the old saying. “You can lead a donkey to the water trough, but you cant make it drink the water”.
As regular DC TIG weld personnel are aware, traditional DC TIG is an Electrode Negative Polarity process in which the arc energy is rapidly directed into the conductive base metal. However with traditional GTA welds few benefits are attained from EN polarity as many GTA welds are made with very slow weld speeds. Lets take a look at weld kj/inch reductions that are enabled by the unique process attributes from the TIP TIP process.
TIP TIG Vs GTA. Pipe weld Kj/inch input comparison.

In contrast GMA and gas shielded flux cored (both much lower arc temp than DC GTA) are electrode positive processes in which the majority of the plasma arc energy is concentrated at the continuous fed weld wire tips. This EP arc heat retention is the reason with these two processes that there is always extensive heat around the weld especially in the GMA and FCA weld’s HAZ’s.
Now with regular DCEN GTA, the expected rapid weld heat conductivity benefits into the parts welded into the Positive parts being welded is rarely attained and the reason is a simple one. With traditional DC GTA the typical very slow weld travel rates attained, from the low weld deposition rates attained, help retain the welded part heat so that with DC GTA, GMAW and FCA welds the weld HAZs are similar.
IF EVERY ALLOY IS HEAT TREATED, IT’S LOGICAL TO USE A WELD PROCESS THAT NOT ONLY PROVIDES THE HIGHEST POSSIBLE WELD QUALITY BUT ALSO THE LOWEST POSSIBLE WELD HEAT INPUT.

THIS SHOULD SHOCK MANY IN THE N AMERICAN DEFENSE, POWER AND AEROSPACE INDUSTRIES, THAT SINCE 2009, WITH TIP TIG, THE WELD SHOP HAS HAD THE EXTRAORDINARY CAPABILITY TO READILY REDUCE WITH ALL METALS INCLUDING ALUMINUM , THE WELD JOULES HEAT INPUT BY 35 TO 55 %. AND THIS DOES NOT TAKE INTO ACCOUNT THE THERMAL CONDUCTIVY INFLUENCE THAT OCCURS WITH DCEN POLARITY.
A NOTE TO THE APPROPRIATE EUROPEAN AND NORTH AMERICAN CODES & SUCH AS ASTM – ASME – AWS SPECIFICATION COMMITTEES. THESE ORGANIZATIONS NEED TO REVIEW THER OUT DATED WELDED PREHEAT – INTER-PASS OR POST HEAT GUIDE LINES THAT HAVE BEEN IN PLACE FOR THE TRADITIONAL FOUR WELD PROCESSES SUCH AS GMA – FCA – GTA – SMAW METALS FOR MANY DECADES. A REMINDER TIP TIG IS ALREADY A DECADE OLD PROCESS.
MECHANICALS – CORROSION – DISTORTION. The dramatic change in TIP TIG reduced weld heat capability can enable extraordinary, weld / clad, never before attained, mechanical, corrosion and metallurgical properties, always with the lowest possible weld distortion and lowest weld fumes.
A SIMPLE TEST OF THE LOW WELD PART HEAT PRODUCED IS SHOWN BELOW. As an example of the lowest possible weld heat into the parts, we do away with the gas trailing shields which is normally recommended protect Titanium from oxidation when DC TIG or GMA is used. As you see below gas trailing shields would no longer be a requirement for many TIP TIG Titanium welds.
IN 2009, AS I SET THE TIP TIG PARAMETERS, I WATCHED IN AWE THE SILVER COLOR THAT WAS REVELAING ITSELF DURING TOM’S WELD THAT WAS ARE FIRST ATTEMPT ON THE TITANIUM PARTS.
Note: A silver color as is titanium weld is an indication the weld and part heat never went above 800F. Note the untouched silver color and note the 24 inch / min weld speed which in contrast to GTA is very fast, but in contrast to pulsed GMA would be slower. However thanks to the low voltage used with TIP TIG and the EN polarity. TIP TIG on these grade 2 titanium parts was producing what no other arc weld process can.
UNFORTUNATELY TOO MANY WELD DECISION MAKERS IN FORTUNE FIVE HUNDRED COMPANIES ARE WHEN IT COMES TO WELDING STUCK IN THE 20th CENTURY:
Someone should put the above advice on the notice board of every Defense, Aerospace, Power, Oil and Medical Equip. company in N.America.
Around 2009 at time when TIP TIG was available in the USA, the shipyard designers, managers and engineers who made the costly decision to use DC TIG for their Titanium pipe welds produced during construction of pipe on a US Aircraft Carrier, were in reality stuck in the 20th Century, and in sync with the US Navy who every year pays contractors hundreds of millions of dollars on unnecessary weld-rework and labor costs. This sad engineering approach has in Navy Ship Yards gone on for decades, and in 2020, the majority of defense contractors are still using the 20th Century, apathetic weld approach to much of their code quality weld and fabrication, a management and engineering approach that reveals the too common front office lack of capability for weld process ownership.
OVER FIVE BILLION DOLLARS ARE LOST ANNUALLY ON WELD QUALITY AND PRODUCTIVITY ISSUES. THE REALITY IS WITH WELD PROCESS CONTROL AND BEST WELD PRACTICE EXPERTISE COULD EASILY BE ELIMINATED.
BY THE WAY THIS IS EXPERTISE THAT’S AVAILABLE AT MY WELDREALITY.COM. AN EXPERTISE THAT GLOBAL COLLEGES AND UNIVERSITIES DON’T TEACH TO THEIR TECHNICIANS AND WELD ENGINEER STUDENTS.
We are all likely aware of the unnecessary hundreds of millions of dollars lost annually in large ship yards due to poor flux cored and MIG weld quality and productivity issues, or the never ending robot MIG problems in most global auto / truck plants. However, it’s also a sad weld reality that in 2020, the majority of Defense, Aerospace, Oil and Power industries that are more than well served by mechanical and weld engineers, are in 2020, likely utilizing the 1946 GTAW process. A process that requires the highest welder skills, produces the lowest weld productivity, and to often on heat sensitive weld applications, puts in too much weld heat into the parts.
Consider TIP TIG when;
- all position, code quality welds are required,
- the welds require open roots and fill passes that are subject to internal weld quality NDT,
- the welded parts have concerns for distortion,
- the welds have a special concern about the weld fusion or porosity.
- the welds are on alloys, alloy steels and high strength steels,
- the welds and parts require specific mechanical and corrosion properties,
- the welds have preheat – inter-pass temp. or post heat requirements, that could now be reduced or eliminated,
- it’s highly cost beneficial if reduced groove weld dimensions are possible,
- weld fumes are a concern,
- welds are being produced in which grinding and cleaning need to be eliminated.
Please remember that the fully equipped semi-automated or full automated TIP TIG system is also when required an AC/DC TIG unit. So when TIG is required for example weld a very thin application say 0.010 thick, the welder can just shut the TIP TIG wire feed and hot wire unit off, and DC GTA weld the part.
Ref Aluminum Welds: If wire feed ability is not an issue as with the > 0.046 (1.17mm) 5XXX series aluminum wires, TIP TIG using the Balance Wave, 80 – 90% EN – EP, Variable Polarity, will with the faster welds TIG speeds enabled, lower weld heat to levels never before attained and create aluminum welds with much higher welded part strength and lower weld porosity than has ever been possible with a TIG or Pulsed MIG weld.
Above. From a weld engineering perspective, DC TIG welding was an inappropriate and outdated approach for this Navy Ship Building yard when it was selected to weld this Titanium and other pipe welds on a 21st Century US Aircraft Carrier.
2009: Chinese National Oil Company. when it comes to welding, a decade ahead of N.American – European Oil / Nat Gas companies.
After I introduced TIP TIG to CNOC in 2009, their engineers and managers quickly embraced the process Above in 2009, two Chinese National Oil Company TIP TIG welders producing Inconel and steel Sub-sea pipe welds, and in reality attaining a weld quality and productivity simply not possible from the most advanced Pulsed MIG or DC GTA equipment, (discussed below).
Here we are in 2020, eleven years after I introduced TIP TIG to N.America, and in the common “why change the way we have always done it” Defense, Aerospace, Oil and Power company weld shops, too many engineers and managers continue to use for their pipe, vessel and plate groove code quality welds, outdated or inferior weld procedures and out dated inferior weld processes such as TIG, Pulsed MIG of FCAW.
WAKE UP AMERICA….I ALWAYS FOUND IT IRONIC THAT AFTER GOING TO GREAT RISK, HASSLE AND EXPENSE I COULD NOT AFFORD, TO ESTABLISH THE TIP TIG PROCESS IN THE USA AND AUSTRALIA DURING 2009, THAT THE FIRST COMPANY TO RESPOND AND PLACE AN ORDER, WAS ONE OF THE LARGEST OIL COMPANIES IN CHINA.
In contrast to Pulsed MIG and Gas Shielded Flux Cored, TIP TIG is an expensive process yet it also is a semi-automated process, and as with any weld process selection, requires logical weld quality – weld productivity and weld cost justification. As for TIP TIG cost versus TIG welder costs, if it takes three TIG welders to do the work of one TIG welder, well even Donald Trump could figure out the annual cost savings produced.
SO HOW LONG DOES IT TAKE TO TRAIN SOMEONE TO USE THE TIP TIG PROCESS? Most pipe welders would consider a 5 or 6G pipe open root, as the most difficult part of a pipe weld. With TIP TIG, you would show the person who wants to weld in these positions and do what any TIG welder would do on a pipe root, and that is walk and weave the ceramic Cup across the pipe groove and root surface.
However in contrast to regular GTA. With TIP TIG there is no feeding a weld wire and no foot control required. With the semi-automated TIP TIG process, of course reduced weld starts /stops are required, and with the continuous fed TIP TIG wire at the plasma sweet spot, the welder will provide a manual pipe root and fill weld continuity never before attained with GTA or Pulsed GMA.
FOR MANAGERS AND ENGINEERS AWAKE TO WELD OPPORTUNITIES, THE TIP TIG SHORT ALL POSITION PIPE OR PLATE TRAINING TIMES, IS SOMETHING THAT ALL GLOBAL WELD DECISION MAKERS DEALING WITH CODE WELDS SHOULD GET EXITED ABOUT:
A FEW DAYS: If the pipe welder using TIP TIG is used to DC TIG welding, 5G open root pipe welds, it would takes one to two days to teach them the required TIP TIG Best Weld Practices and Weld Settings as provided in my TIP TIG program. (TRAINING RESOURCES). However something that should bring joy to those managers who have unnecessarily been keep complaining over the last decade how difficult it is to “find skilled TIG welders”. It would take someone again using my TIP TIG training program about eight to ten days to train a person Who Has Never Welded to become a TIP TIG pipe weld expert with the ability be able to pass any code, (including ASME) all position, Pipe Welder Qualification Tests.
I am well aware, that at most of the Fortune 500, Defense, Aerospace, Power, Oil and Medical corporations, that you will usually find minimum understanding in the plant’s engineering office on the weld quality – cost benefits attained with weld process controls and on best weld practice expertise. The general lack of weld process control awareness is typically responsible for the general global lack of front office weld process ownership capability that influences the daily poor or inconsistent weld quality, rework, rejects and often unacceptable weld production costs. By the way, any manager or engineer that believes in the importance of weld engineering evolution, should take a look at the dates of the weld procedures and specifications that they daily use, and wonder why as we get close to 2020 that their company is still likely using Weld Procedures & Specifications that were establishes in the 20th century.
JUST ABOUT EVERY WELD TRAINING DEPARTMENT, UNIVERSITY AND COMMUNITY COLLEGE WELD PROGRAMS THAT I EVALUATED IN THE LAST THREE DECADES WERE STUCK IN A 1980’s TIME WARP. IF COMPANIES WANT DRAMATIC WELD QUALITY IMPROVEMENTS AND COST REDUCTIONS, THEY SHOULD AT LEAST WONDER WHY THEIR EXISTING WELD TRAINING PROGRAMS RESULT IN WELDERS OR WELD DECISION MAKERS FREQUENTLY PLAYING AROUND WITH WELD CONTROLS. AND ALSO EXAMINE THEIR COMPANIES LACK OF ABILITY TO CONSISTENTLY ATTAIN OPTIMUM, UNIFORM GMA – FCA – GTA WELD QUALITY AND PRODUCTIVITY FROM WELD PROCESSES THAT HAVE CHANGED LITTLE SINCE THE 1960s.
Note: My easy to learn TIP TIG Self Teaching / Process Controls – Best Weld Practice Training programs is critical for those that want optimum utilization of the TIP TIG process. The program requires approx. 15 hours and has all the TIP TIG best weld practices and weld settings for any weld applications.
NOTE: Please be aware that its no good purchasing a new process such as TIP TIG and then have weld personnel that are not aware of how to get the best possible weld results on the numerous weld applications that TIP TIG should be used on. Many global weld shops do this, and the equipment will soon be discarded and gather dust,
It does not matter how experienced weld personnel are, all weld personnel including front office weld decision makers will benefit from process control training programs that quickly enable process optimization. To get immediate and dramatic weld quality – cost benefits from the TIP TIG – GMA – GMA ROBOT or FCA process, consider spending a couple of hundred dollars and get the world’s best process control – best practice self teach / training programs.
Em’s TIP TIG + Advanced TIG. – Manual – Robot MIG – Flux cored, Weld Process Controls & Best Weld Practice, Self Teaching / Training Programs.
SpaceX, while extensive engineering evolution is evident in it’s rocket technology, this company through poor weld management was slow to evolve in it’s weld engineering technology.
Some are slower than others. SpaceX first learnt about TIP TIG around 2009, it then took their engineers and managers ten more years to figure out that this was the arc weld process that would give them the best opportunity to consistently pass the NASA destructive tests for the Falcon rockets.
Evaluating the weld quality / productivity, semi-automated TIP TIG process benefits, as Elon Musk and his SpaceX managers / engineers eventually discovered, is not Rocket Science. With this process any weld shop will quickly find out that TIP TIG;
- will in contrast to the other arc weld processes, show that all position welder skill requirements are dramatically reduced,
- will always produce superior weld quality with improves weld uniformity and consistently,
- will show that inter-pass temperatures are typically not required, and pre-heat and post heat will often be eliminated or reduced.
- will show that distortion issues are no longer a concern,
- will reveal on all metals that weld & part cracks no longer concerns,
- will show no weld porosity concerns,
- will reveal no weld fume concerns,
- will eliminate weld rework,
- will in contrast to DCEN TIG, on average, enable 200 – 400% more weld each hour,
- will on all position welds produce weld speeds that are compatible with the inferior pulsed MIG process.
THE GLOBAL, MANAGEMENT AND ENGINEERING INDUCED NONSENSE ABOUT THE SO CALLED “SKILLED WELDER SHORTAGE” HAS FOR DECADES BEEN SIMPLY RIDICULOUS, AND UNFORTUNATELY ITS SIMPLY BEEN ANOTHER INDICATION OF THE GENERAL FRONT OFFICE MANAGEMENT AND ENGINEERING LACK OF WELD PROCESS OWNERSHIP CAPABILITY.
So here we are in 2020, and as they have done for decades, those managers and engineers that lack the ability for weld process ownership with ARC weld processes that typically have one or two controls, will be found in welding magazine articles complaining about their inability to find “skilled TIG welders”. Yet the reality is that thanks to TIP TIG, the traditional TIG weld skills have been redundant now for more than a decade. And for those apathetic managers and engineer who can’t find skilled MIG and flux cored welders, read below or visit www.weldreality.com
Common comment in many global weld shops
2020.. In the “why change the way we have always done it” Aerospace, Defense, Power and Oil industries, you will find with the majority of facilities that weld are still stuck in the 20th Century using traditional GTAW as their prime arc weld process. This is a process that requires the highest welder skills, provides the lowest weld deposition rates and produces high welded part heat input. This is an indication of what?
Welders don’t typically advance weld technology, but weld decision makers should.
2020. IT’S NOT JUST ABOUT THE N. AMERICAN LACK OF GLOBAL WELD SHOP AWARENESS OF THE 10 YEAR OLD TIP TIG PROCESS, IT’S ALSO THE GENERAL LACK OF ENGINEERING AWARENESS OF WELD PROCESS CONTROLS AND BEST WELD PRACTICES.
In the last decade, two of the companies that I provided MIG and flux Cored process control training employed approx. 700 weld personnel. Many of the weld personnel had limited weld experience, and the majority with weld experience played around with their weld controls and were mostly using poor weld practices. One training program I provided occurred in a USA. ship yard that made oil tankers and container ships. The other training program was for a company that built rail road tankers for transporting oil. These two industries had something in common in that they both used gas shielded flux cored and MIG. In both facilities, I required less than 7 days to enable over 200 “none welders” to meet the ship yard ABS ceramic backed, and the rail road companies AWS steel backed, all position, Gas Shielded Flux Cored welder qualification tests. For those that had weld experience it took my one day program for these personnel to learn the requirement for weld quality – productivity optimization.
Note: Above Photo. Myself in blue sweater in the rear, and my friend Tom, (blue right), training ship yard welders in something that in reality has for decades, been a missing link in most global ship yards. Weld Process Controls – Best Weld Practice Training. This training has little in common with the usual ship yard welder training program. Its a program that enables the participants, the weld process controls – best weld practice expertise, so when they walk up to a MIG power source, they can instantly, (without playing around) set optimum FCAW or MIG parameters, and then use the required best weld practices to produce welds that would ensure minimum weld rework and welds with maximum weld production.
For those interested. My weld process controls – best weld practice self teach / training resources are applicable to MIG – Robot MIG- Gas Shielded Flux Cored, GTAW / Advanced GTAW and now also the TIP TIG process. link here, https://weldreality.com/weld-training-resources/
Now take a close look below at the semi-automated TIP TIG process. First examine the arc, plasma and the unique continuous fed weld wire delivery features that will be discussed below.
There are numerous weld benefits derived from using the Semi or Automated TIP TIG process:
FOR MANY DECADES, TWO SEMI-AUTOMATED WELD PROCESSES HAVE BEEN COMMONLY USED ON CODE QUALITY WELDS.
The two most utilized, Semi-automated arc weld processes used on Code welds, have been the EP, reverse polarity GMAW (MIG / MAG) and the Gas Shielded Flux Cored process. With these two weld processes, once three simple weld parameters were learnt, (to learn, visit my MIG – FCAW self teach / training process control resources) per wire diameter used, the optimum wire feed rate and weld voltage was set for the continuous fed weld wire. The welder would then press the gun switch and then direct and guide the gun to where the weld was required. However the reality has been for seven decades, that in contrast to any of the 2020, available sophisticated EP Pulsed MIG power sources, with their wide variety of weld transfer modes, or with any available gas shielded flux cored or metal cored wire, that in contrast, the higher weld energy DCEN TIG process, with it’s inert gas protection, the TIG process has been the process to go to when the highest manual arc, code weld quality was desired.
ALWAYS SUPERIOR QUALITY WITH IMPROVED WELD CONSISTENCY AND UNIFORMITY. 200 TO 400% INCREASE IN GTAW PRODUCTION, AND ALWAYS HIGHEST POSSIBLE MECHANICAL PROPERTIES SHOULD WAKE UP ANY MANAGER OR ENGINEER INVOLVED WITH WELDS. With TIP TIG the weld wire is continuously directed into a unique upper plasma sweet spot. The position enables the highest possible plasma energy coverage over the weld, which in contrast to manual DC TIG, enables the ability to consistently deliver more weld wire and attain higher weld energy that always delivering the highest possible quality weld in an inert atmosphere, that’s more consistent and uniform, than manual GTAW. And lets not forget, with the increased TIP TIG weld travel rates and EN polarity, for the first time in arc weld history, the weld shop has a manual or automated arc process that should always attain the lowest distortion, the least weld / part stresses, and the highest possible welded part metallurgical properties.
TIP TIG, patented, Semi-automated Wire Feeder for either Manual or Automated arc welds. A brilliant mechanical action is the heart of the Austrian,TIP TIG, Plasch, Austria patent. There are cheap copies and the way to test them is in all position weld capability with the deposition rates attained. TIP TIG no magic electronic bells and whistles or the usual exaggerated weld sales claims, just a simple, wire feed mechanical action combined with AC Hot Wire current.
WIKEPIDA ADDS TO PROCESS CONFUSION THAT’S WITH THIS PROCESS IS COMMON THROUGHOUT THIS GLOBAL INDUSTRY; 2020 Note: Wikipedia and the majority of weld decision makers around the globe that I have followed that have been discussing the TIP TIG process, have for the last decade, an incorrect concept of the TIP TIG process, or have been providing incorrect descriptions of TIP TIG. As you are likely aware, in pulsed MIG, Reverse Electrode Positive, the electrons travel from the negative metal across the arc plasma and collide with the gas molecules and deliver around 70% of the plasma energy to the tip of the positive , continuous fed, MIG wire tip. An important note, the CV MIG welder can influence the weld transfer modes, short circ. globular or spray through changes to gas mixes utilized and the wire feed rate and volts. With Pulsed MIG the power source can also influence the weld drop size, and the rate of weld droplet detachment through the pulsed MIG parameters.
In contrast to the semi-automated pulsed MIG transfer, both the traditional DCEN GTAW, and DC TIP TIG circuit have a completely opposite function. With DCEN TIP TIG and DCEN TIG, first arc temperatures are far greater than possible with a MIG arc. The TIP TIG electrons travel from the tip of the negative tungsten to the positive ground. The electrons in the arc, apart from colliding and breaking the larger argon gas molecules for a high temperature plasma, provide the energy necessary to melt the weld wires. While TIP TIG is a semi-automated weld process, in contrast to MIG, most of the influence of the TIG power source is on the weld rather than on the wire running into the weld. Adding a Hot Wire current in the TIP TIG wire speeds up the weld melt, and using pulsed and variable polarity will also effect both the wire melt and weld.
As the TIP TIG wire melts, it forms droplets on the continuous fed wire tip. The key question is, what can be done to enable those weld drops to detach in a rapid manner before the continuous fed TIP TIG wire and drops make contact with the weld and disrupt the wire / weld transfer. The patented TIP TIG wire vibration, enables the weld droplets to detach and cross the arc. In contrast to DC TIG, the TIP TIG process allows much more weld wire to be deposited, which like a domino effect, enables more weld current to be used, and this influences both the plasma and weld?
Thanks to the Austrian, patented, Plasch invention, the TIP TIG wire vibrates, and like a plucked guitar string it agitates the wire so as the continuous fed wire exits the copper tip, the wire agitation “encourages rapid weld droplet detachment” from the wire. The more weld wire that can be delivered into the plasma, and on average TIP TIG delivers approx. 200 to 400% more weld than is possible with any GTA weld, the higher the weld current that can be utilized for the welds. The use of Hot Wire current also slightly decreases the time required for the molten welds drops to form. That increased weld current influences the weld energy and also increases the TIP TIG arc plasma density and width. These attributes reduce arc length sensitivity enabling TIP TIG to also be an excellent automated process without the concerns for arc length sensitivity, a common issues with GTA automation.
Since the 1940's, there has never been an arc weld process that provides the weld energy and welded part metallurgical benefits that can be attained with either the manual or automated TIP TIG process.
UNIQUE ATTRIBUTES OF THE TIP TIG PROCESS
IN THE LAST DECADE, MANY OF THE WELD DECISION MAKERS THAT ARE EASILY INFLUENCED BY A WELD SALESMEN, THOUGHT THE SOLUTION TO IMPROVING THEIR CODE QUALITY WELDS, WOULD EVENTUALLY COME FROM IMPROVEMENTS WITH THE PULSED MIG PROCESS.
Many weld decision makers in this industry believed in the 21st century, that with the never ending electronic bells and whistles they see added to the semi-automated Pulsed GMAW (MIG) process, that the Pulsed MIG would eventually provide the manual and also automated weld solutions to consistently enable all position code quality welds that don’t require weld rework. The weld reality is just as a donkey can never be a race horse, the pulsed MIG process will never have the unique weld process characteristics that is necessary to attain the weld quality and part metallurgical properties that can be attained with another semi-automated process called TIP TIG.
In my roles as both Corporate Product and Training managers with Linde, Airgas, AGA, ABB and Liquid Carbonic. I have been evaluating Pulsed MIG equipment from all the major GLOBAL Pulsed MIG mfgs. since the early 1980’s. And in the 1990’s, in my 600 page book “A Management and Engineers Guide to MIG” (training Resource Section) I wrote over a 100 pages on the issues with Pulsed MIG, and the reality is in 2020, that most of my 1980s pulsed MIG concerns are still relevant, however no one reads the book.
Note: For those interested in the extensive weld issues generated with Pulsed MIG especially in robot cells, you may wish to visit my MIG process / equipment sections at my weldreality.com site. or purchase one of my MIG weld process control self teach / training programs, also visit the TIP TIG versus Pulsed MIG section here.
The weld shop should be aware that if DC TIG, Pulsed MIG and Gas Shield Flux Cored is not attaining a weld quality in which zero weld rework is produced, with TIP TIG it’s easy to attain these weld results. The weld shop should also be aware with TIP TIG one TIP TIG welder will on average in a shift do the welds that three GTAW welders will do, and with TIP TIG there is no weld application size or part thickness limits.
TIP TIG All Position Welds are Easier than GMAW
REAL WORLD WELD BENEFITS FROM TIP TIG: With TIP TIG, no manual wire to feed and no amp foot control required. TIP TIG always superior control of arc starts – stops. TIP TIG no spatter, no weld fume concerns and no weld rework. With TIP TIG the smallest weld HAZ is produced with the least stresses and distortion. With TIP TIG always the highest weld and part metallurgical properties. Yes it’s an expensive process but the weld cost savings from no rejects or rework along with the dramatic reductions in welder skills and increased GTAW productivity and the cost is quickly justified.
As with any costly equipment to be used in a weld shop, the TIP TIG process of course requires cost justification, and it’s logical that weld shops during a TIP TIG demonstration should want to see and measure the improvements and cost reduction capability that will be provided by TIP TIG;
- With a short training program that should be presented not only to the welders, but also to all those that make weld decisions. (see my low cost TIP TIG training / self teaching power point programs), TIP TIG dramatically reduces all position welder skills, which enables increased and more consistent, uniform weld quality. In contrast to TIG – Pulsed MIG and Flux Cored, R
- The TIP TIG all position welder skill reductions dramatically reduces welder training times.
- TIP TIG dramatically improves both DC and AC TIG weld quality.
- TIP TIG enables more weld current than GTA welds which when combined with the unique TIP TIG wire placement produces a higher energy plasma with increased plasma coverage over the weld. Weld fusion is the highest possible with the lowest possible weld porosity.
- Weld quality is further improved from the TIP TIG consistent wire feed placement to the plasma sweet spot which enables the continuous, uniform melt of small weld drops that provide increased weld fluidity.
- In contrast to GTAW, with TIP, arc start – stops are dramatically reduced and with decreased arc length sensitivity their is less opportunity for tungsten contamination and tungsten melt.
- TIP TIG enabling on average 200 – 400 % more weld than DC TIG, enables increased weld current capability, and faster weld speeds, reducing weld costs.
- TIP TIG greatly extends the weld application potential and no job is to small, thin, large or thick.
- Be aware that for 5 – 6G pipe welds, the TIP TIG manual fill pass weld speeds would be similar to pulsed MIG.
- TIP TIG increased welds speed capability with electrode negative polarity dramatically lowers the welded part heat, which always enables superior welded part properties, with no concerns for carbide precipitation that affects corrosion, or concerns for weld stresses, part distortion and weld fumes.
- TIP TIG eliminates arc length sensitivity concerns, making it suited to all manual semi-automated and fully automated applications.
- TIP TIG enables the following results on the stainless fillet in the video below, The weld produced process attributes that no weld shop can produce when using DC TIG or any Pulsed MIG process.
With the above TIP TIG stainless gauge fillet weld, note the weld color, lack of oxidation, no spatter, and small HAZ that results from the lowest possible weld heat into the parts. Note how the welder can hold the TIP TIG torch just like a GMAW gun or if required like a GTAW torch. As with any semi-automated arc weld process, on parts with decent fit, with TIP TIG no weld weaves or skipping techniques should be used when making single pass fillet or lap welds up to 7 mm.
With TIP TIG, you have the best of both worlds, for groove or fillets, you can either rest the ceramic torch nozzle in a groove or on the plate, and if you walk the cup which adds to the simplicity and control of all position welds. Or the welder can hold the TIP TIG torch and weld like a MIG weld.
Again take a moment with the above video to examine the untouched stainless weld surface quality. Carefully examine the silver weld color, (lack of oxidation) attained that’s a benefit of EN polarity and increased weld speeds that result in the lowest possible weld heat input. Also then examine the weld fluidity continuity on the weld surface and toes, that reflects on the high weld energy attained. Note with the extremely small HAZ produced, a benefit weld shops can anticipate with any stainless welds, therefore the lowest distortion should always be attained. And with some stainless grades, with this process, anticipate the least opportunity for carbide precipitation. Also note the respectable weld speed being attained, (as quick as MIG) , and in case anyone is interested also note in the video as well as the photo, no visible stainless, carcinogenic weld fumes.
2020: MY MESSAGE TO THOSE NORTH AMERICAN AND EUROPEAN WELD – METALS CODE / SPECIFICATION COMMITTEE MEMBERS THAT APPEAR TO BE STUCK IN A COMA DURING THE LAST DECADE: Of course it’s appropriate that weld process information and metal guidelines should be kept up to date by the major Code bodies such as ASME – AWS – API – ASTM – ABS – NAVSEA. Unfortunately these N.American Governing bodies and their engineer committee members are in 2020, now ten years behind the capability of a process such as TIP TIG.
- TIP TIG will dramatically change the recommendations and guidelines that have been provided in the last seven decades. From my perspective, when it comes to comparing the common arc weld process’s that account for most code welds, GTAW – FCAW and GMAW , the code providers are not aware that when TIP TIG is utilized, major changes will be enabled.For example;
- Preheat, inter pass and post heat treatments are typically dramatically reduced or no longer required.
- Weld groove preparation dimension recommendations can be dramatically reduced. For example from the typical Vee-grooves of 60 plus degrees, to 40 to 50 degrees.
- Costly NDT weld inspection requirements should be reduced or elminated.
- There will be less concern for HAZ changes, impact properties will dramatically increase.
- There will be less concerns for cracks, stresses and distortion.
- There should be minimal concern for Carbide Precipitation or other corrosion issues.
- In clad welds, the weld layers can be reduced as a result of less alloy loss.
- Many Titanium welds will not require trailing shields.
Yet all I have heard since I introduced TIP TIG to N.America in 2009 is SILENCE. Which is again a reflection of where we are as an industry.the
WHEN TIP TIG IS BOUGHT INTO THE WELD SHOP AND ALL WELDERS THAT USE THE PROCESS ARE PROVIDED WITH CORRECT TRAINING (SEE MY MY 3 HOUR TIP TIG SELF TEACH / TRAINING PROGRAM) IN MY TRAINING RESOURCES, MANAGERS SHOULD EXPECT THE FOLLOWING BENEFITS?
- TIP TIG enable the best possible, manual and automated all position, consistent arc weld fusion, with the cleanest welds with the lowest porosity, so informed plant engineers or mangers should expect NO WELD REJECTS OR REWORK on any metals and code quality applications.
- TIP TIG provides optimum automated weld capability without arc length sensitivity concerns that are common with the Hot Wire process, so simply connect that TIP TIG torch to a robot, a carriage or rotary positioner.
- TIP TIG is the easier to use than the TIG – GMAW – FCAW process on all position code welds, and also enables the best possible root and fill weld quality. So on most pipe welds or welds with roots, instead of using two weld processes with TIP TIG you have one process that’s suited to any gauge, any thickness, or any size.
- TIP TIG produces code welds without spatter, and welds with the lowest oxidation that should not require grinding or cleaning.
- TIP TIG also enables the lowest possible weld fumes. If you weld any metals that have fumes or grinding dust that you don’t want to subject your employees to, you now have a weld process solution.
- TIP TIG always provides the lowest possible welded part heat input, the least distortion, the lowest weld stresses, the best possible mechanical and corrosion properties, and that applies to all metals.
Take another moment with the close up of the TIP TIG arc and weld.
- Note below the vert up, continuous highest possible arc weld energy, enables from increased DCEN current from higher deposition and smaller filler wire capability, and from the wire to plasma placement that enables full plasma coverage over the pool.
- Note the highest possible weld fluidity, a fluidity that is not inhibited by the already small fluid weld drop additions to the weld.
- Note the weld metal purity from the combination of highest arc energy capability protected by the inert atmosphere. Any weld person would know simply by looking at this weld that the weld would be defect free. This weld can not be duplicated with any Pulsed MIG or GTA weld.
Remember with any arc weld, the best possible code weld results will come from a weld process that provides FOUR prime weld functions;
- A weld protected by an inert atmosphere.
- An arc plasma that provides the highest weld energy.
- An EN polarity that enables a fast freeze weld making it easy to use for all positions.
- A deposition that enables good welds speeds in combination with an EN polarity that enables the lowest welded part heat input.
TIP TIP ENABLES SIMILAR VERTICAL UP WELD SPEEDS TO PULSED MIG. TIP TIG typically delivers 200 to 400% higher weld deposition rates than DC TIG and produces similar vertical and overhead weld travel rates as pulsed MIG. Another point, In contrast to traditional GTAW, both the DCEN & also Variable Polarity used for aluminum welds, TIP TIG continuously feeds the commonly used 0.035 – 0.045 (1 – 1.2 mm) diameter weld wires into the TIP TIG plasma sweet spot.
When TIP TIG is used on clean applications such as this Super Duplex fillet weld, note the untouched TIP TIG weld color which reveals lack of oxidation influence with the atmosphere. This is only possible with very low welded part heat input. With TIP TIG, weld shops should always anticipate the cleanest, defect free welds that produce the smallest weld HAZ, and this applies to most weld applications > 2 mm. Note try and replicate the fillet on on the left with either a duplex, stainless or inconel weld wire and the process of your choice.
CONSISTENTLY ATTAINING OPTIMUM UNIFORM WELD QUALITY & WITH THE LOWEST WELD COSTS, SHOULD BE OF INTEREST TO ANY GLOBAL WELD DECISION MAKER.
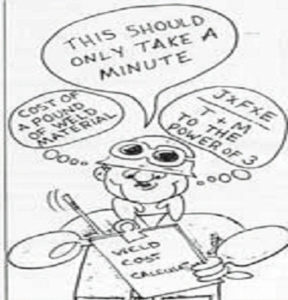
2019: I am aware that the technical weld process process details at this site may not get everyone as exited as I get when discussing TIP TIG versus the AC/ DC GTAW, Pulsed MIG, Gas Shielded Flux Cored and also the automated Hot Wire TIG, however most weld shops do have a great interest in two subjects WELD QUALITY AND COSTS.
With this in mind, I will start in the first following paragraph discussing some of the unique TIP TIG weld COST reasons that any company that is using DC TIG – MIG – Pulsed MIG or Flux Cored for code quality welds on steels, alloy steels, alloys and also specific AC TIG & MIG Aluminum applications, simply cannot afford to ignore.Please don’t forget that weld costs are of course influenced by weld deposition rates, weld rejects, weld rework, weld cleaning, by the welder’s skills, and by additional material costs or material handling.
Weld shops take note: The traditional arc weld processes such as AC/DC TIG, Pulsed MIG, Flux Cored or the SMAW process, require higher all position welder skills than required with TIP TIG.
As most in this business are aware, when hiring GTA welders;
[] the slow weld speeds and cost consequences,
[] the never ending weld start and stops ,
[] the many trips by the welders to the grinder to reshape and replace tungsten,
[] as GTAW welder skill requirements change from one welder to another, this and above have a major influence on both the GTA weld quality and the hourly labor costs generated.
If you were stand in any Aerospace plant and watch 5 TIG welders produce similar welded parts, and you will note that their different manual welder skills and weld practices are influencing the lack of GTA weld uniformity, continuity that results in the too often inconsistent weld quality attained,
THE FREQUENT TUNGSTEN CHANGES WITH TRADITIONAL DC TIG WELDS DO NOT OCCUR WITH TIP TIG :
As mentioned, DC TIG welders have to place their weld wire in front of the weld in a very small, fast freeze weld pool and often that wire or weld pool will touch and contaminate the tungsten, lowering the tungsten melt temperature and changing its required profile. The welder will then stop welding and replace their tungsten and create another weld start / stop which are common weld defect locations. When large amounts of AC/DC TIG weld are required, those tungsten changes will be very frequent. In contrast, the TIP TIG wire is fed to the side of the TIP TIG arc plasma and therefore its more difficult for the TIP TIG weld to contaminate a TIP TIG tungsten. Once this process is learnt correctly and especially the unique the TIP TIG Best weld practices the welder will likely have no more than one or two tungsten changes per shift.
SO LETS LOOK AT THINGS THAT INFLUENCE WELD DEPARTMENT BUDGETS WITH A CHANGE TO TIP TIG:
It would take me about an hour to prove the following statement. “In a weld shop that employs mostly DC TIG welders, with a change to the TIP TIG process, that weld shop should anticipate at least a 65 to 75% annual weld labor cost cost reduction in their weld department budget. As for those weld shops that utilize pulsed MIG or gas shielded flux cored on code quality weld applications, most of the weld shops will budget for weld rejects or weld rework. In contrast, with TIP the weld shop can anticipate no weld rework. The TIP TIG weld deposition and weld travel details that greatly influence weld costs are well documented at this site, however I want to get across both the the extensive weld costs savings potential and weld quality improvement impact with a change from regular DC TIG to TIP TIG and this applies to any company that provides Code Quality steels, alloy steels, alloys and also many aluminum weld applications.
The following info. provides how I attained an average of 70% hourly weld cost reduction with changing from DC GTA to TIP TIG.
DC TIG TO DC TIP WELD COST REDUCTION: Lets take a Fortune 500, Aerospace corporation that has many global plants that employ manual DC TIG welders for code quality weld applications, call it PLANT 1. This plants employs 10 DC TIG welders, five on each shift. The plant also employs two weld shop supervisors to manage the two shifts. The Aerospace TIG welders earn $30 /hr, and mostly weld steels and alloy steel code applications. This companies typical welder labor costs $60,000.00 / yr. The welders benefits are $8,000 / yr. Also as TIG is such a slow process, overtime is the norm. The average overtime per-TIG welder was 10 hours a week at time and a half, 10 x $45 hr = $450 x 50 weeks = ($22,500 / year). The annual TOTAL weld labor costs for the aerospace company is $90,500.00 per/welder x 10 welders. Also add two weld supervisors at $80,000 /yr, with the supervisor combined annual salary of $160,000.yr. The total weld labor cots for this Aerospace weld shop is $1,065,000. The TIG weld equipment investment for the 10 welding units, approx. $78,000.
COMPARE ABOVE PLANT 1 WITH WITH TIP TIG WELD LABOR COSTS IN PLANT 2:
Now for those still hanging in there, first thanks for your patience. The above aerospace company changes to TIP TIG. At PLANT 2, instead of the 10 DC TIG welders, all this company would now require to achieve the same weld production with superior weld quality , would be three TIP TIG welders and one supervisor working one ONE shift. Three TIP TIG welders wage plus benefits, 3 x $68,000 / yr = $204,000 / yr, plus one supervisor $80,000 / yr, producing a yearly TIP TIG WELD LABOR costs of $292,000. By the way with TIP TIG you would also reduce the annual argon TIG gas cost in the range of 50 to 70% , and also take approx. 15 – 30% of the weld wire costs. The TIP TIG equipment costs depending on the power sources available in the shop would be in the range between $50 to $80K. As you you can see with the added weld consumable savings, its easy to anticipate at least an annual TIG labor cost savings of 70% would be anticipated.
The above annual DC TIP TIG weld shop wages total is $292.000. The annual DC TIG weld shop wage $1,065.000.
A GTAW Weld Cost Question: Em, as weld deposition rates are a large factor in weld shop costs, can you provide more detailed info. on the typical average weld deposition rate capability with manual DCEN TIG welding?
Regular DC TIG Weld Cost Answer:
Welding a 3/16 horizontal fillet, the DC TIG manual welder on average would feed a common 3/32 steel or stainless TIG wire into the weld pool at approx. 8 inch minute, (20 cm/min). This wire feed rate delivers just less than 1 lb/hr with 60 minutes arc on time. Lets say the average arc on time per/hr for a TIG welder may be around 20 minutes delivering approx. 0.3 lb/hr.
If a TIG welder decided to try and feed a smaller 0.035 (1 mm) wire, with an 0.035 steel or stainless wire, the welder would require that the DC TIG welder continuously feed the 0.035 wire at around 70 inches per-min, (not going to happen with traditional TIG).
TIP TIG Weld Cost Answer: On the same weld, the TIP TIG welder would set an 0.035 wire feed rate of around 150 inch/min, approx 2.2 lb/hr, As TIP TIG increases the arc on time to lets say 30 minutes per-hr the TIP TIG welder is depositing 1.1 lb/hr, so you can see with this conservative TIP TIG setting the TIP TIG welder is putting in 200% more weld and depending on the weld application, the TIP TIG process will readily provide a 300 plus percent increase in weld than is possible with the DC TIG welder.
I HOPE YOU ARE NOW ALL WELL AWARE THAT TIP TIG IS UNTOUCHABLE FOR ALLOY WELDS, BUT WHAT ABOUT THE COST SAVINGS FOR A SIMPLE CARBON STEEL PIPES WELD APPLICATION?.
As reported by a TIP TIG user. Our customer ordered plain carbon steel pipe assemblies from the weld shop used in heating system. This was a first time that they had used TIP TIG for any welding application. The biggest pipe was 8 inch diam with a 1/4 wall.
With regular DC TIG it took around 90 minutes to complete the pipe welds from root to cap and this was done with 3-4 passes depending from the welding position. With TIP TIG the same pipe welds with made two weld passes and in 30 minutes. As for the weld quality, 100 % x-ray was used on the welds. With regular TIG this company would often find minor defects and with X-RAY evaluation pipe weld rework was common. In contrast with the TIP TIG welds there was absolutely nothing shown on the X-rays. The X-ray were taken with digital equipment so they were able to zoom in and check everything very precisely. So the weld shop attained far better quality, extensive increased production, and this was within the first two weeks of purchasing the TIP TIG equipment.
Note: Please keep in mind, that with all position code quality weld applications as in pipe and vessel plants will also employ Pulsed MIG welders. You may be surprised to know that the weld deposition rates for code quality vertical up and over head pulsed MIG welds are quite similar to the deposition rates attained by TIP TIG, however the pulsed MIG weld quality will be inferior with special concerns for the weld fusion, the weld heat, porosity and weld fume concerns. Of course for horizontal fillet welds the pulsed MIG process will enable dramatic deposition rate increase, but again with the quality, heat and fume concerns.
IMPROVED WELD CONTROL COMES WITH DRAMATICALLY REDUCING ALL POSITION WELDER SKILLS AND ALLOWING TWO HANDS ON THE TORCH:
If the above was welded with DC GTA, the welder would have one hand on the torch, the other hand to feed the wire, and maybe one foot on the amp control.
If the above was welded with pulsed MIG, apart from the inferior weld quality especially with the sluggish stainless, the MIG welder would have to deal with weld fumes and spatter.
- With TIP TIG code quality all position welds, and the rapid freeze characteristics influenced by the EN polarity, the weld pool is easy to control and the welder skills are dramatically reduced. Also one or two hands can be used to hold the TIP TIG torch and the TIP TIG welder does not require a foot amp control.
- Irrespective of a person’s background, the TIP TIG process is easy to learn in a few days, that is if the correct settings and best weld practices are taught, (available at this site). This is a process that will reduce the concerns for skilled welder shortages, and reducing welder skills will affect weld labor costs.
- Reducing welder skills also enables higher weld quality, especially when the weld shop employs more than one welder and wishes to produce uniform, consistent optimum manual weld quality.
- Don’t forget that the TIP TIG weld wire is continuously fed into the plasma arc sweet spot. This wire feed feature, drives consistent, uniform weld melt that enables consistent weld fusion, decreased weld porosity, and enables improved control of the weld travel rates.
- In contrast to a manual DC TIG weld, typically no more that two weld settings are required for the weld wire diameter utilized. And TIP TIG weld arc starts and stop parameters are automatically controlled, to a weld quality level that will never be available with any TIG, Pulsed MIG or Flux Cored weld.
- With TIG welds, there are often many weld arc start / stops influenced by the manual wire delivery that affect both weld quality and productivity, solution provided by TIP TIG.
- Instead of using DC TIG and then adding another weld process to complete the welds, such as TIG and Pulsed MIG, with the TIP TIG process, the weld shop requires one weld equipment package, one weld wire, one gas for any pipe root to fill, or for any all position welds on any metals, and on welds with any thickness. One process one skill set.
Of course many welds don’t require the TIP TIG process: If welds are made on parts in which “internal” code weld quality evaluation is not required, or on parts with mill scale, coatings and contaminates in the weld area, then MIG and flux cored would be a more appropriate weld process choices. However if they are not code quality welds and if weld spatter, weld cleaning or weld fumes is a concern, consider TIP TIG.
PIPE ROOT WELD OPTIONS: Three decades ago, I manged a pipe weld project, training Imperial Oil, (Exxon) union pipe welders, Tar Sands Alberta Canada. Left, Ed checking the MIG root weld issues generated with with different MIG weld transfer modes.
Imperial Oil was looking to create dramatic Nat Gas pipe line weld cost reductions, and I was contacted to first train the “we love our SMAW weld process” sub-contractor, manual pipe welders on how in the 5G pipe position, for pipe root welds to use the semi-automated Lincoln MIG STT process, (in reality a simple low pulsed MIG mode), and also the Miller RMD (reduced SC current) process. And for their shop welded rotated pipe joints, teach the welders the process controls – best weld practices with the conventional MIG Short Circuit mode.
After the 5G Exxon pipe welder root training, I provided the same welders gas shielded flux cored process control – best practice, 5G pipe fill pass training. At that time, the Oil & Nat Gas industry did not have an extraordinary pipe weld process such as TIP TIG which was all they would have required for root and fill passes. And its perhaps a reflection of the general weld engineering apathy found in the Oil – Nat Gas industry, that in 2020, ten years after I introduced TIP TIG to N.America and Australia, that most weld engineers and relevant managers in this industry, still know little about the TIP TIG process.
On a pipe projects like the above, if the welders used TIP TIG, they would have;
- only required one weld process for all root and fill passes,
- only required one gas,
- only required one weld wire,
- only required one weld procedure with two simple weld settings.
- have had the ability for zero weld rework.
- would have attained the highest possible impact properties, a necessary requirement for Alberta.
WELD REALITY: The most popular Semi-automated MIG process for Pipe Root Welds is MIG. First it was MIG Short Circuit, followed by MIG STT and MIG RMD, for the root, and then another process such as flux cored or pulsed MIG for the fill passes. The reality is no other arc weld process can compete with TIP TIG in terms of capability and quality on code quality welds.
Linclon MIG STT Left – Miller RMD right. Both attaining acceptable 5G root, vert down weld results. If I had to GMA a pipe root today I would use an OTC pulsed unit.
Ed Training Exxon / Imperial Oil pipe welders on the different MIG weld transfer modes available to weld Nat Gas Pipe. Pipe weld shops need to be aware that when they use MIG Short Circuit for rotated pipe root welds, or use MIG STT or MIG RMD for the all position pipe root welds, in contrast to TIP TIG they are using inferior arc weld processes that are not only sensitive to wire stick variations, but also sensitive to root weld gap and root alignment variations. That sensitivity is not part of the TIP TIG process
Pipe, plate, vessel, valve, tank welds when the best possible weld quality is required, from the root welds to the fill passes, TIP TIG would always provide all position fill weld passes with superior mechanical or corrosion weld / part properties, and all the QA department would have to do is document the passed welds.
What about Gas Shielded Flux Cored Welds? There are many reasons why an experienced weld engineer should be nervous about allowing gas shielded flux cored welds on code quality applications in which the internal quality of each weld is closely evaluated. And there are many reasons why the weld shop should not be surprised on any code quality all position welds, when the flux cored welds that are made by a highly skilled welders looks like this.
The Gas Shielded E71T-1 Flux Cored process does not need a welder to be responsible for generating weld defects.
If you are aware of the weld process controls and best weld practices associated with Gas Shielded Flux Cored, (as taught in my process control programs), you would know what was the prime cause of the common issue.
With code quality welds, and the traditional arc weld processes, such as flux cored, pulsed MIG and SMAW, there are many reasons beyond the welders control, why managers, engineers and supervisors cannot get a good nights sleep.
MOST EXCELLENT LOOKING MIG FILLET WELDS, WHEN MACRO EXAMINED, WOULD REVEAL MARGINAL SIDE WALL WELD FUSION
What makes TIP TIG a superior weld process than Pulsed MIG or Gas Shielded flux cored for vertical up and over head welds?
An easy way to explain why the Reverse Polarity MIG and Gas Shielded Flux Cored process will often leave welds with lack of weld fusion, especially with vertical up and overhead welds on parts > 5 mm thick. Both MIG and gas shielded flux cored arc temperatures are almost 50% of a DC TIG weld. And with the Reverse Electrode Positive MIG and flux cored welds in which most of the arc energy plasma is used to melt the continuous fed weld wires, they simply do not have the required weld energy for the welds the weld mass delivered, and the weld deposition rates delivered that influence the weld travel speeds generated which influence the weld solidification rates. The bottom line is MIG and flux cored cannot generate the weld fluidity that’s created by a DC Electrode Negative TIP TIG weld.
As for weld purity which influences weld porosity and oxidation buildup, both MIG and flux cored use reactive gases such as CO2 and Oxygen which add to the weld porosity formation. And when gas shielded Flux Cored is selected for code applications weld shops should be aware that with this process, there can never be a guarantee of not getting trapped weld slag, worm tracks influenced by moisture and excess porosity. When you add the common weld defects found with flux cored or MIG, along with the concentrated weld heat around the weld wire tip influenced by reverse polarity, you will have questionable weld quality results and also welds that have large weld heat affected zones. Therefore, when it comes to code welds, the semi-automated MIG and flux cored weld processes simply cannot compete with the semi-automated TIP TIG process.
Note: Be aware that the typical increase in weld deposition rates that are attained from TIP TIG, the weld shop, typically will provide all position TIP TIG travel rates that are similar to those attained with pulsed MIG process. |
TIP TIG is not simply the evolution of TIG welding, for code quality welds, it's the evolution of all arc weld processes. For those weld decision makers that are awake during Covid 2020, welcome to the now 13 year old, TIP TIG process.
NOTE UNDER EDIT……..In the above video, you could ask yourself the following questions.
- Why is this super hot looking stainless weld silver in color, what happened to the oxidation on these thin parts?
- Why is the weld so hot yet the Heat Affected Zone (HAZ) is so small?
- How is that spatter free, 1/4, (6 mm) TIP TIG fillet weld being made at a weld travel rate more in common with a pulsed MIG weld?
- For those aware of the hazards of carcinogenic weld fumes generated when welding stainless chrome alloys, where are the fumes?
In an advertisement that I produced for TIP TIG USA, the USA company that my partner Tom O’Malley and I founded around 2009, I called TIP TIG “the EVOLUTION of TIG”. However while examining the TIP TIG process on a wide variety of weld applications over the next 11 years, the weld reality with this unique weld process as you will read at this site, is that TIP TIG is much more than an improved versions of the DC/AC GTAW and the Hot Wire GTAW process.
FOR THE FIRST TIME IN 60 YEARS WE HAVE GONE FROM TWO TO THREE SEMI-AUTOMATED ARC WELD PROCESSES. Since the 1950’s, there has only been TWO SEMI-AUTOMATED cost effective arc weld processes available to the global weld industry, GMAW and Flux Cored. And the reality is with approx. 70 years of process and equipment development, both these processes as you will read at this site cannot be relied on to consistently produce welds subject to X-Rays, that will not require weld rework. Around 2009 in N.America, things changed, I introduced the semi-automated Plasch invented TIP TIG process to N. America.
Here we have a 2020, TIP TIG unit connected to a Miller Dynasty 400 amp TIG power source. Miller proudly claimed that with it’s use of sophisticated electronics in the Dynasty, that they were proud to announce to their customers who did TIG welds with the Dynasty, that in contrast to traditional DCEN TIG equipment, weld shops MAY anticipate around a 17% increase in hourly TIG weld productivity.
However when a TIP TIG Wire Feeder and Hot Wire power source is added to that Miller Dynasty unit, not only does the weld shop dramatically reduce the required TIG welders skills, they should also anticipate with the TIP TIG unit at least 200 to 400% more weld each hour. Also for the first time, the weld shop will attain the weld heat dissipation benefits of DCEN polarity, along with the numerous weld quality and metallurgical benefits that result. NOTE
For 70 plus years, we only had two practical semi-automated weld processes, GMAW - FCAW, however if the best weld quality was required we turned to traditional GTAW.
Two big developers of GTAW equipment in the 1950’s – 60s, Union Carbide & Westinghouse.
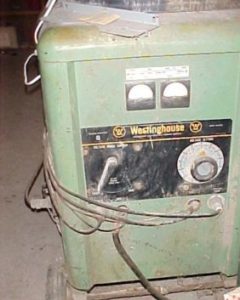
It’s a weld reality that with the above old DC TIG weld equipment, or with the 2019, DC TIG weld equipment shown below, the weld shop would produce similar DC weld quality and productivity. Of course the 2019 TIG welder is now using an Inverter power source loaded with electronics that could enable DC pulsed frequency, however this equipment also makes these type of power sources less durable, and more costly to repair. Lets face it, the modern day welder below looks good with his fancy gloves, jacket and weld helmet, however the reality for weld shops, is as they have been aware for approx. 70 years, that the AC/DC TIG process, when used on code quality welds would provide the best arc weld quality, while also requiring the highest arc welder skills and producing the lowest weld deposition rates. Those deposition rates also produce slow weld speeds that will influence the welded part properties.
2019 GTAW (TIG)
YOU ARE GOING TO READ SOME REMARKABLE UNIQUE WELD FACTS AT THIS SITE , AND IN THIS INDUSTRY WHERE BOVINE FECAL MATTER IS THE NORM, THE WELD EXPERTISE, EXPERIENCE AND APPLICATION DIVERSITY OF THE MESSENGER SHOULD BE HIGHLY RELEVANT TO THE READER.
Hello my name is Emily Craig, used to be Ed, but with a few plasma cuts I finally am where I belong. Many of you will know me by my twenty PLUS year weldreality.com web weld blog, or perhaps you were one of thousands that attended my MIG and flux cored weld process control seminars in the 1980s. Maybe you were one of the 80,000 readers of the “Weld Design & Fabrication” magazine in which each month for almost 20 years, you read the monthly Weld QA column that I wrote. And for those of you that have a “Machinery Handbook” gathering dust on your shelf, I wrote the weld section, and was also the key technical writer of AWS MIG Specifications.
As a weld engineer, who has specialized in Weld Process Controls – Best Weld Practices for more than 5 decades, I spent the last 40 years working in 13 countries, in hundreds of weld shops resolving weld quality and productivity issues. As for understanding weld equip. as a weld product and weld training manager with Airgas – AGA – Praxair – Liquid Carbonic, and the N. American Welding Manager at ABB Robots, I spent decades doing arc weld process, consumable and weld equipment evaluations from the world’s leading weld equip. and consumable companies.
For decades, my focus has been on the simplification of arc weld process controls and the best weld practices required for arc weld process optimization. Some of you will have one of my three books on the subject, or purchased my low cost self teach / training resources on the requirements of weld process controls – best practices. I believe that this focus and my 50 years of hands on experience in over a 1000 weld shops, provides me with the expertise and capability to critique the global weld industry, and to point out the unique attributes and detriments of each arc weld process, and how each of the common arc weld processes compare with the TIP TIG process.
Manual, automated or robot welds, my process control training programs enable weld shops to provide the best possible weld quality at the lowest weld costs, and provide the resources front office weld decision makers need for weld process ownership, plus eliminate the need for weld personnel to play around with weld controls with Manual MIG – Robot MIG – Gas Shielded Flux Cored – Advanced TIG, and now also now on the TIP TIG weld process.
TO UNDERSTAND TIP TIG, WE FIRST HAVE TO BE AWARE OF THE ISSUES WITH THE TRADITIONAL DC GTA PROCESS.
TO IMPROVE THE IMPORTANT DC GTA PROCESS, THERE HAD TO BE MAJOR CHANGES AND IT TOOK MORE THAN SIX DECADES TO ACHIEVE THAT CHANGE .
Poor utilization of the traditional high temperature DC GTA plasma.
The traditional DC GTA ARC. Note the arc requirements to melt the oversize TIG wire, and also the GTA plasma energy distribution required to melt the tip of that wire and maintain to weld pool.
As DCEN TIG for approx, 75 years has provided the best manual arc weld quality for steels and alloys, it’s understandable that few weld decision makers will have given consideration to the DC or AC GTA weld issues generated by this important weld process.
The DC/AC TIG manual requirements to feed the lengths of weld wire into a short arc length, small rapid freeze weld area, influences the weld current capability and the wire melt energy and uniformity and continuity which of course will influence the weld quality, weld consistency attained between different TIG welders that are welding the same products. The manual feed requirements also will influence tungsten contamination and wear.
Many DC TIG manual welds, will as a result of the weld wire lengths utilized, have the weld requirement for frequent weld start and stops, which are common code quality weld defect locations. The starts / stops and very low deposition rates that result in very slow TIG weld speeds greatly influence the welded part heat input.
With the deposition rates attained, the DC TIG process has from a weld cost perspective, been poorly suited to many common global weld applications that required a good amount of weld metal.
The poor TIG deposition rates have on many weld applications, resulted in the requirement of an additional, inferior, secondary weld process such as SMAW, Flux Cored or Pulsed MIG to also be utilized. With the DC/AC TIG application restrictions, the weld shop had to acquire additional weld processes / weld equipment, weld consumables, and required different weld procedures, welder skills and weld practices.
Low TIG weld deposition rates not only affects the weld speed capability, it also restricts the TIG weld current capability for the weld which apart from affecting the weld fusion and weld porosity, also influence the arc length sensitivity that would often become especially notable with automated TIG applications.
The high TIG welder skill requirements, and the low TIG weld deposition rates, typically create the highest Weld Labor Costs.
- The DC TIG process can often be “arc length sensitive,” adding to the manual welder skills and as mentioned making TIG poorly suited as a semi-automated process. If used with automated welds that require filler metal, TIG will often require costly, automated arc length correction equipment.
Carefully Examine the Traditional DCEN TIG Weld and Plasma Functions.
For almost 65 years, on most manual welds, the DCEN TIG process, has never been able to fully utilize it’s full energy potential from it’s high temp. arc plasma, therefore this process rarely enabled benefits that could have been attainable from the Electrode Negative Polarity Conductivity capability.
Examine the typical DCEN TIG weld as the large TIG weld wire is fed into the bottom portion of the plasma close to the weld pool. When melting the large TIG weld wire, as the wire gets close to the outer plasma, the wire tip melts and the DC TIG plasma is drawn slightly to the molten formation on the wire tip. The small fluid weld pool being generated by the restricted weld deposition attained is in reality a small “rapid freeze weld pool”. The DC TIG weld pool energy, and rapid weld solidification times, not only effects the TIG weld fusion potential and also porosity. The low deposition and restricted weld current also influences the weld arc stability and therefore arc length sensitivity. Take another close look at the above DC TIG plasma influence on the base metal, the weld, and the wire melt.
Three multi – functions of the traditional DCEN TIG plasma and filler metal reactions.
- REGULAR DC GTA. A portion of the traditional DC TIG plasma energy is being used to maintain the small fluid weld area behind the tungsten.
As DCEN TIG for approx, 75 years has provided the best manual arc weld quality for steels and alloys, it’s understandable that few weld decision makers will have given consideration to the DC or AC GTA weld issues generated by this important weld process.
The DC/AC TIG manual requirements to feed the lengths of weld wire into a short arc length, small rapid freeze weld area, influences the weld current capability and the wire melt energy and uniformity and continuity which of course will influence the weld quality, weld consistency attained between different TIG welders that are welding the same products. The manual feed requirements also will influence tungsten contamination and wear.
Many DC TIG manual welds, will as a result of the weld wire lengths utilized, have the weld requirement for frequent weld start and stops, which are common code quality weld defect locations. The starts / stops and very low deposition rates that result in very slow TIG weld speeds greatly influence the welded part heat input.
With the deposition rates attained, the DC TIG process has from a weld cost perspective, been poorly suited to many common global weld applications that required a good amount of weld metal.
The poor TIG deposition rates have on many weld applications, resulted in the requirement of an additional, inferior, secondary weld process such as SMAW, Flux Cored or Pulsed MIG to also be utilized. With the DC/AC TIG application restrictions, the weld shop had to acquire additional weld processes / weld equipment, weld consumables, and required different weld procedures, welder skills and weld practices.
Low TIG weld deposition rates not only affects the weld speed capability, it also restricts the TIG weld current capability for the weld which apart from affecting the weld fusion and weld porosity, also influence the arc length sensitivity that would often become especially notable with automated TIG applications.
The high TIG welder skill requirements, and the low TIG weld deposition rates, typically create the highest Weld Labor Costs.
- The DC TIG process can often be “arc length sensitive,” adding to the manual welder skills and as mentioned making TIG poorly suited as a semi-automated process. If used with automated welds that require filler metal, TIG will often require costly, automated arc length correction equipment.
Carefully Examine the traditional DCEN TIG Weld and Plasma Functions.
For almost 65 years, on most manual welds, the DCEN TIG process, has never been able to fully utilize it’s full energy potential from it’s high temp. arc plasma, therefore this process rarely enabled benefits that could have been attainable from the Electrode Negative Polarity Conductivity capability.
Examine the typical DCEN TIG weld as the large TIG weld wire is fed into the bottom portion of the plasma close to the weld pool. When melting the large TIG weld wire, as the wire gets close to the outer plasma, the wire tip melts and the DC TIG plasma is drawn slightly to the molten formation on the wire tip. The small fluid weld pool being generated by the restricted weld deposition attained is in reality a small “rapid freeze weld pool”. The DC TIG weld pool energy, and rapid weld solidification times, not only effects the TIG weld fusion potential and also porosity. The low deposition and restricted weld current also influences the weld arc stability and therefore arc length sensitivity. Take another close look at the above DC TIG plasma influence on the base metal, the weld, and the wire melt.
Three multi – functions of the traditional DCEN TIG plasma and filler metal reactions.
- REGULAR DC GTA…A portion of the traditional DC TIG plasma energy is being used to maintain the small fluid weld area behind the tungsten.
- REGULAR DC GTA… portion of the plasma energy in front of the tungsten is required at the leading edge of the weld pool to provide sufficient energy to fully melt the large molten filler wire tip.
- REGULAR DC GTA…An outer front portion of the DC TIG plasma energy is used to melt the tip of an over sized weld wire.
Note the typical DC GTA wire is a weld wire that is typically twice the diameter of a MIG wire. A large weld wire size that actually restricts both the weld current that could be used and weld deposition rates that could be attained.
MANY COMPANIES LOOKING FOR TIG WELDERS ARE SIMPLY NOT AWARE THAT SINCE 2010 IN N. AMERICA THE TRADITIONAL GTAW PROCESS REQUIRES UNECESSARY OBSOLETE HIGH WELDER SKILLS:
For the few rare weld supervisor, managers or engineers that visit this site, please note. The regular DC/AC TIG process, has for decades required the highest welder skills. Those TIG welders have to manually feed the weld wire and know when to feed and withdraw the wire. The TIG welder may be required to aggressively manipulate the torch, and sometimes at the same time operate a foot amp control.
GTAW HAS FOR DECADES BEEN POORLY SUITED TO AUTOMATION THAT REQUIRES FILLER METAL: As a result of the TIG short arc length requirements and resulting arc length sensitivity, and other TIG weld issues and limitations as discussed in this section, the regular DC TIG process would be poorly suited as a “manual Semi-automated” process, and poorly suited as a fully Automated arc weld process.
A portion of the plasma energy in front of the tungsten ensures the leading edge of the weld pool has sufficient energy to fully melt the molten filler wire.
- An outer front portion of the DC TIG plasma energy is used to melt the tip of an over sized weld wire.
Note this is a weld wire that is typically twice the diameter of a MIG wire. A wire size that has to be used for manual TIG, (discussed below). A large weld wire size that actually restricts both the weld current that could be used and weld deposition rate that could be attained.
GTAW IS USING UNNECESSARY HIGH WELDER SKILLS: For the few weld supervisor, managers or engineers that visit this site, please note. The regular DC/AC TIG process, has for decades required the highest welder skills. TIG welders have to manually feed the weld wire and know when to feed the wire. The TIG welder may be required to aggressively manipulate the torch, and sometimes at the same time operate a foot amp control.
GTAW IS POORLY SUITED TO WELD AUTOMATION: As a result of the TIG common arc length sensitivity, and other TIG weld issues discussed in this section, the regular DC TIG process is frequently poorly suited as a “manual Semi-automated” process, and poorly suited as a Fully Automated arc weld process on applications in which filler is required as there would be concerns for tungsten to work, arc length variations.
DC GTA PLASMA FUNCTION.. The traditional DC TIG arc plasma uses a good portion of the arc plasma energy in the task of melting the large diameter TIG wires. The balance of that DC TIG plasma is utilized in keeping the small, rapid freeze weld fluid. A large part of the welder skills required for GTA welds, is for the welder to be aware of when to move that weld wire in and out of the weld pool. The inconsistency of that wire feed timing and skill and the wire placement to plasma placement is one of the reasons for the frequent lack of GTA weld quality uniformity and consistency.
The reason large DC TIG weld wires are used, is welders could not feed smaller wires fast enough to attain a deposition rate advantage. The divided plasma energy distribution over the weld surface and weld wire, limits the weld deposition capability. The low DC GTA weld deposition rates are often around a 1 lb/hr or less and limits the GTA weld current potential per-application, and produces very low weld travel rates that add to the DC GTA parts weld heat input. These GTA process characteristics are the prime reasons the DC TIG process has for decades been highly restricted in it’s weld application potential.
WHEN THE COMPANY REQUIRES EXTENSIVE USE OF THE TRADITIONAL DC GTA PROCESS. When weld decision makers, select the DCEN GTA weld process, in 2020 they need to be aware that thanks to their weld management they are;
- requiring welders to use unnecessary high welder skills and practices, both of which influence weld quality, the weld uniformity and the weld labor costs,
- producing TIG welds that require unnecessary weld starts – stops, (typical defect locations),
- producing slow TIG welds that are providing unnecessary high welded part heat, an issue that affects distortion and mechanical – corrosion properties,
- when welding heat sensitive weld applications adding to unnecessary metallurgical considerations,
- using a process in which it’s difficult with a group of welders welding similar parts to create uniform welds,
- each hour ensuring that their welders are on average adding 200 – 400 % to their companies weld labor costs.
SO A REASONABLE QUESTION IN 2020 WOULD BE..
Why would managers select a weld process that requires higher welder skills, will produce inferior weld and part quality, and creates much the highest costs?
AFTER 70 PLUS YEARS, ITS TIME TO CHANGE THE WAY YOU THINK ABOUT CODE QUALITY WELDS.
I have been in many Aerospace, Defense and Medical companies that employed a group of DC TIG welders many making similar welded production parts. And the first thing I would often note on the weld shop floor, was apart from the usual, lack of management & engineering Weld Process Ownership, there also was a common LACK OF WELD QUALITY – WELD APPEARANCE UNIFORMITY on the production parts.
The common lack of GTA mfg. weld quality uniformity was greatly influenced by the fact that manual GTAW is not a Semi-automated weld process and the welder skills vary from welder to welder. Also what would be missing from not only the weld shop floor but also too often from the weld shop front office, was an evident lack of understanding or focus on the requirements for weld process controls and best weld practices.
The TIP TIG process was invented by Plasch in Austria.
In 2009, when I should have been thinking about retirement, I found the a process in Scotland called TIP TIG and while showing some development issues, during a 10 minute demonstration from my friend Darren, I instantly became determined to introduce the TIP TIG N. America. This was no easy task as in both the USA and Canada we had two countries highly reluctant to weld industry and weld shop process change.. I borrowed many dollars, and established TIP TIG USA in 2009 with my friend Tom O’Malley, and a year later Tom and I also introduced TIP TIG to both Australia and China
REGULAR DC TIG VERSUS TIP TIG FEATURE BENEFITS:
A summary of why TIP TIG is a unique arc weld process:
Craig Notes..10-2019: The patented “Plasch” TIP TIG changes in the weld transfer, allow TIP TIG to provide a unique “wire to weld placement” (view above) which enables many weld benefits and allows for “more weld energy” than has been possible with the traditional DC/AC GTA welds, or with any manual arc welds.
With traditional DC GTA welds, the required weld wire to plasma placement (left) is necessary to melt the required large DC TIG weld wire diameter, (1/16 to 1/8 is norm). This takes “extensive energy from both the DC TIG arc plasma and also away from the weld”.
Craig Notes 10-2019. In contrast to traditional DC TIG, note with TIP TIG (left) how the unique TIP TIG wire feed position at the top of the plasma, and the resulting unique plasma and weld attributes that with this process allow the use continuous fed smaller wire diameters providing higher weld deposition rates to melt in the upper portion of the outer plasma periphery. The unique TIP TIG wire to plasma placement enables most of the TIP TIG plasma energy to be distributed over the weld pool. Another contrast to DC TIG, is the TIP TIG process is depositing already molten weld drops into a now higher energy, more fluid weld pool.
Regular DC GTA
BY THE WAY, THE FREQUENT TUNGSTEN CHANGES WITH TRADITIONAL DC TIG WELDS DO NOT OCCUR WITH TIP TIG : As mentioned, DC TIG welders have to place their weld wire in front of the weld in a very small, fast freeze weld pool and often that wire or weld pool will touch and contaminate the tungsten, lowering the tungsten melt temperature and changing its required profile. The welder will then stop welding and replace their tungsten and create another weld start / stop which are common weld defect locations. The tungsten modifications or changes can be frequent. In contrast, the TIP TIG wire as noted below is fed to into the top of the TIP TIG arc plasma and the weld drops that detach will not make contact with the tungsten. Once the TIP TIG Best weld practices are learnt, the welder will likely have no more than one or two tungsten changes per shift.
Craig. Notes 10-2019. Take a moment to again compare the above regular DC TIG weld wire feed to the arc plasma position with the DC TIP TIG weld wire placement left. The unique TIP TIG small wire to plasma placement at the upper outer plasma periphery is enabling all of the high arc temp. plasma energy over the weld pool surface. The unique TIP TIG energy distribution action allows the TIP TIG arc electron flow to be enhanced and this can result in a wider, more dense, increased velocity plasma than that attainable with regular GTAW. Also with this plasma improvement a slightly longer open arc length is enabled and the traditional GTAW arc length sensitivity is eliminated. The GTA Arc Length Sensitivity has always been associated with both the regular DC/AC TIG manual welds, and also with the automated Hot and Cold Wire TIG process which due to this sensitivity have not been suited as a semi-automated manual process.
Craig. Notes 10-2019. Another major benefit from the TIP TIG plasma distribution over the weld which enables increased and Prolonged Weld Fluidity. This improved weld fluidity enables more TIP TIG Wire to be Fed into the weld pool. More wire then enables more weld current to be used further adding to the TIP TIG plasma and weld energy. The extensive changes to the traditional DC TIG plasma energy distribution and the TIG weld dynamics to be discussed further, dramatically adds to both the TIP TIG weld and part quality potential, and also greatly enhances the TIP TIG weld application capability.
Craig… 10-2019. As you will note at this site numerous weld benefits will be generated with this unique process, and another major weld shop benefit, is that with TIP TIG from root to fill any metals any thickness, TIP TIG will be easy to use both as a manual, Semi-automated Arc Weld Process, or with most weld Automation, including robotics, without the additional requirements for costly automated arc length sensing devices, as typical with the GTAW – Hot Wire and Cold Wire processes.
This is what makes TIP TIG UNIQUE.
So you now know that the continuous fed TIP TIG weld wire is fed through a set of patented wire feed drive rolls that go back and forth with a rapid velocity and this makes the wire vibrate. Why is it important for the wire to vibrate.
Craig Note.. 10-2019: The patented TIP TIG weld wire vibration, (like a plucked guitar string) in combination with additional energy in the wire delivered from an AC Hot Wire power source that preheats the weld wire to around a 1000F, which creates a unique semi-automated arc process combination that enables both the rapid small weld drops to form and then rapidly shake off and transfer into an agitated weld pool.
Craig 10-2019: The wire vibration and resulting numerous agitated weld drops create a slight weld pool agitation that can add micro seconds to the fluid weld solidification time which allows more wire to be delivered to the pool and therefore allows more weld current to be used for the weld.
IN A WELL MANAGED WELD SHOP, EACH ENGINEER, SUPERVISOR AND MANAGER INVOLVED WITH WELD DECISIONS WOULD UNDERSTAND WITH THE PRIME WELD PROCESSES UTILIZED, THE REQUIREMENTS OF WELD PROCESS CONTROLS – BEST WELD PRACTICES THAT ARE NECESSARY FOR WELD PROCESS OWNERSHIP AND WELD QUALITY & PRODUCTIVITY OPTIMIZATION.
AND WHEN THAT RARE NEW WELD PROCESS OPPORTUNITY COMES ALONG TO FURTHER IMPROVE WELD / PART QUALITY AND DRIVE DOWN WELD COSTS, THESE INDIVIDUALS WOULD FIRST PROVIDE THE JUSTIFICATION, AND THEN IMPLEMENT THE CHANGES, AND PROVIDE THE TRAINING.
UNFORTUNATELY TOO MANY WELD DECISION MAKERS IN FORTUNE FIVE HUNDRED COMPANIES ARE WHEN IT COMES TO WELDING STUCK IN THE 20th CENTURY:
Someone should put the above advice on the notice board of every Defense, Aerospace , Power , Oil and Medical Equip. company in N.America.
At a time when TIP TIG was available, the shipyard designers, managers and engineers who made the costly decision to use DC TIG for their Titanium pipe welds produced during construction of a recent, US Aircraft Carrier, were in reality, well in sync with the Navy, who every year manages to pay contractors hundreds of millions of dollars on unnecessary weld-rework and labor costs. This sad engineering approach has in Navy Ship Yards gone on for decades, and in 2020, the majority of defense contractors are using a 20th Century, apathetic approach to much of their arc welding and fabrication, an approach that reveals the too common front office lack of capability for front office weld process ownership.
OVER FIVE BILLION DOLLARS ARE LOST ANNUALLY ON WELD QUALITY AND PRODUCTIVITY ISSUES, THAT WITH WELD PROCESS CONTROL EXPERTISE COULD EASILY BE ELIMINATED. BY THE WAY THAT’S EXPERTISE THAT GLOBAL COLLEGES AND UNIVERSITIES DON’T TEACH TO TECHNICIANS AND ENGINEER STUDENTS.
We are all likely aware of the unnecessary hundreds of millions of dollars lost annually in large ship yards due to poor flux cored and MIG weld quality and productivity issues, or the never ending robot MIG problems in most global auto / truck plants. However, it’s also a sad weld reality that in 2020, the majority of Defense, Aerospace, Oil and Power industries that are more than well served by mechanical and weld engineers, are in 2020, likely utilizing the 1946 GTAW process. A process that requires the highest welder skills, produces the lowest weld productivity, and to often on heat sensitive weld applications, puts in too much weld heat into the parts.
Above. From a weld engineering perspective, DC TIG welding was an inappropriate and outdated approach for this Navy Ship Building yard when it was selected to weld this Titanium and other pipe welds on a 21st Century US Aircraft Carrier.
2009: Chinese National Oil Company. when it comes to welding, a decade ahead of N.American – European Oil / Nat Gas companies.
After I introduced TIP TIG to CNOC in 2009, their engineers and managers quickly embraced the process Above in 2009, two Chinese National Oil Company TIP TIG welders producing Inconel and steel Sub-sea pipe welds, and in reality attaining a weld quality and productivity simply not possible from Pulsed MIG or DC TIG. (discussed below). Here we are in 2020, eleven years after I introduced TIP TIG to N.America, in the common “why change the way we have always done it” Defense, Aerospace, Oil and Power company weld shops, too many engineers and managers continue to use for their pipe, vessel and plate groove code quality welds, outdated or inferior weld procedures and out dated inferior weld processes such as TIG, Pulsed MIG of FCAW.
WAKE UP AMERICA….I ALWAYS FOUND IT IRONIC THAT AFTER GOING TO GREAT RISK, HASSLE AND EXPENSE I COULD NOT AFFORD, TO ESTABLISH THE TIP TIG PROCESS IN THE USA AND AUSTRALIA DURING 2009, THAT THE FIRST COMPANY TO RESPOND AND PLACE AN ORDER, WAS ONE OF THE LARGEST OIL COMPANIES IN CHINA.
In contrast to Pulsed MIG and Gas Shielded Flux Cored, TIP TIG is an expensive process yet it also is a semi-automated process, and as with any weld process selection, requires logical weld quality – weld productivity and weld cost justification. As for TIP TIG cost versus TIG welder costs, if it takes three TIG welders to do the work of one TIG welder, well even Donald Trump could figure out the annual cost savings produced.
Keep in mind that for decades in the weld industry, there has been only two semi-automated arc weld processes. Since 2009, there are THREE Manual Semi-automated weld processes for weld shops to consider for code quality welds, TIP TIG, MIG and Gas Shielded Flux Cored. Anyone that considers the Self Shielded Flux Cored process suitable for code quality welds, has from my perspective been listening to misinformation from a salesman or been guided by the screwed up and inappropriate FEMA recommendations.
All weld shops need to be aware that in 2020, there is no MIG weld mode or flux cored wire, (as shown at this site), that will ever attain the all position weld quality capability, or the welded part metallurgical properties on all metals that can be attained by TIP TIG.
The following are the specific weld applications that I recommend TIP TIG be considered for. Consider TIP TIG when;
- all position, code quality welds are required,
- the welds require open roots and fill passes that are subject to internal weld quality NDT,
- the welded parts have concerns for distortion,
- the welds have a special concern about the weld fusion or porosity.
- the welds are on alloys, alloy steels and high strength steels,
- the welds and parts require specific mechanical and corrosion properties,
- the welds have preheat – inter-pass temp. or post heat requirements, that could now be reduced or eliminated,
- it’s highly cost beneficial if reduced groove weld dimensions are possible,
- weld fumes are a concern,
- welds are being produced in which grinding and cleaning need to be eliminated.
Please remember that the semi-automated or full automated TIP TIG system is also when required an AC/DC TIG unit. So when TIG is required for example weld a very thin application 0.010, the welder can just shut the TIP TIG wire feed and hot wire unit off, and TIG weld the part.
Note Ref Alum. Welds: If wire feed ability is not an issue as with the > 0.046 5XXX series aluminum wires, TIP TIG using the Balance Wave, 80 – 90% EN – EP, variable polarity, will with the faster welds TIG speeds enabled, lower weld heat to levels never before attained and create aluminum welds with much higher welded part strength and lower weld porosity than has ever been possible with a TIG or Pulsed MIG weld.
SO, HOW LONG DOES IT TAKE TO TRAIN SOMEONE TO USE THE TIP TIG PROCESS? Most pipe welders would consider a fixed pipe open root, as the most difficult part of the pipe weld. So with TIP TIG, you would show the person who wants to do what any TIG welders would do on a pipe root and that is walk and weave the ceramic Cup across the pipe groove surface. But in contrast to regular TIG. No feeding a weld wire and no foot control required. With TIP TIG, reduced weld starts /stops and the welder will provide a manual pipe root weld continuity never before attained.
SHORT ALL POSITION PIPE OR PLATE TRAINING TIMES IS SOMETHING THAT ALL GLOBAL WELD MANAGERS DEALING WITH CODE WELDS SHOULD GET EXITED ABOUT: If the pipe welder using TIP TIG is used to DC TIG welding, all position, open root pipe welds, it would takes one to two days to learn the required TIP TIG best practices and settings as provided in my TIP TIG program. However something that should bring joy to those managers who have unnecessarily been keep complaining over the last decade how difficult it is to “find skilled TIG welders”. It would take someone again using my TIP TIG training program about eight to ten days to train a person Who Has Never Welded to become a TIP TIG weld expert, and to be able to pass any code, (including ASME) all position, Pipe Welder Qualification Tests.
I am well aware that at most of the Fortune 500, high tech. Defense, Aerospace, Power, Oil and Medical corporations, that you will usually find minimum understanding in the engineering office on the weld quality – cost benefits attained with weld process controls and on best weld practice expertise. This lack of process control awareness is mostly responsible for the general global lack of front office weld process ownership and the daily weld quality, rework, rejects and unacceptable weld production costs. By the way any manager or engineer that believes in the importance of engineering evolution, should take a look at the dates of the weld procedures and specifications that they daily use, and wonder why as we get close to 2020 that their company is still likely using Weld Procedures & Specifications that were generated in the 20th century.
JUST ABOUT EVERY WELD TRAINING DEPARTMENT AND COMMUNITY COLLEGE WELD PROGRAM THAT I EVALUATED IN THE LAST FEW DECADES WAS STUCK IN A 1970s TIME WARP. IF COMPANIES WANT DRAMATIC WELD QUALITY IMPROVEMENTS AND COST REDUCTIONS, THEY SHOULD AT LEAST WONDER WHY THE EXISTING WELDER TRAINING PROGRAMS RESULT IN WELDERS OR WELD DECISION MAKERS “PLAYING WITH WELD CONTROLS” AND WHY FEW WELDERS OR FRONT OFFICE WELD DECISION MAKERS LACK THE ABILITY TO MAXIMIZE MIG AND FLUX CORED WELD WELD QUALITY AND PRODUCTIVITY FROM WELD PROCESSES THAT HAVE CHANGED LITTLE SINCE THE 1960s.
Note: My easy to learn TIP TIG – Manual and Robot MIG and Flux Cored, Self Teaching / Process Controls – Best Weld Practice Training programs require approx. 15 hours. These are a great tools to train yourself or those employees that for decades think its normal to “play around” with their weld controls. Please be aware that its no good purchasing a new process such as TIP TIG and then have weld personnel that are not aware of how to get the best possible weld results on the numerous weld applications that TIP TIG should be used on.
It does not matter how experienced weld personnel are, all weld personnel will benefit from training programs that enable process optimization. To get immediate and dramatic weld quality – cost benefits from the TIP process, and to avoid weld personnel playing around with the TIP TIG weld controls, consider spending a couple of hundred dollars and get the world’s best TIP TIG + ADVANCED TIG – OR MY MANUAL & ROBOT MIG and FLUX CORED self teach / training programs.
Em’s TIP TIG + Advanced TIG. – Manual – Robot MIG – Flux cored, Weld Process Controls & Best Weld Practice, Self Teaching / Training Programs.
SpaceX, while rapid evolution in rocket technology, it was slow evolution in their weld engineering technology.
Some are slower than others. SpaceX first learnt about TIP TIG around 2009, it then took their engineers and managers ten more years to figure out that this was the arc weld process that would give them the best opportunity to consistently pass the NASA destructive tests for the Falcon rockets.
Evaluating the weld quality / productivity, semi-automated TIP TIG process benefits, as Elon Musk and his SpaceX managers / engineers eventually discovered, is not Rocket Science. With this process any weld shop will quickly find out that TIP TIG;
- will in contrast to the other arc weld processes, show that all position welder skill requirements are dramatically reduced,
- will always produce superior weld quality with improves weld uniformity and consistently,
- will show that inter-pass temperatures are typically not required, and pre-heat and post heat will often be eliminated or reduced.
- will show that distortion issues are no longer a concern,
- will reveal on all metals that weld & part cracks no longer concerns,
- will show no weld porosity concerns,
- will reveal no weld fume concerns,
- will eliminate weld rework,
- will in contrast to DCEN TIG, on average, enable 200 – 400% more weld each hour,
- will on all position welds produce weld speeds that are compatible with the inferior pulsed MIG process.
THE GLOBAL, MANAGEMENT AND ENGINEERING INDUCED NONSENSE ABOUT THE SO CALLED “SKILLED WELDER SHORTAGE” HAS FOR DECADES BEEN SIMPLY RIDICULOUS, AND UNFORTUNATELY ITS SIMPLY BEEN ANOTHER INDICATION OF THE GENERAL FRONT OFFICE MANAGEMENT AND ENGINEERING LACK OF WELD PROCESS OWNERSHIP CAPABILITY.
So here we are in 2020, and as they have done for decades, those managers and engineers that lack the ability for weld process ownership with ARC weld processes that typically have one or two controls, will be found in welding magazine articles complaining about their inability to find “skilled TIG welders”. Yet the reality is that thanks to TIP TIG, the traditional TIG weld skills have been redundant now for more than a decade. And for those apathetic managers and engineer who can’t find skilled MIG and flux cored welders, read below or visit www.weldreality.com
Common comment in many global weld shops
2020.. In the “why change the way we have always done it” Aerospace, Defense, Power and Oil industries, you will find with the majority of facilities that weld are still stuck in the 20th Century using traditional GTAW as their prime arc weld process. This is a process that requires the highest welder skills, provides the lowest weld deposition rates and produces high welded part heat input. This is an indication of what?
Welders don’t typically advance weld technology, but weld decision makers should.
2020. IT’S NOT JUST ABOUT THE N. AMERICAN LACK OF GLOBAL WELD SHOP AWARENESS OF THE 10 YEAR OLD TIP TIG PROCESS, IT’S ALSO THE GENERAL LACK OF ENGINEERING AWARENESS OF WELD PROCESS CONTROLS AND BEST WELD PRACTICES.
In the last decade, two of the companies that I provided MIG and flux Cored process control training employed approx. 700 weld personnel. Many of the weld personnel had limited weld experience, and the majority with weld experience played around with their weld controls and were mostly using poor weld practices. One training program I provided occurred in a USA. ship yard that made oil tankers and container ships. The other training program was for a company that built rail road tankers for transporting oil. These two industries had something in common in that they both used gas shielded flux cored and MIG. In both facilities, I required less than 7 days to enable over 200 “none welders” to meet the ship yard ABS ceramic backed, and the rail road companies AWS steel backed, all position, Gas Shielded Flux Cored welder qualification tests. For those that had weld experience it took my one day program for these personnel to learn the requirement for weld quality – productivity optimization.
Note: Above Photo. Myself in blue sweater in the rear, and my friend Tom, (blue right), training ship yard welders in something that in reality has for decades, been a missing link in most global ship yards. Weld Process Controls – Best Weld Practice Training. This training has little in common with the usual ship yard welder training program. Its a program that enables the participants, the weld process controls – best weld practice expertise, so when they walk up to a MIG power source, they can instantly, (without playing around) set optimum FCAW or MIG parameters, and then use the required best weld practices to produce welds that would ensure minimum weld rework and welds with maximum weld production.
For those interested. My weld process controls – best weld practice self teach / training resources are applicable to MIG – Robot MIG- Gas Shielded Flux Cored, GTAW / Advanced GTAW and now also the TIP TIG process. link here, https://weldreality.com/weld-training-resources/
TO UNDERSTAND THE POSITIVE ATTRIBUTES OF TIP TIG, WELD DECISION MAKERS SHOULD FIRST UNDERSTAND THE NEGATIVE ATTRIBUTES OF THEIR DC/AC GTAW PROCESS.
Now take a close look below at the semi-automated TIP TIG process. First examine the arc, plasma and the unique continuous fed weld wire delivery features that will be discussed below.
There are numerous weld benefits derived from using the Semi or Automated TIP TIG process:
FOR MANY DECADES, TWO SEMI-AUTOMATED WELD PROCESSES HAVE BEEN COMMONLY USED ON CODE QUALITY WELDS.
The two most utilized, Semi-automated arc weld processes used on Code welds, have been the EP, reverse polarity GMAW (MIG / MAG) and the Gas Shielded Flux Cored process. With these two weld processes, once three simple weld parameters were learnt, (to learn, visit my MIG – FCAW self teach / training process control resources) per wire diameter used, the optimum wire feed rate and weld voltage was set for the continuous fed weld wire. The welder would then press the gun switch and then direct and guide the gun to where the weld was required. However the reality has been for seven decades, that in contrast to any of the 2020, available sophisticated EP Pulsed MIG power sources, with their wide variety of weld transfer modes, or with any available gas shielded flux cored or metal cored wire, that in contrast, the higher weld energy DCEN TIG process, with it’s inert gas protection, the TIG process has been the process to go to when the highest manual arc, code weld quality was desired.
TIP TIG IS A PROCESS THAT DRAMATICALLY ELIMINATES ALL POSITION WELDER SKILLS: In contrast to GTAW and also MIG and flux cored, from root to fill passes, when using the semi-automated TIP TIG process, the weld shop simplifies all position welder skill requirements and of course eliminates many of the individual manual DC GTAW welder skills. Also TIP TIG, eliminates common concerns for the MIG – Flux Cored Wire Stick Out, (WSO) variations, that influence the weld energy produced.
ALWAYS SUPERIOR QUALITY WITH IMPROVED WELD CONSISTENCY AND UNIFORMITY. 200 TO 400% INCREASE IN GTAW PRODUCTION, AND ALWAYS HIGHEST POSSIBLE MECHANICAL PROPERTIES SHOULD WAKE UP ANY MANAGER OR ENGINEER INVOLVED WITH WELDS. With TIP TIG the weld wire is continuously directed into a unique upper plasma sweet spot. The position enables the highest possible plasma energy coverage over the weld, which in contrast to manual DC TIG, enables the ability to consistently deliver more weld wire and attain higher weld energy that always delivering the highest possible quality weld in an inert atmosphere, that’s more consistent and uniform, than manual GTAW. And lets not forget, with the increased TIP TIG weld travel rates and EN polarity, for the first time in arc weld history, the weld shop has a manual or automated arc process that should always attain the lowest distortion, the least weld / part stresses, and the highest possible welded part metallurgical properties.
TIP TIG, patented, Semi-automated Wire Feeder for either Manual or Automated arc welds. A brilliant mechanical action is the heart of the Austrian,TIP TIG, Plasch, Austria patent. There are cheap copies and the way to test them is in all position weld capability with the deposition rates attained. TIP TIG no magic electronic bells and whistles or the usual exaggerated weld sales claims, just a simple, wire feed mechanical action combined with AC Hot Wire current.
WIKEPIDA ADDS TO PROCESS CONFUSION THAT’S WITH THIS PROCESS IS COMMON THROUGHOUT THIS GLOBAL INDUSTRY; 2020 Note: Wikipedia and the majority of weld decision makers around the globe that I have followed that have been discussing the TIP TIG process, have for the last decade, an incorrect concept of the TIP TIG process, or have been providing incorrect descriptions of TIP TIG. As you are likely aware, in pulsed MIG, Reverse Electrode Positive, the electrons travel from the negative metal across the arc plasma and collide with the gas molecules and deliver around 70% of the plasma energy to the tip of the positive , continuous fed, MIG wire tip. An important note, the CV MIG welder can influence the weld transfer modes, short circ. globular or spray through changes to gas mixes utilized and the wire feed rate and volts. With Pulsed MIG the power source can also influence the weld drop size, and the rate of weld droplet detachment through the pulsed MIG parameters.
In contrast to the semi-automated pulsed MIG transfer, both the traditional DCEN GTAW, and DC TIP TIG circuit have a completely opposite function. With DCEN TIP TIG and DCEN TIG, first arc temperatures are far greater than possible with a MIG arc. The TIP TIG electrons travel from the tip of the negative tungsten to the positive ground. The electrons in the arc, apart from colliding and breaking the larger argon gas molecules for a high temperature plasma, provide the energy necessary to melt the weld wires. While TIP TIG is a semi-automated weld process, in contrast to MIG, most of the influence of the TIG power source is on the weld rather than on the wire running into the weld. Adding a Hot Wire current in the TIP TIG wire speeds up the weld melt, and using pulsed and variable polarity will also effect both the wire melt and weld.
As the TIP TIG wire melts, it forms droplets on the continuous fed wire tip. The key question is, what can be done to enable those weld drops to detach in a rapid manner before the continuous fed TIP TIG wire and drops make contact with the weld and disrupt the wire / weld transfer. The patented TIP TIG wire vibration, enables the weld droplets to detach and cross the arc. In contrast to DC TIG, the TIP TIG process allows much more weld wire to be deposited, which like a domino effect, enables more weld current to be used, and this influences both the plasma and weld?
Thanks to the Austrian, patented, Plasch invention, the TIP TIG wire vibrates, and like a plucked guitar string it agitates the wire so as the continuous fed wire exits the copper tip, the wire agitation “encourages rapid weld droplet detachment” from the wire. The more weld wire that can be delivered into the plasma, and on average TIP TIG delivers approx. 200 to 400% more weld than is possible with any GTA weld, the higher the weld current that can be utilized for the welds. The use of Hot Wire current also slightly decreases the time required for the molten welds drops to form. That increased weld current influences the weld energy and also increases the TIP TIG arc plasma density and width. These attributes reduce arc length sensitivity enabling TIP TIG to also be an excellent automated process without the concerns for arc length sensitivity, a common issues with GTA automation.
Since the 1940's, there has never been an arc weld process that provides the weld energy and welded part metallurgical benefits that can be attained with either the manual or automated TIP TIG process.
UNIQUE ATTRIBUTES OF THE TIP TIG PROCESS
IN THE LAST DECADE, MANY OF THE WELD DECISION MAKERS THAT ARE EASILY INFLUENCED BY A WELD SALESMEN, THOUGHT THE SOLUTION TO IMPROVING THEIR CODE QUALITY WELDS, WOULD EVENTUALLY COME FROM IMPROVEMENTS WITH THE PULSED MIG PROCESS.
Many weld decision makers in this industry believed in the 21st century, that with the never ending electronic bells and whistles they see added to the semi-automated Pulsed GMAW (MIG) process, that the Pulsed MIG would eventually provide the manual and also automated weld solutions to consistently enable all position code quality welds that don’t require weld rework. The weld reality is just as a donkey can never be a race horse, the pulsed MIG process will never have the unique weld process characteristics that is necessary to attain the weld quality and part metallurgical properties that can be attained with another semi-automated process called TIP TIG.
In my roles as both Corporate Product and Training managers with Linde, Airgas, AGA, ABB and Liquid Carbonic. I have been evaluating Pulsed MIG equipment from all the major GLOBAL Pulsed MIG mfgs. since the early 1980’s. And in the 1990’s, in my 600 page book “A Management and Engineers Guide to MIG” (training Resource Section) I wrote over a 100 pages on the issues with Pulsed MIG, and the reality is in 2020, that most of my 1980s pulsed MIG concerns are still relevant, however no one reads the book.
Note: For those interested in the extensive weld issues generated with Pulsed MIG especially in robot cells, you may wish to visit my MIG process / equipment sections at my weldreality.com site. or purchase one of my MIG weld process control self teach / training programs, also visit the TIP TIG versus Pulsed MIG section here.
The weld shop should be aware that if DC TIG, Pulsed MIG and Gas Shield Flux Cored is not attaining a weld quality in which zero weld rework is produced, with TIP TIG it’s easy to attain these weld results. The weld shop should also be aware with TIP TIG one TIP TIG welder will on average in a shift do the welds that three GTAW welders will do, and with TIP TIG there is no weld application size or part thickness limits.
TIP TIG All Position Welds are Easier than GMAW
REAL WORLD WELD BENEFITS FROM TIP TIG: With TIP TIG, no manual wire to feed and no amp foot control required. TIP TIG always superior control of arc starts – stops. TIP TIG no spatter, no weld fume concerns and no weld rework. With TIP TIG the smallest weld HAZ is produced with the least stresses and distortion. With TIP TIG always the highest weld and part metallurgical properties. Yes it’s an expensive process but the weld cost savings from no rejects or rework along with the dramatic reductions in welder skills and increased GTAW productivity and the cost is quickly justified.
As with any costly equipment to be used in a weld shop, the TIP TIG process of course requires cost justification, and it’s logical that weld shops during a TIP TIG demonstration should want to see and measure the improvements and cost reduction capability that will be provided by TIP TIG;
- With a short training program that should be presented not only to the welders, but also to all those that make weld decisions. (see my low cost TIP TIG training / self teaching power point programs), TIP TIG dramatically reduces all position welder skills, which enables increased and more consistent, uniform weld quality. In contrast to TIG – Pulsed MIG and Flux Cored, R
- The TIP TIG all position welder skill reductions dramatically reduces welder training times.
- TIP TIG dramatically improves both DC and AC TIG weld quality.
- TIP TIG enables more weld current than GTA welds which when combined with the unique TIP TIG wire placement produces a higher energy plasma with increased plasma coverage over the weld. Weld fusion is the highest possible with the lowest possible weld porosity.
- Weld quality is further improved from the TIP TIG consistent wire feed placement to the plasma sweet spot which enables the continuous, uniform melt of small weld drops that provide increased weld fluidity.
- In contrast to GTAW, with TIP, arc start – stops are dramatically reduced and with decreased arc length sensitivity their is less opportunity for tungsten contamination and tungsten melt.
- TIP TIG enabling on average 200 – 400 % more weld than DC TIG, enables increased weld current capability, and faster weld speeds, reducing weld costs.
- TIP TIG greatly extends the weld application potential and no job is to small, thin, large or thick.
- Be aware that for 5 – 6G pipe welds, the TIP TIG manual fill pass weld speeds would be similar to pulsed MIG.
- TIP TIG increased welds speed capability with electrode negative polarity dramatically lowers the welded part heat, which always enables superior welded part properties, with no concerns for carbide precipitation that affects corrosion, or concerns for weld stresses, part distortion and weld fumes.
- TIP TIG eliminates arc length sensitivity concerns, making it suited to all manual semi-automated and fully automated applications.
- TIP TIG enables the following results on the stainless fillet in the video below, The weld produced process attributes that no weld shop can produce when using DC TIG or any Pulsed MIG process.
With the above TIP TIG stainless gauge fillet weld, note the weld color, lack of oxidation, no spatter, and small HAZ that results from the lowest possible weld heat into the parts. Note how the welder can hold the TIP TIG torch just like a GMAW gun or if required like a GTAW torch. As with any semi-automated arc weld process, on parts with decent fit, with TIP TIG no weld weaves or skipping techniques should be used when making single pass fillet or lap welds up to 7 mm.
With TIP TIG, you have the best of both worlds, for groove or fillets, you can either rest the ceramic torch nozzle in a groove or on the plate, and if you walk the cup which adds to the simplicity and control of all position welds. Or the welder can hold the TIP TIG torch and weld like a MIG weld.
Again take a moment with the above video to examine the untouched stainless weld surface quality. Carefully examine the silver weld color, (lack of oxidation) attained that’s a benefit of EN polarity and increased weld speeds that result in the lowest possible weld heat input. Also then examine the weld fluidity continuity on the weld surface and toes, that reflects on the high weld energy attained. Note with the extremely small HAZ produced, a benefit weld shops can anticipate with any stainless welds, therefore the lowest distortion should always be attained. And with some stainless grades, with this process, anticipate the least opportunity for carbide precipitation. Also note the respectable weld speed being attained, (as quick as MIG) , and in case anyone is interested also note in the video as well as the photo, no visible stainless, carcinogenic weld fumes.
2020: MY MESSAGE TO THOSE NORTH AMERICAN AND EUROPEAN WELD – METALS CODE / SPECIFICATION COMMITTEE MEMBERS THAT APPEAR TO BE STUCK IN A COMA DURING THE LAST DECADE: Of course it’s appropriate that weld process information and metal guidelines should be kept up to date by the major Code bodies such as ASME – AWS – API – ASTM – ABS – NAVSEA. Unfortunately these N.American Governing bodies and their engineer committee members are in 2020, now ten years behind the capability of a process such as TIP TIG.
- TIP TIG will dramatically change the recommendations and guidelines that have been provided in the last seven decades. From my perspective, when it comes to comparing the common arc weld process’s that account for most code welds, GTAW – FCAW and GMAW , the code providers are not aware that when TIP TIG is utilized, major changes will be enabled.For example;
- Preheat, inter pass and post heat treatments are typically dramatically reduced or no longer required.
- Weld groove preparation dimension recommendations can be dramatically reduced. For example from the typical Vee-grooves of 60 plus degrees, to 40 to 50 degrees.
- Costly NDT weld inspection requirements should be reduced or elminated.
- There will be less concern for HAZ changes, impact properties will dramatically increase.
- There will be less concerns for cracks, stresses and distortion.
- There should be minimal concern for Carbide Precipitation or other corrosion issues.
- In clad welds, the weld layers can be reduced as a result of less alloy loss.
- Many Titanium welds will not require trailing shields.
Yet all I have heard since I introduced TIP TIG to N.America in 2009 is SILENCE. Which is again a reflection of where we are as an industry.the
WHEN TIP TIG IS BOUGHT INTO THE WELD SHOP AND ALL WELDERS THAT USE THE PROCESS ARE PROVIDED WITH CORRECT TRAINING (SEE MY MY 3 HOUR TIP TIG SELF TEACH / TRAINING PROGRAM) IN MY TRAINING RESOURCES, MANAGERS SHOULD EXPECT THE FOLLOWING BENEFITS?
- TIP TIG enable the best possible, manual and automated all position, consistent arc weld fusion, with the cleanest welds with the lowest porosity, so informed plant engineers or mangers should expect NO WELD REJECTS OR REWORK on any metals and code quality applications.
- TIP TIG provides optimum automated weld capability without arc length sensitivity concerns that are common with the Hot Wire process, so simply connect that TIP TIG torch to a robot, a carriage or rotary positioner.
- TIP TIG is the easier to use than the TIG – GMAW – FCAW process on all position code welds, and also enables the best possible root and fill weld quality. So on most pipe welds or welds with roots, instead of using two weld processes with TIP TIG you have one process that’s suited to any gauge, any thickness, or any size.
- TIP TIG produces code welds without spatter, and welds with the lowest oxidation that should not require grinding or cleaning.
- TIP TIG also enables the lowest possible weld fumes. If you weld any metals that have fumes or grinding dust that you don’t want to subject your employees to, you now have a weld process solution.
- TIP TIG always provides the lowest possible welded part heat input, the least distortion, the lowest weld stresses, the best possible mechanical and corrosion properties, and that applies to all metals.
Take another moment with the close up of the TIP TIG arc and weld.
- Note below the vert up, continuous highest possible arc weld energy, enables from increased DCEN current from higher deposition and smaller filler wire capability, and from the wire to plasma placement that enables full plasma coverage over the pool.
- Note the highest possible weld fluidity, a fluidity that is not inhibited by the already small fluid weld drop additions to the weld.
- Note the weld metal purity from the combination of highest arc energy capability protected by the inert atmosphere. Any weld person would know simply by looking at this weld that the weld would be defect free. This weld can not be duplicated with any Pulsed MIG or GTA weld.
Remember with any arc weld, the best possible code weld results will come from a weld process that provides FOUR prime weld functions;
- A weld protected by an inert atmosphere.
- An arc plasma that provides the highest weld energy.
- An EN polarity that enables a fast freeze weld making it easy to use for all positions.
- A deposition that enables good welds speeds in combination with an EN polarity that enables the lowest welded part heat input.
TIP TIP ENABLES SIMILAR VERTICAL UP WELD SPEEDS TO PULSED MIG. TIP TIG typically delivers 200 to 400% higher weld deposition rates than DC TIG and produces similar vertical and overhead weld travel rates as pulsed MIG. Another point, In contrast to traditional GTAW, both the DCEN & also Variable Polarity used for aluminum welds, TIP TIG continuously feeds the commonly used 0.035 – 0.045 (1 – 1.2 mm) diameter weld wires into the TIP TIG plasma sweet spot.
When TIP TIG is used on clean applications such as this Super Duplex fillet weld, note the untouched TIP TIG weld color which reveals lack of oxidation influence with the atmosphere. This is only possible with very low welded part heat input. With TIP TIG, weld shops should always anticipate the cleanest, defect free welds that produce the smallest weld HAZ, and this applies to most weld applications > 2 mm. Note try and replicate the fillet on on the left with either a duplex, stainless or inconel weld wire and the process of your choice.
CONSISTENTLY ATTAINING OPTIMUM UNIFORM WELD QUALITY & WITH THE LOWEST WELD COSTS, SHOULD BE OF INTEREST TO ANY GLOBAL WELD DECISION MAKER.
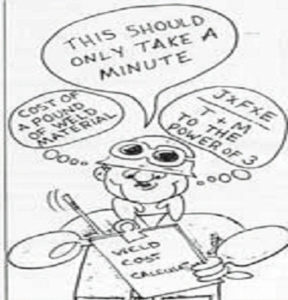
2019: I am aware that the technical weld process process details at this site may not get everyone as exited as I get when discussing TIP TIG versus the AC/ DC GTAW, Pulsed MIG, Gas Shielded Flux Cored and also the automated Hot Wire TIG, however most weld shops do have a great interest in two subjects WELD QUALITY AND COSTS.
With this in mind, I will start in the first following paragraph discussing some of the unique TIP TIG weld COST reasons that any company that is using DC TIG – MIG – Pulsed MIG or Flux Cored for code quality welds on steels, alloy steels, alloys and also specific AC TIG & MIG Aluminum applications, simply cannot afford to ignore.Please don’t forget that weld costs are of course influenced by weld deposition rates, weld rejects, weld rework, weld cleaning, by the welder’s skills, and by additional material costs or material handling.
Weld shops take note: The traditional arc weld processes such as AC/DC TIG, Pulsed MIG, Flux Cored or the SMAW process, require higher all position welder skills than required with TIP TIG.
As most in this business are aware, when hiring GTA welders;
[] the slow weld speeds and cost consequences,
[] the never ending weld start and stops ,
[] the many trips by the welders to the grinder to reshape and replace tungsten,
[] as GTAW welder skill requirements change from one welder to another, this and above have a major influence on both the GTA weld quality and the hourly labor costs generated.
If you were stand in any Aerospace plant and watch 5 TIG welders produce similar welded parts, and you will note that their different manual welder skills and weld practices are influencing the lack of GTA weld uniformity, continuity that results in the too often inconsistent weld quality attained,
THE FREQUENT TUNGSTEN CHANGES WITH TRADITIONAL DC TIG WELDS DO NOT OCCUR WITH TIP TIG :
As mentioned, DC TIG welders have to place their weld wire in front of the weld in a very small, fast freeze weld pool and often that wire or weld pool will touch and contaminate the tungsten, lowering the tungsten melt temperature and changing its required profile. The welder will then stop welding and replace their tungsten and create another weld start / stop which are common weld defect locations. When large amounts of AC/DC TIG weld are required, those tungsten changes will be very frequent. In contrast, the TIP TIG wire is fed to the side of the TIP TIG arc plasma and therefore its more difficult for the TIP TIG weld to contaminate a TIP TIG tungsten. Once this process is learnt correctly and especially the unique the TIP TIG Best weld practices the welder will likely have no more than one or two tungsten changes per shift.
SO LETS LOOK AT THINGS THAT INFLUENCE WELD DEPARTMENT BUDGETS WITH A CHANGE TO TIP TIG:
It would take me about an hour to prove the following statement. “In a weld shop that employs mostly DC TIG welders, with a change to the TIP TIG process, that weld shop should anticipate at least a 65 to 75% annual weld labor cost cost reduction in their weld department budget. As for those weld shops that utilize pulsed MIG or gas shielded flux cored on code quality weld applications, most of the weld shops will budget for weld rejects or weld rework. In contrast, with TIP the weld shop can anticipate no weld rework. The TIP TIG weld deposition and weld travel details that greatly influence weld costs are well documented at this site, however I want to get across both the the extensive weld costs savings potential and weld quality improvement impact with a change from regular DC TIG to TIP TIG and this applies to any company that provides Code Quality steels, alloy steels, alloys and also many aluminum weld applications.
The following info. provides how I attained an average of 70% hourly weld cost reduction with changing from DC GTA to TIP TIG.
DC TIG TO DC TIP WELD COST REDUCTION: Lets take a Fortune 500, Aerospace corporation that has many global plants that employ manual DC TIG welders for code quality weld applications, call it PLANT 1. This plants employs 10 DC TIG welders, five on each shift. The plant also employs two weld shop supervisors to manage the two shifts. The Aerospace TIG welders earn $30 /hr, and mostly weld steels and alloy steel code applications. This companies typical welder labor costs $60,000.00 / yr. The welders benefits are $8,000 / yr. Also as TIG is such a slow process, overtime is the norm. The average overtime per-TIG welder was 10 hours a week at time and a half, 10 x $45 hr = $450 x 50 weeks = ($22,500 / year). The annual TOTAL weld labor costs for the aerospace company is $90,500.00 per/welder x 10 welders. Also add two weld supervisors at $80,000 /yr, with the supervisor combined annual salary of $160,000.yr. The total weld labor cots for this Aerospace weld shop is $1,065,000. The TIG weld equipment investment for the 10 welding units, approx. $78,000.
COMPARE ABOVE PLANT 1 WITH WITH TIP TIG WELD LABOR COSTS IN PLANT 2:
Now for those still hanging in there, first thanks for your patience. The above aerospace company changes to TIP TIG. At PLANT 2, instead of the 10 DC TIG welders, all this company would now require to achieve the same weld production with superior weld quality , would be three TIP TIG welders and one supervisor working one ONE shift. Three TIP TIG welders wage plus benefits, 3 x $68,000 / yr = $204,000 / yr, plus one supervisor $80,000 / yr, producing a yearly TIP TIG WELD LABOR costs of $292,000. By the way with TIP TIG you would also reduce the annual argon TIG gas cost in the range of 50 to 70% , and also take approx. 15 – 30% of the weld wire costs. The TIP TIG equipment costs depending on the power sources available in the shop would be in the range between $50 to $80K. As you you can see with the added weld consumable savings, its easy to anticipate at least an annual TIG labor cost savings of 70% would be anticipated.
The above annual DC TIP TIG weld shop wages total is $292.000. The annual DC TIG weld shop wage $1,065.000.
A GTAW Weld Cost Question: Em, as weld deposition rates are a large factor in weld shop costs, can you provide more detailed info. on the typical average weld deposition rate capability with manual DCEN TIG welding?
Regular DC TIG Weld Cost Answer:
Welding a 3/16 horizontal fillet, the DC TIG manual welder on average would feed a common 3/32 steel or stainless TIG wire into the weld pool at approx. 8 inch minute, (20 cm/min). This wire feed rate delivers just less than 1 lb/hr with 60 minutes arc on time. Lets say the average arc on time per/hr for a TIG welder may be around 20 minutes delivering approx. 0.3 lb/hr.
If a TIG welder decided to try and feed a smaller 0.035 (1 mm) wire, with an 0.035 steel or stainless wire, the welder would require that the DC TIG welder continuously feed the 0.035 wire at around 70 inches per-min, (not going to happen with traditional TIG).
TIP TIG Weld Cost Answer: On the same weld, the TIP TIG welder would set an 0.035 wire feed rate of around 150 inch/min, approx 2.2 lb/hr, As TIP TIG increases the arc on time to lets say 30 minutes per-hr the TIP TIG welder is depositing 1.1 lb/hr, so you can see with this conservative TIP TIG setting the TIP TIG welder is putting in 200% more weld and depending on the weld application, the TIP TIG process will readily provide a 300 plus percent increase in weld than is possible with the DC TIG welder.
I HOPE YOU ARE NOW ALL WELL AWARE THAT TIP TIG IS UNTOUCHABLE FOR ALLOY WELDS, BUT WHAT ABOUT THE COST SAVINGS FOR A SIMPLE CARBON STEEL PIPES WELD APPLICATION?.
As reported by a TIP TIG user. Our customer ordered plain carbon steel pipe assemblies from the weld shop used in heating system. This was a first time that they had used TIP TIG for any welding application. The biggest pipe was 8 inch diam with a 1/4 wall.
With regular DC TIG it took around 90 minutes to complete the pipe welds from root to cap and this was done with 3-4 passes depending from the welding position. With TIP TIG the same pipe welds with made two weld passes and in 30 minutes. As for the weld quality, 100 % x-ray was used on the welds. With regular TIG this company would often find minor defects and with X-RAY evaluation pipe weld rework was common. In contrast with the TIP TIG welds there was absolutely nothing shown on the X-rays. The X-ray were taken with digital equipment so they were able to zoom in and check everything very precisely. So the weld shop attained far better quality, extensive increased production, and this was within the first two weeks of purchasing the TIP TIG equipment.
Note: Please keep in mind, that with all position code quality weld applications as in pipe and vessel plants will also employ Pulsed MIG welders. You may be surprised to know that the weld deposition rates for code quality vertical up and over head pulsed MIG welds are quite similar to the deposition rates attained by TIP TIG, however the pulsed MIG weld quality will be inferior with special concerns for the weld fusion, the weld heat, porosity and weld fume concerns. Of course for horizontal fillet welds the pulsed MIG process will enable dramatic deposition rate increase, but again with the quality, heat and fume concerns.
IMPROVED WELD CONTROL COMES WITH DRAMATICALLY REDUCING ALL POSITION WELDER SKILLS AND ALLOWING TWO HANDS ON THE TORCH:
If the above was welded with DC GTA, the welder would have one hand on the torch, the other hand to feed the wire, and maybe one foot on the amp control.
If the above was welded with pulsed MIG, apart from the inferior weld quality especially with the sluggish stainless, the MIG welder would have to deal with weld fumes and spatter.
- With TIP TIG code quality all position welds, and the rapid freeze characteristics influenced by the EN polarity, the weld pool is easy to control and the welder skills are dramatically reduced. Also one or two hands can be used to hold the TIP TIG torch and the TIP TIG welder does not require a foot amp control.
- Irrespective of a person’s background, the TIP TIG process is easy to learn in a few days, that is if the correct settings and best weld practices are taught, (available at this site). This is a process that will reduce the concerns for skilled welder shortages, and reducing welder skills will affect weld labor costs.
- Reducing welder skills also enables higher weld quality, especially when the weld shop employs more than one welder and wishes to produce uniform, consistent optimum manual weld quality.
- Don’t forget that the TIP TIG weld wire is continuously fed into the plasma arc sweet spot. This wire feed feature, drives consistent, uniform weld melt that enables consistent weld fusion, decreased weld porosity, and enables improved control of the weld travel rates.
- In contrast to a manual DC TIG weld, typically no more that two weld settings are required for the weld wire diameter utilized. And TIP TIG weld arc starts and stop parameters are automatically controlled, to a weld quality level that will never be available with any TIG, Pulsed MIG or Flux Cored weld.
- With TIG welds, there are often many weld arc start / stops influenced by the manual wire delivery that affect both weld quality and productivity, solution provided by TIP TIG.
- Instead of using DC TIG and then adding another weld process to complete the welds, such as TIG and Pulsed MIG, with the TIP TIG process, the weld shop requires one weld equipment package, one weld wire, one gas for any pipe root to fill, or for any all position welds on any metals, and on welds with any thickness. One process one skill set.
Of course many welds don’t require the TIP TIG process: If welds are made on parts in which “internal” code weld quality evaluation is not required, or on parts with mill scale, coatings and contaminates in the weld area, then MIG and flux cored would be a more appropriate weld process choices. However if they are not code quality welds and if weld spatter, weld cleaning or weld fumes is a concern, consider TIP TIG.
PIPE ROOT WELD OPTIONS: Three decades ago, I manged a pipe weld project, training Imperial Oil, (Exxon) union pipe welders, Tar Sands Alberta Canada. Left, Ed checking the MIG root weld issues generated with with different MIG weld transfer modes.
Imperial Oil was looking to create dramatic Nat Gas pipe line weld cost reductions, and I was contacted to first train the “we love our SMAW weld process” sub-contractor, manual pipe welders on how in the 5G pipe position, for pipe root welds to use the semi-automated Lincoln MIG STT process, (in reality a simple low pulsed MIG mode), and also the Miller RMD (reduced SC current) process. And for their shop welded rotated pipe joints, teach the welders the process controls – best weld practices with the conventional MIG Short Circuit mode.
After the 5G Exxon pipe welder root training, I provided the same welders gas shielded flux cored process control – best practice, 5G pipe fill pass training. At that time, the Oil & Nat Gas industry did not have an extraordinary pipe weld process such as TIP TIG which was all they would have required for root and fill passes. And its perhaps a reflection of the general weld engineering apathy found in the Oil – Nat Gas industry, that in 2020, ten years after I introduced TIP TIG to N.America and Australia, that most weld engineers and relevant managers in this industry, still know little about the TIP TIG process.
On a pipe projects like the above, if the welders used TIP TIG, they would have;
- only required one weld process for all root and fill passes,
- only required one gas,
- only required one weld wire,
- only required one weld procedure with two simple weld settings.
- have had the ability for zero weld rework.
- would have attained the highest possible impact properties, a necessary requirement for Alberta.
WELD REALITY: The most popular Semi-automated MIG process for Pipe Root Welds is MIG. First it was MIG Short Circuit, followed by MIG STT and MIG RMD, for the root, and then another process such as flux cored or pulsed MIG for the fill passes. The reality is no other arc weld process can compete with TIP TIG in terms of capability and quality on code quality welds.
Linclon MIG STT Left – Miller RMD right. Both attaining acceptable 5G root, vert down weld results. If I had to GMA a pipe root today I would use an OTC pulsed unit.
Ed Training Exxon / Imperial Oil pipe welders on the different MIG weld transfer modes available to weld Nat Gas Pipe. Pipe weld shops need to be aware that when they use MIG Short Circuit for rotated pipe root welds, or use MIG STT or MIG RMD for the all position pipe root welds, in contrast to TIP TIG they are using inferior arc weld processes that are not only sensitive to wire stick variations, but also sensitive to root weld gap and root alignment variations. That sensitivity is not part of the TIP TIG process
Pipe, plate, vessel, valve, tank welds when the best possible weld quality is required, from the root welds to the fill passes, TIP TIG would always provide all position fill weld passes with superior mechanical or corrosion weld / part properties, and all the QA department would have to do is document the passed welds.
What about Gas Shielded Flux Cored Welds? There are many reasons why an experienced weld engineer should be nervous about allowing gas shielded flux cored welds on code quality applications in which the internal quality of each weld is closely evaluated. And there are many reasons why the weld shop should not be surprised on any code quality all position welds, when the flux cored welds that are made by a highly skilled welders looks like this.
The Gas Shielded E71T-1 Flux Cored process does not need a welder to be responsible for generating weld defects.
If you are aware of the weld process controls and best weld practices associated with Gas Shielded Flux Cored, (as taught in my process control programs), you would know what was the prime cause of the common issue.
With code quality welds, and the traditional arc weld processes, such as flux cored, pulsed MIG and SMAW, there are many reasons beyond the welders control, why managers, engineers and supervisors cannot get a good nights sleep.
MOST EXCELLENT LOOKING MIG FILLET WELDS, WHEN MACRO EXAMINED, WOULD REVEAL MARGINAL SIDE WALL WELD FUSION
What makes TIP TIG a superior weld process than Pulsed MIG or Gas Shielded flux cored for vertical up and over head welds?
An easy way to explain why the Reverse Polarity MIG and Gas Shielded Flux Cored process will often leave welds with lack of weld fusion, especially with vertical up and overhead welds on parts > 5 mm thick. Both MIG and gas shielded flux cored arc temperatures are almost 50% of a DC TIG weld. And with the Reverse Electrode Positive MIG and flux cored welds in which most of the arc energy plasma is used to melt the continuous fed weld wires, they simply do not have the required weld energy for the welds the weld mass delivered, and the weld deposition rates delivered that influence the weld travel speeds generated which influence the weld solidification rates. The bottom line is MIG and flux cored cannot generate the weld fluidity that’s created by a DC Electrode Negative TIP TIG weld.
As for weld purity which influences weld porosity and oxidation buildup, both MIG and flux cored use reactive gases such as CO2 and Oxygen which add to the weld porosity formation. And when gas shielded Flux Cored is selected for code applications weld shops should be aware that with this process, there can never be a guarantee of not getting trapped weld slag, worm tracks influenced by moisture and excess porosity. When you add the common weld defects found with flux cored or MIG, along with the concentrated weld heat around the weld wire tip influenced by reverse polarity, you will have questionable weld quality results and also welds that have large weld heat affected zones. Therefore, when it comes to code welds, the semi-automated MIG and flux cored weld processes simply cannot compete with the semi-automated TIP TIG process.
Note: Be aware that the typical increase in weld deposition rates that are attained from TIP TIG, the weld shop, typically will provide all position TIP TIG travel rates that are similar to those attained with pulsed MIG process. |
TIP TIG is not simply the evolution of TIG welding, for code quality welds, it's the evolution of all arc weld processes. For those awake in Covid 2020, welcome to the now 13 year old, TIP TIG process.
In the above video, you could ask yourself the following questions.
- Why is this super hot looking stainless weld silver in color, what happened to the oxidation on these thin parts?
- Why is the weld so hot yet the Heat Affected Zone (HAZ) is so small?
- How is that spatter free, 1/4, (6 mm) TIP TIG fillet weld being made at a weld travel rate more in common with a pulsed MIG weld?
- For those aware of the hazards of carcinogenic weld fumes generated when welding stainless chrome alloys, where are the fumes?
In an advertisement that I produced for TIP TIG USA, the USA company that my partner Tom O’Malley and I founded around 2009, I called TIP TIG “the EVOLUTION of TIG”. However while examining the TIP TIG process on a wide variety of weld applications over the next 11 years, the weld reality with this unique weld process as you will read at this site, is that TIP TIG is much more than an improved versions of the DC/AC GTAW and Hot Wire GTAW process.
FROM TWO TO THREE SEMI-AUTOMATED ARC WELD PROCESSES, Since the 1950’s, there has only been TWO SEMI-AUTOMATED cost effective arc weld processes available to the global weld industry, GMAW and Flux Cored. And the reality is with approx. 70 years of process and equipment development, both these processes as you will read at this site cannot be relied on to consistently produce welds subject to X-Rays, that will not require weld rework. Around 2009 in N.America, things changed, I introduced the semi-automated Plasch invented TIP TIG process to N. America.
Here we have a 2020, TIP TIG unit connected to a Miller Dynasty 400 amp TIG power source. Miller proudly claimed that with it’s use of sophisticated electronics in the Dynasty, that they were proud to announce to their customers who did TIG welds with the Dynasty, that in contrast to traditional DCEN TIG equipment, weld shops MAY anticipate around a 17% increase in hourly TIG weld productivity.
However when a TIP TIG Wire Feeder and Hot Wire power source is added to that Miller Dynasty unit, not only does the weld shop dramatically reduce the required TIG welders skills, they should also anticipate with the TIP TIG unit at least 200 to 400% more weld each hour. Also for the first time, the weld shop will attain the weld heat dissipation benefits of DCEN polarity, along with the numerous weld quality and metallurgical benefits that result.
For 70 plus years, we only had two practical semi-automated weld processes, GMAW - FCAW, however if the best weld quality was required we turned to traditional GTAW.
Two big developers of GTAW equipment in the 1950’s – 60s, Union Carbide & Westinghouse.
It’s a weld reality that with the above old DC TIG weld equipment, or with the 2019, DC TIG weld equipment shown below, the weld shop would produce similar DC weld quality and productivity. Of course the 2019 TIG welder is now using an Inverter power source loaded with electronics that could enable DC pulsed frequency, however this equipment also makes these type of power sources less durable, and more costly to repair. Lets face it, the modern day welder below looks good with his fancy gloves, jacket and weld helmet, however the reality for weld shops, is as they have been aware for approx. 70 years, that the AC/DC TIG process, when used on code quality welds would provide the best arc weld quality, while also requiring the highest arc welder skills and producing the lowest weld deposition rates. Those deposition rates also produce slow weld speeds that will influence the welded part properties.
2019 GTAW (TIG)
Hello my name is Emily Craig, used to be Ed, but now I am where I belong. Many of you will know me by my twenty PLUS year weldreality.com web weld blog, or perhaps you were one of thousands that attended my MIG and flux cored weld process control seminars in the 1980s. Maybe you were one of the 80,000 readers of the “Weld Design & Fabrication” magazine in which each month for almost 20 years, you read the monthly Weld QA column that I wrote. And for those of you that have a “Machinery Handbook” gathering dust on your shelf, I wrote the weld section, and was also the key technical writer of AWS MIG Specifications.
The TIP TIG process was invented by Plasch in Austria. In 2009, when I should have been thinking about retirement, I found this process in Scotland, and during a 10 minute demonstration from my friend Darren Mathierson, and I was determined to introduce TIP TIG to N.America and also to Australia. I established TIP TIG USA in 2009 with another friend Tom O’Malley, and a year later Tom and I also introduced TIP TIG to Australia and China came running.
IN WELDING, THE EXPERTISE, EXPERIENCE AND APPLICATION DIVERSITY OF THE MESSENGER HAS TO BE HIGHLY RELEVANT…In 2020, I am providing information on my back ground, as the weld process information I am about to present to you will be very different from what you read elsewhere, and as you will likely be aware in this industry where process confusion is too often the norm, the weld experience of the engineer presenting any weld data should be highly relevant. As a weld engineer, who has specialized in Weld Process Controls – Best Weld Practices for more than 5 decades, I spent the last 40 years working in 13 countries resolving weld application quality and productivity issues. Also as a weld product and training manager with Airgas – AGA – Praxair – Liquid Carbonic and the N. American Weld Manager at ABB Robots, I also spent decades doing arc weld process, consumable and weld equipment evaluations from the world’s leading companies from around the globe.
For decades, my focus has been on the simplification of arc weld process controls and best weld practices required for weld process optimization. Some of you will have one of my three books on the subject, or purchased my low cost self teach / training resources on the requirements of weld process controls – best practices. I believe that this focus and my 50 years of hands on experience in over a 1000 weld shops, provides me with the expertise and capability to critique the global weld industry, and to point out the unique attributes and detriments of each arc weld process, and how each of the common arc weld processes compare with the TIP TIG process.
Manual, automated or robot welds, my process control training programs enable weld shops to provide the best possible weld quality at the lowest weld costs, and provide the resources front office weld decision makers need for weld process ownership, plus eliminate the need for weld personnel to play around with weld controls with Manual MIG – Robot MIG – Gas Shielded Flux Cored – Advanced TIG, and now also now on the TIP TIG weld process. I
IN A WELL MANAGED WELD SHOP, EACH ENGINEER, SUPERVISOR AND MANAGER INVOLVED WITH WELD DECISIONS WOULD UNDERSTAND WITH THE PRIME WELD PROCESSES UTILIZED, THE REQUIREMENTS OF WELD PROCESS CONTROLS – BEST WELD PRACTICES THAT ARE NECESSARY FOR WELD PROCESS OWNERSHIP AND WELD QUALITY & PRODUCTIVITY OPTIMIZATION.
AND WHEN THAT RARE NEW WELD PROCESS OPPORTUNITY COMES ALONG TO FURTHER IMPROVE WELD / PART QUALITY AND DRIVE DOWN WELD COSTS, THESE INDIVIDUALS WOULD FIRST PROVIDE THE JUSTIFICATION, AND THEN IMPLEMENT THE CHANGES, AND PROVIDE THE TRAINING.
UNFORTUNATELY TOO MANY WELD DECISION MAKERS IN FORTUNE FIVE HUNDRED COMPANIES ARE WHEN IT COMES TO WELDING STUCK IN THE 20th CENTURY:
Someone should put the above advice on the notice board of every Defense, Aerospace , Power , Oil and Medical Equip. company in N.America.
At a time when TIP TIG was available, the shipyard designers, managers and engineers who made the costly decision to use DC TIG for their Titanium pipe welds produced during construction of a recent, US Aircraft Carrier, were in reality, well in sync with the Navy, who every year manages to pay contractors hundreds of millions of dollars on unnecessary weld-rework and labor costs. This sad engineering approach has in Navy Ship Yards gone on for decades, and in 2020, the majority of defense contractors are using a 20th Century, apathetic approach to much of their arc welding and fabrication, an approach that reveals the too common front office lack of capability for front office weld process ownership.
OVER FIVE BILLION DOLLARS ARE LOST ANNUALLY ON WELD QUALITY AND PRODUCTIVITY ISSUES, THAT WITH WELD PROCESS CONTROL EXPERTISE COULD EASILY BE ELIMINATED. BY THE WAY THAT’S EXPERTISE THAT GLOBAL COLLEGES AND UNIVERSITIES DON’T TEACH TO TECHNICIANS AND ENGINEER STUDENTS.
We are all likely aware of the unnecessary hundreds of millions of dollars lost annually in large ship yards due to poor flux cored and MIG weld quality and productivity issues, or the never ending robot MIG problems in most global auto / truck plants. However, it’s also a sad weld reality that in 2020, the majority of Defense, Aerospace, Oil and Power industries that are more than well served by mechanical and weld engineers, are in 2020, likely utilizing the 1946 GTAW process. A process that requires the highest welder skills, produces the lowest weld productivity, and to often on heat sensitive weld applications, puts in too much weld heat into the parts.
When plant or shop weld decision makers, select the DCEN TIG weld process, in 2020 they need to be aware that they are;
- requiring welders to use unnecessary high welder skills and practices, both of which influence weld quality, the weld uniformity and the weld labor costs,
- producing TIG welds that require unnecessary weld starts – stops, (typical defect locations),
- producing slow TIG welds that are providing unnecessary high welded part heat, an issue that affects distortion and mechanical – corrosion properties,
- when welding, making titanium and other heat sensitive weld applications more complex,
- using a process in which in mfg, its difficult with a group if welders to create uniform welds,
- each hour ensuring that their welders are on average adding 200 – 400 % to their companies weld labor costs.
Above. From a weld engineering perspective, DC TIG welding was an inappropriate and outdated approach for this Navy Ship Building yard when it was selected to weld this Titanium and other pipe welds on a 21st Century US Aircraft Carrier.
2009: Chinese National Oil Company. when it comes to welding, a decade ahead of N.American – European Oil / Nat Gas companies.
After I introduced TIP TIG to CNOC in 2009, their engineers and managers quickly embraced the process Above in 2009, two Chinese National Oil Company TIP TIG welders producing Inconel and steel Sub-sea pipe welds, and in reality attaining a weld quality and productivity simply not possible from Pulsed MIG or DC TIG. (discussed below). Here we are in 2020, eleven years after I introduced TIP TIG to N.America, in the common “why change the way we have always done it” Defense, Aerospace, Oil and Power company weld shops, too many engineers and managers continue to use for their pipe, vessel and plate groove code quality welds, outdated or inferior weld procedures and out dated inferior weld processes such as TIG, Pulsed MIG of FCAW.
WAKE UP AMERICA….I ALWAYS FOUND IT IRONIC THAT AFTER GOING TO GREAT RISK, HASSLE AND EXPENSE I COULD NOT AFFORD, TO ESTABLISH THE TIP TIG PROCESS IN THE USA AND AUSTRALIA DURING 2009, THAT THE FIRST COMPANY TO RESPOND AND PLACE AN ORDER, WAS ONE OF THE LARGEST OIL COMPANIES IN CHINA.
In contrast to Pulsed MIG and Gas Shielded Flux Cored, TIP TIG is an expensive process yet it also is a semi-automated process, and as with any weld process selection, requires logical weld quality – weld productivity and weld cost justification. As for TIP TIG cost versus TIG welder costs, if it takes three TIG welders to do the work of one TIG welder, well even Donald Trump could figure out the annual cost savings produced.
Keep in mind that for decades in the weld industry, there has been only two semi-automated arc weld processes. Since 2009, there are THREE Manual Semi-automated weld processes for weld shops to consider for code quality welds, TIP TIG, MIG and Gas Shielded Flux Cored. Anyone that considers the Self Shielded Flux Cored process suitable for code quality welds, has from my perspective been listening to misinformation from a salesman or been guided by the screwed up and inappropriate FEMA recommendations.
All weld shops need to be aware that in 2020, there is no MIG weld mode or flux cored wire, (as shown at this site), that will ever attain the all position weld quality capability, or the welded part metallurgical properties on all metals that can be attained by TIP TIG.
The following are the specific weld applications that I recommend TIP TIG be considered for. Consider TIP TIG when;
- all position, code quality welds are required,
- the welds require open roots and fill passes that are subject to internal weld quality NDT,
- the welded parts have concerns for distortion,
- the welds have a special concern about the weld fusion or porosity.
- the welds are on alloys, alloy steels and high strength steels,
- the welds and parts require specific mechanical and corrosion properties,
- the welds have preheat – inter-pass temp. or post heat requirements, that could now be reduced or eliminated,
- it’s highly cost beneficial if reduced groove weld dimensions are possible,
- weld fumes are a concern,
- welds are being produced in which grinding and cleaning need to be eliminated.
Please remember that the semi-automated or full automated TIP TIG system is also when required an AC/DC TIG unit. So when TIG is required for example weld a very thin application 0.010, the welder can just shut the TIP TIG wire feed and hot wire unit off, and TIG weld the part.
Note Ref Alum. Welds: If wire feed ability is not an issue as with the > 0.046 5XXX series aluminum wires, TIP TIG using the Balance Wave, 80 – 90% EN – EP, variable polarity, will with the faster welds TIG speeds enabled, lower weld heat to levels never before attained and create aluminum welds with much higher welded part strength and lower weld porosity than has ever been possible with a TIG or Pulsed MIG weld.
SpaceX, while rapid evolution in rocket technology, it was slow evolution in their weld engineering technology.
Some are slower than others. SpaceX first learnt about TIP TIG around 2009, it then took their engineers and managers ten more years to figure out that this was the arc weld process that would give them the best opportunity to consistently pass the NASA destructive tests for the Falcon rockets.
Evaluating the weld quality / productivity, semi-automated TIP TIG process benefits, as Elon Musk and his SpaceX managers / engineers eventually discovered, is not Rocket Science. With this process any weld shop will quickly find out that TIP TIG;
- will in contrast to the other arc weld processes, show that all position welder skill requirements are dramatically reduced,
- will always produce superior weld quality with improves weld uniformity and consistently,
- will show that inter-pass temperatures are typically not required, and pre-heat and post heat will often be eliminated or reduced.
- will show that distortion issues are no longer a concern,
- will reveal on all metals that weld & part cracks no longer concerns,
- will show no weld porosity concerns,
- will reveal no weld fume concerns,
- will eliminate weld rework,
- will in contrast to DCEN TIG, on average, enable 200 – 400% more weld each hour,
- will on all position welds produce weld speeds that are compatible with the inferior pulsed MIG process.
THE GLOBAL, MANAGEMENT AND ENGINEERING INDUCED NONSENSE ABOUT THE SO CALLED “SKILLED WELDER SHORTAGE” HAS FOR DECADES BEEN SIMPLY RIDICULOUS, AND UNFORTUNATELY ITS SIMPLY BEEN ANOTHER INDICATION OF THE GENERAL FRONT OFFICE MANAGEMENT AND ENGINEERING LACK OF WELD PROCESS OWNERSHIP CAPABILITY.
So here we are in 2020, and as they have done for decades, those managers and engineers that lack the ability for weld process ownership with ARC weld processes that typically have one or two controls, will be found in welding magazine articles complaining about their inability to find “skilled TIG welders”. Yet the reality is that thanks to TIP TIG, the traditional TIG weld skills have been redundant now for more than a decade. And for those apathetic managers and engineer who can’t find skilled MIG and flux cored welders, read below or visit www.weldreality.com
Common comment in many global weld shops
2020.. In the “why change the way we have always done it” Aerospace, Defense, Power and Oil industries, you will find with the majority of facilities that weld are still stuck in the 20th Century using traditional GTAW as their prime arc weld process. This is a process that requires the highest welder skills, provides the lowest weld deposition rates and produces high welded part heat input. This is an indication of what?
Welders don’t typically advance weld technology, but weld decision makers should.
2020. IT’S NOT JUST ABOUT THE N. AMERICAN LACK OF GLOBAL WELD SHOP AWARENESS OF THE 10 YEAR OLD TIP TIG PROCESS, IT’S ALSO THE GENERAL LACK OF ENGINEERING AWARENESS OF WELD PROCESS CONTROLS AND BEST WELD PRACTICES.
In the last decade, two of the companies that I provided MIG and flux Cored process control training employed approx. 700 weld personnel. Many of the weld personnel had limited weld experience, and the majority with weld experience played around with their weld controls and were mostly using poor weld practices. One training program I provided occurred in a USA. ship yard that made oil tankers and container ships. The other training program was for a company that built rail road tankers for transporting oil. These two industries had something in common in that they both used gas shielded flux cored and MIG. In both facilities, I required less than 7 days to enable over 200 “none welders” to meet the ship yard ABS ceramic backed, and the rail road companies AWS steel backed, all position, Gas Shielded Flux Cored welder qualification tests. For those that had weld experience it took my one day program for these personnel to learn the requirement for weld quality – productivity optimization.
Note: Above Photo. Myself in blue sweater in the rear, and my friend Tom, (blue right), training ship yard welders in something that in reality has for decades, been a missing link in most global ship yards. Weld Process Controls – Best Weld Practice Training. This training has little in common with the usual ship yard welder training program. Its a program that enables the participants, the weld process controls – best weld practice expertise, so when they walk up to a MIG power source, they can instantly, (without playing around) set optimum FCAW or MIG parameters, and then use the required best weld practices to produce welds that would ensure minimum weld rework and welds with maximum weld production.
Why would managers select a weld process that requires higher welder skills, will produce inferior weld and part quality, and creates much the highest costs
WHILE WELD SHOPS ARE AWARE OF THE HIGH WELD QUALITY OF THE TRADITIONAL GTAW PROCESS, THEY HAVE ALSO BEEN AWARE THAT FROM A WELD APPLICATION AND COST PERSPECTIVE, IT’S BEEN A WELD PROCESS THAT’S OFTEN LIMITED IN WELD APPLICATION SCOPE.
FOR 70 PLUS YEARS, WHEN USED IN A MFG. ENVIRONMENT, THE REQUIRED GTAW WELDER SKILLS WOULD OFTEN CREATE A LACK OF MANUAL TIG WELD APPEARANCE, AND WELD UNIFORMITY AND CONSISTENCY.
I have been in many Aerospace, Defense and Medical companies that employed a group of DC TIG welders making similar welded production parts. And the first thing I would often note on the weld shop floor, was apart from the usual, pathetic lack of management / engineering Weld Process Ownership, there also was a common LACK OF WELD QUALITY – WELD APPEARANCE UNIFORMITY on the production parts, this was greatly influenced by the fact that manual GTAW was not a Semi-automated weld process. Also what would be missing from not only the weld shop floor but also the front office, was an evident lack of weld process controls and best weld practice expertise.
For those interested. My weld process controls – best weld practice self teach / training resources are applicable to MIG – Robot MIG- Gas Shielded Flux Cored, GTAW / Advanced GTAW and now also the TIP TIG process. link here, https://weldreality.com/weld-training-resources/
TO UNDERSTAND THE POSITIVE ATTRIBUTES OF TIP TIG, WELD DECISION MAKERS SHOULD FIRST UNDERSTAND THE NEGATIVE ATTRIBUTES OF THEIR DC/AC GTAW PROCESS.
As DCEN TIG for approx, 75 years has provided the best manual arc weld quality for steels and alloys, it’s understandable that few weld decision makers will have given consideration to the DC or AC GTA weld issues generated by this important weld process.
The DC/AC TIG manual requirements to feed the lengths of weld wire into a short arc length, small rapid freeze weld area, influences the weld current capability and the wire melt energy and uniformity and continuity which of course will influence the weld quality, weld consistency attained between different TIG welders that are welding the same products. The manual feed requirements also will influence tungsten contamination and wear.
Many DC TIG manual welds, will as a result of the weld wire lengths utilized, have the weld requirement for frequent weld start and stops, which are common code quality weld defect locations. The starts / stops and very low deposition rates that result in very slow TIG weld speeds greatly influence the welded part heat input.
With the deposition rates attained, the DC TIG process has from a weld cost perspective, been poorly suited to many common global weld applications that required a good amount of weld metal.
The poor TIG deposition rates have on many weld applications, resulted in the requirement of an additional, inferior, secondary weld process such as SMAW, Flux Cored or Pulsed MIG to also be utilized. With the DC/AC TIG application restrictions, the weld shop had to acquire additional weld processes / weld equipment, weld consumables, and required different weld procedures, welder skills and weld practices.
Low TIG weld deposition rates not only affects the weld speed capability, it also restricts the TIG weld current capability for the weld which apart from affecting the weld fusion and weld porosity, also influence the arc length sensitivity that would often become especially notable with automated TIG applications.
The high TIG welder skill requirements, and the low TIG weld deposition rates, typically create the highest Weld Labor Costs.
- The DC TIG process can often be “arc length sensitive,” adding to the manual welder skills and as mentioned making TIG poorly suited as a semi-automated process. If used with automated welds that require filler metal, TIG will often require costly, automated arc length correction equipment.
Carefully Examine the Traditional DCEN TIG Weld and Plasma Functions.
For almost 65 years, on most manual welds, the DCEN TIG process, has never been able to fully utilize it’s full energy potential from it’s high temp. arc plasma, therefore this process rarely enabled benefits that could have been attainable from the Electrode Negative Polarity Conductivity capability.
Examine the typical DCEN TIG weld as the large TIG weld wire is fed into the bottom portion of the plasma close to the weld pool. When melting the large TIG weld wire, as the wire gets close to the outer plasma, the wire tip melts and the DC TIG plasma is drawn slightly to the molten formation on the wire tip. The small fluid weld pool being generated by the restricted weld deposition attained is in reality a small “rapid freeze weld pool”. The DC TIG weld pool energy, and rapid weld solidification times, not only effects the TIG weld fusion potential and also porosity. The low deposition and restricted weld current also influences the weld arc stability and therefore arc length sensitivity. Take another close look at the above DC TIG plasma influence on the base metal, the weld, and the wire melt.
Three multi – functions of the traditional DCEN TIG plasma and filler metal reactions.
- A portion of the traditional DC TIG plasma energy is being used to maintain the small fluid weld area behind the tungsten.
- A portion of the plasma energy in front of the tungsten ensures the leading edge of the weld pool has sufficient energy to fully melt the molten filler wire.
- An outer front portion of the DC TIG plasma energy is used to melt the tip of an over sized weld wire.
Note this is a weld wire that is typically twice the diameter of a MIG wire. A wire size that has to be used for manual TIG, (discussed below). A large weld wire size that actually restricts both the weld current that could be used and weld deposition rate that could be attained.
GTAW IS USING UNNECESSARY HIGH WELDER SKILLS: For the few weld supervisor, managers or engineers that visit this site, please note. The regular DC/AC TIG process, has for decades required the highest welder skills. TIG welders have to manually feed the weld wire and know when to feed the wire. The TIG welder may be required to aggressively manipulate the torch, and sometimes at the same time operate a foot amp control.
GTAW IS POORLY SUITED TO WELD AUTOMATION: As a result of the TIG common arc length sensitivity, and other TIG weld issues discussed in this section, the regular DC TIG process is frequently poorly suited as a “manual Semi-automated” process, and poorly suited as a Fully Automated arc weld process on applications in which filler is required as there would be concerns for tungsten to work, arc length variations.
Now take a close look below at the semi-automated TIP TIG process. First examine the arc, plasma and the unique continuous fed weld wire delivery features that will be discussed below.
There are numerous weld benefits derived from using the Semi or Automated TIP TIG process:
FOR MANY DECADES, TWO SEMI-AUTOMATED WELD PROCESSES HAVE BEEN COMMONLY USED ON CODE QUALITY WELDS.
The two most utilized, Semi-automated arc weld processes used on Code welds, have been the EP, reverse polarity GMAW (MIG / MAG) and the Gas Shielded Flux Cored process. With these two weld processes, once three simple weld parameters were learnt, (to learn, visit my MIG – FCAW self teach / training process control resources) per wire diameter used, the optimum wire feed rate and weld voltage was set for the continuous fed weld wire. The welder would then press the gun switch and then direct and guide the gun to where the weld was required. However the reality has been for seven decades, that in contrast to any of the 2020, available sophisticated EP Pulsed MIG power sources, with their wide variety of weld transfer modes, or with any available gas shielded flux cored or metal cored wire, that in contrast, the higher weld energy DCEN TIG process, with it’s inert gas protection, the TIG process has been the process to go to when the highest manual arc, code weld quality was desired.
TIP TIG IS A PROCESS THAT DRAMATICALLY ELIMINATES ALL POSITION WELDER SKILLS: In contrast to GTAW and also MIG and flux cored, from root to fill passes, when using the semi-automated TIP TIG process, the weld shop simplifies all position welder skill requirements and of course eliminates many of the individual manual DC GTAW welder skills. Also TIP TIG, eliminates common concerns for the MIG – Flux Cored Wire Stick Out, (WSO) variations, that influence the weld energy produced.
ALWAYS SUPERIOR QUALITY WITH IMPROVED WELD CONSISTENCY AND UNIFORMITY. 200 TO 400% INCREASE IN GTAW PRODUCTION, AND ALWAYS HIGHEST POSSIBLE MECHANICAL PROPERTIES SHOULD WAKE UP ANY MANAGER OR ENGINEER INVOLVED WITH WELDS. With TIP TIG the weld wire is continuously directed into a unique upper plasma sweet spot. The position enables the highest possible plasma energy coverage over the weld, which in contrast to manual DC TIG, enables the ability to consistently deliver more weld wire and attain higher weld energy that always delivering the highest possible quality weld in an inert atmosphere, that’s more consistent and uniform, than manual GTAW. And lets not forget, with the increased TIP TIG weld travel rates and EN polarity, for the first time in arc weld history, the weld shop has a manual or automated arc process that should always attain the lowest distortion, the least weld / part stresses, and the highest possible welded part metallurgical properties.
TIP TIG, patented, Semi-automated Wire Feeder for either Manual or Automated arc welds. A brilliant mechanical action is the heart of the Austrian,TIP TIG, Plasch, Austria patent. There are cheap copies and the way to test them is in all position weld capability with the deposition rates attained. TIP TIG no magic electronic bells and whistles or the usual exaggerated weld sales claims, just a simple, wire feed mechanical action combined with AC Hot Wire current.
WIKEPIDA ADDS TO PROCESS CONFUSION THAT’S WITH THIS PROCESS IS COMMON THROUGHOUT THIS GLOBAL INDUSTRY; 2020 Note: Wikipedia and the majority of weld decision makers around the globe that I have followed that have been discussing the TIP TIG process, have for the last decade, an incorrect concept of the TIP TIG process, or have been providing incorrect descriptions of TIP TIG. As you are likely aware, in pulsed MIG, Reverse Electrode Positive, the electrons travel from the negative metal across the arc plasma and collide with the gas molecules and deliver around 70% of the plasma energy to the tip of the positive , continuous fed, MIG wire tip. An important note, the CV MIG welder can influence the weld transfer modes, short circ. globular or spray through changes to gas mixes utilized and the wire feed rate and volts. With Pulsed MIG the power source can also influence the weld drop size, and the rate of weld droplet detachment through the pulsed MIG parameters.
In contrast to the semi-automated pulsed MIG transfer, both the traditional DCEN GTAW, and DC TIP TIG circuit have a completely opposite function. With DCEN TIP TIG and DCEN TIG, first arc temperatures are far greater than possible with a MIG arc. The TIP TIG electrons travel from the tip of the negative tungsten to the positive ground. The electrons in the arc, apart from colliding and breaking the larger argon gas molecules for a high temperature plasma, provide the energy necessary to melt the weld wires. While TIP TIG is a semi-automated weld process, in contrast to MIG, most of the influence of the TIG power source is on the weld rather than on the wire running into the weld. Adding a Hot Wire current in the TIP TIG wire speeds up the weld melt, and using pulsed and variable polarity will also effect both the wire melt and weld.
As the TIP TIG wire melts, it forms droplets on the continuous fed wire tip. The key question is, what can be done to enable those weld drops to detach in a rapid manner before the continuous fed TIP TIG wire and drops make contact with the weld and disrupt the wire / weld transfer. The patented TIP TIG wire vibration, enables the weld droplets to detach and cross the arc. In contrast to DC TIG, the TIP TIG process allows much more weld wire to be deposited, which like a domino effect, enables more weld current to be used, and this influences both the plasma and weld?
Thanks to the Austrian, patented, Plasch invention, the TIP TIG wire vibrates, and like a plucked guitar string it agitates the wire so as the continuous fed wire exits the copper tip, the wire agitation “encourages rapid weld droplet detachment” from the wire. The more weld wire that can be delivered into the plasma, and on average TIP TIG delivers approx. 200 to 400% more weld than is possible with any GTA weld, the higher the weld current that can be utilized for the welds. The use of Hot Wire current also slightly decreases the time required for the molten welds drops to form. That increased weld current influences the weld energy and also increases the TIP TIG arc plasma density and width. These attributes reduce arc length sensitivity enabling TIP TIG to also be an excellent automated process without the concerns for arc length sensitivity, a common issues with GTA automation.
Since the 1940's, there has never been an arc weld process that provides the weld energy and welded part metallurgical benefits that can be attained with either the manual or automated TIP TIG process.
UNIQUE ATTRIBUTES OF THE TIP TIG PROCESS
IN THE LAST DECADE, MANY OF THE WELD DECISION MAKERS THAT ARE EASILY INFLUENCED BY A WELD SALESMEN, THOUGHT THE SOLUTION TO IMPROVING THEIR CODE QUALITY WELDS, WOULD EVENTUALLY COME FROM IMPROVEMENTS WITH THE PULSED MIG PROCESS.
Many weld decision makers in this industry believed in the 21st century, that with the never ending electronic bells and whistles they see added to the semi-automated Pulsed GMAW (MIG) process, that the Pulsed MIG would eventually provide the manual and also automated weld solutions to consistently enable all position code quality welds that don’t require weld rework. The weld reality is just as a donkey can never be a race horse, the pulsed MIG process will never have the unique weld process characteristics that is necessary to attain the weld quality and part metallurgical properties that can be attained with another semi-automated process called TIP TIG.
In my roles as both Corporate Product and Training managers with Linde, Airgas, AGA, ABB and Liquid Carbonic. I have been evaluating Pulsed MIG equipment from all the major GLOBAL Pulsed MIG mfgs. since the early 1980’s. And in the 1990’s, in my 600 page book “A Management and Engineers Guide to MIG” (training Resource Section) I wrote over a 100 pages on the issues with Pulsed MIG, and the reality is in 2020, that most of my 1980s pulsed MIG concerns are still relevant, however no one reads the book.
Note: For those interested in the extensive weld issues generated with Pulsed MIG especially in robot cells, you may wish to visit my MIG process / equipment sections at my weldreality.com site. or purchase one of my MIG weld process control self teach / training programs, also visit the TIP TIG versus Pulsed MIG section here.
The weld shop should be aware that if DC TIG, Pulsed MIG and Gas Shield Flux Cored is not attaining a weld quality in which zero weld rework is produced, with TIP TIG it’s easy to attain these weld results. The weld shop should also be aware with TIP TIG one TIP TIG welder will on average in a shift do the welds that three GTAW welders will do, and with TIP TIG there is no weld application size or part thickness limits.
TIP TIG All Position Welds are Easier than GMAW
REAL WORLD WELD BENEFITS FROM TIP TIG: With TIP TIG, no manual wire to feed and no amp foot control required. TIP TIG always superior control of arc starts – stops. TIP TIG no spatter, no weld fume concerns and no weld rework. With TIP TIG the smallest weld HAZ is produced with the least stresses and distortion. With TIP TIG always the highest weld and part metallurgical properties. Yes it’s an expensive process but the weld cost savings from no rejects or rework along with the dramatic reductions in welder skills and increased GTAW productivity and the cost is quickly justified.
As with any costly equipment to be used in a weld shop, the TIP TIG process of course requires cost justification, and it’s logical that weld shops during a TIP TIG demonstration should want to see and measure the improvements and cost reduction capability that will be provided by TIP TIG;
- With a short training program that should be presented not only to the welders, but also to all those that make weld decisions. (see my low cost TIP TIG training / self teaching power point programs), TIP TIG dramatically reduces all position welder skills, which enables increased and more consistent, uniform weld quality. In contrast to TIG – Pulsed MIG and Flux Cored, R
- The TIP TIG all position welder skill reductions dramatically reduces welder training times.
- TIP TIG dramatically improves both DC and AC TIG weld quality.
- TIP TIG enables more weld current than GTA welds which when combined with the unique TIP TIG wire placement produces a higher energy plasma with increased plasma coverage over the weld. Weld fusion is the highest possible with the lowest possible weld porosity.
- Weld quality is further improved from the TIP TIG consistent wire feed placement to the plasma sweet spot which enables the continuous, uniform melt of small weld drops that provide increased weld fluidity.
- In contrast to GTAW, with TIP, arc start – stops are dramatically reduced and with decreased arc length sensitivity their is less opportunity for tungsten contamination and tungsten melt.
- TIP TIG enabling on average 200 – 400 % more weld than DC TIG, enables increased weld current capability, and faster weld speeds, reducing weld costs.
- TIP TIG greatly extends the weld application potential and no job is to small, thin, large or thick.
- Be aware that for 5 – 6G pipe welds, the TIP TIG manual fill pass weld speeds would be similar to pulsed MIG.
- TIP TIG increased welds speed capability with electrode negative polarity dramatically lowers the welded part heat, which always enables superior welded part properties, with no concerns for carbide precipitation that affects corrosion, or concerns for weld stresses, part distortion and weld fumes.
- TIP TIG eliminates arc length sensitivity concerns, making it suited to all manual semi-automated and fully automated applications.
- TIP TIG enables the following results on the stainless fillet in the video below, The weld produced process attributes that no weld shop can produce when using DC TIG or any Pulsed MIG process.
With the above TIP TIG stainless gauge fillet weld, note the weld color, lack of oxidation, no spatter, and small HAZ that results from the lowest possible weld heat into the parts. Note how the welder can hold the TIP TIG torch just like a GMAW gun or if required like a GTAW torch. As with any semi-automated arc weld process, on parts with decent fit, with TIP TIG no weld weaves or skipping techniques should be used when making single pass fillet or lap welds up to 7 mm.
With TIP TIG, you have the best of both worlds, for groove or fillets, you can either rest the ceramic torch nozzle in a groove or on the plate, and if you walk the cup which adds to the simplicity and control of all position welds. Or the welder can hold the TIP TIG torch and weld like a MIG weld.
Again take a moment with the above video to examine the untouched stainless weld surface quality. Carefully examine the silver weld color, (lack of oxidation) attained that’s a benefit of EN polarity and increased weld speeds that result in the lowest possible weld heat input. Also then examine the weld fluidity continuity on the weld surface and toes, that reflects on the high weld energy attained. Note with the extremely small HAZ produced, a benefit weld shops can anticipate with any stainless welds, therefore the lowest distortion should always be attained. And with some stainless grades, with this process, anticipate the least opportunity for carbide precipitation. Also note the respectable weld speed being attained, (as quick as MIG) , and in case anyone is interested also note in the video as well as the photo, no visible stainless, carcinogenic weld fumes.
2020: MY MESSAGE TO THOSE NORTH AMERICAN AND EUROPEAN WELD – METALS CODE / SPECIFICATION COMMITTEE MEMBERS THAT APPEAR TO BE STUCK IN A COMA DURING THE LAST DECADE: Of course it’s appropriate that weld process information and metal guidelines should be kept up to date by the major Code bodies such as ASME – AWS – API – ASTM – ABS – NAVSEA. Unfortunately these N.American Governing bodies and their engineer committee members are in 2020, now ten years behind the capability of a process such as TIP TIG.
- TIP TIG will dramatically change the recommendations and guidelines that have been provided in the last seven decades. From my perspective, when it comes to comparing the common arc weld process’s that account for most code welds, GTAW – FCAW and GMAW , the code providers are not aware that when TIP TIG is utilized, major changes will be enabled.For example;
- Preheat, inter pass and post heat treatments are typically dramatically reduced or no longer required.
- Weld groove preparation dimension recommendations can be dramatically reduced. For example from the typical Vee-grooves of 60 plus degrees, to 40 to 50 degrees.
- Costly NDT weld inspection requirements should be reduced or elminated.
- There will be less concern for HAZ changes, impact properties will dramatically increase.
- There will be less concerns for cracks, stresses and distortion.
- There should be minimal concern for Carbide Precipitation or other corrosion issues.
- In clad welds, the weld layers can be reduced as a result of less alloy loss.
- Many Titanium welds will not require trailing shields.
Yet all I have heard since I introduced TIP TIG to N.America in 2009 is SILENCE. Which is again a reflection of where we are as an industry.the
WHEN TIP TIG IS BOUGHT INTO THE WELD SHOP AND ALL WELDERS THAT USE THE PROCESS ARE PROVIDED WITH CORRECT TRAINING (SEE MY MY 3 HOUR TIP TIG SELF TEACH / TRAINING PROGRAM) IN MY TRAINING RESOURCES, MANAGERS SHOULD EXPECT THE FOLLOWING BENEFITS?
- TIP TIG enable the best possible, manual and automated all position, consistent arc weld fusion, with the cleanest welds with the lowest porosity, so informed plant engineers or mangers should expect NO WELD REJECTS OR REWORK on any metals and code quality applications.
- TIP TIG provides optimum automated weld capability without arc length sensitivity concerns that are common with the Hot Wire process, so simply connect that TIP TIG torch to a robot, a carriage or rotary positioner.
- TIP TIG is the easier to use than the TIG – GMAW – FCAW process on all position code welds, and also enables the best possible root and fill weld quality. So on most pipe welds or welds with roots, instead of using two weld processes with TIP TIG you have one process that’s suited to any gauge, any thickness, or any size.
- TIP TIG produces code welds without spatter, and welds with the lowest oxidation that should not require grinding or cleaning.
- TIP TIG also enables the lowest possible weld fumes. If you weld any metals that have fumes or grinding dust that you don’t want to subject your employees to, you now have a weld process solution.
- TIP TIG always provides the lowest possible welded part heat input, the least distortion, the lowest weld stresses, the best possible mechanical and corrosion properties, and that applies to all metals.
Take another moment with the close up of the TIP TIG arc and weld.
- Note below the vert up, continuous highest possible arc weld energy, enables from increased DCEN current from higher deposition and smaller filler wire capability, and from the wire to plasma placement that enables full plasma coverage over the pool.
- Note the highest possible weld fluidity, a fluidity that is not inhibited by the already small fluid weld drop additions to the weld.
- Note the weld metal purity from the combination of highest arc energy capability protected by the inert atmosphere. Any weld person would know simply by looking at this weld that the weld would be defect free. This weld can not be duplicated with any Pulsed MIG or GTA weld.
Remember with any arc weld, the best possible code weld results will come from a weld process that provides FOUR prime weld functions;
- A weld protected by an inert atmosphere.
- An arc plasma that provides the highest weld energy.
- An EN polarity that enables a fast freeze weld making it easy to use for all positions.
- A deposition that enables good welds speeds in combination with an EN polarity that enables the lowest welded part heat input.
TIP TIP ENABLES SIMILAR VERTICAL UP WELD SPEEDS TO PULSED MIG. TIP TIG typically delivers 200 to 400% higher weld deposition rates than DC TIG and produces similar vertical and overhead weld travel rates as pulsed MIG. Another point, In contrast to traditional GTAW, both the DCEN & also Variable Polarity used for aluminum welds, TIP TIG continuously feeds the commonly used 0.035 – 0.045 (1 – 1.2 mm) diameter weld wires into the TIP TIG plasma sweet spot.
When TIP TIG is used on clean applications such as this Super Duplex fillet weld, note the untouched TIP TIG weld color which reveals lack of oxidation influence with the atmosphere. This is only possible with very low welded part heat input. With TIP TIG, weld shops should always anticipate the cleanest, defect free welds that produce the smallest weld HAZ, and this applies to most weld applications > 2 mm. Note try and replicate the fillet on on the left with either a duplex, stainless or inconel weld wire and the process of your choice.
CONSISTENTLY ATTAINING OPTIMUM UNIFORM WELD QUALITY & WITH THE LOWEST WELD COSTS, SHOULD BE OF INTEREST TO ANY GLOBAL WELD DECISION MAKER.
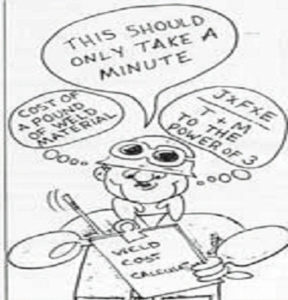
2019: I am aware that the technical weld process process details at this site may not get everyone as exited as I get when discussing TIP TIG versus the AC/ DC GTAW, Pulsed MIG, Gas Shielded Flux Cored and also the automated Hot Wire TIG, however most weld shops do have a great interest in two subjects WELD QUALITY AND COSTS.
With this in mind, I will start in the first following paragraph discussing some of the unique TIP TIG weld COST reasons that any company that is using DC TIG – MIG – Pulsed MIG or Flux Cored for code quality welds on steels, alloy steels, alloys and also specific AC TIG & MIG Aluminum applications, simply cannot afford to ignore.Please don’t forget that weld costs are of course influenced by weld deposition rates, weld rejects, weld rework, weld cleaning, by the welder’s skills, and by additional material costs or material handling.
Weld shops take note: The traditional arc weld processes such as AC/DC TIG, Pulsed MIG, Flux Cored or the SMAW process, require higher all position welder skills than required with TIP TIG.
As most in this business are aware, when hiring GTA welders;
[] the slow weld speeds and cost consequences,
[] the never ending weld start and stops ,
[] the many trips by the welders to the grinder to reshape and replace tungsten,
[] as GTAW welder skill requirements change from one welder to another, this and above have a major influence on both the GTA weld quality and the hourly labor costs generated.
If you were stand in any Aerospace plant and watch 5 TIG welders produce similar welded parts, and you will note that their different manual welder skills and weld practices are influencing the lack of GTA weld uniformity, continuity that results in the too often inconsistent weld quality attained,
THE FREQUENT TUNGSTEN CHANGES WITH TRADITIONAL DC TIG WELDS DO NOT OCCUR WITH TIP TIG :
As mentioned, DC TIG welders have to place their weld wire in front of the weld in a very small, fast freeze weld pool and often that wire or weld pool will touch and contaminate the tungsten, lowering the tungsten melt temperature and changing its required profile. The welder will then stop welding and replace their tungsten and create another weld start / stop which are common weld defect locations. When large amounts of AC/DC TIG weld are required, those tungsten changes will be very frequent. In contrast, the TIP TIG wire is fed to the side of the TIP TIG arc plasma and therefore its more difficult for the TIP TIG weld to contaminate a TIP TIG tungsten. Once this process is learnt correctly and especially the unique the TIP TIG Best weld practices the welder will likely have no more than one or two tungsten changes per shift.
SO LETS LOOK AT THINGS THAT INFLUENCE WELD DEPARTMENT BUDGETS WITH A CHANGE TO TIP TIG:
It would take me about an hour to prove the following statement. “In a weld shop that employs mostly DC TIG welders, with a change to the TIP TIG process, that weld shop should anticipate at least a 65 to 75% annual weld labor cost cost reduction in their weld department budget. As for those weld shops that utilize pulsed MIG or gas shielded flux cored on code quality weld applications, most of the weld shops will budget for weld rejects or weld rework. In contrast, with TIP the weld shop can anticipate no weld rework. The TIP TIG weld deposition and weld travel details that greatly influence weld costs are well documented at this site, however I want to get across both the the extensive weld costs savings potential and weld quality improvement impact with a change from regular DC TIG to TIP TIG and this applies to any company that provides Code Quality steels, alloy steels, alloys and also many aluminum weld applications.
The following info. provides how I attained an average of 70% hourly weld cost reduction with changing from DC GTA to TIP TIG.
DC TIG TO DC TIP WELD COST REDUCTION: Lets take a Fortune 500, Aerospace corporation that has many global plants that employ manual DC TIG welders for code quality weld applications, call it PLANT 1. This plants employs 10 DC TIG welders, five on each shift. The plant also employs two weld shop supervisors to manage the two shifts. The Aerospace TIG welders earn $30 /hr, and mostly weld steels and alloy steel code applications. This companies typical welder labor costs $60,000.00 / yr. The welders benefits are $8,000 / yr. Also as TIG is such a slow process, overtime is the norm. The average overtime per-TIG welder was 10 hours a week at time and a half, 10 x $45 hr = $450 x 50 weeks = ($22,500 / year). The annual TOTAL weld labor costs for the aerospace company is $90,500.00 per/welder x 10 welders. Also add two weld supervisors at $80,000 /yr, with the supervisor combined annual salary of $160,000.yr. The total weld labor cots for this Aerospace weld shop is $1,065,000. The TIG weld equipment investment for the 10 welding units, approx. $78,000.
COMPARE ABOVE PLANT 1 WITH WITH TIP TIG WELD LABOR COSTS IN PLANT 2:
Now for those still hanging in there, first thanks for your patience. The above aerospace company changes to TIP TIG. At PLANT 2, instead of the 10 DC TIG welders, all this company would now require to achieve the same weld production with superior weld quality , would be three TIP TIG welders and one supervisor working one ONE shift. Three TIP TIG welders wage plus benefits, 3 x $68,000 / yr = $204,000 / yr, plus one supervisor $80,000 / yr, producing a yearly TIP TIG WELD LABOR costs of $292,000. By the way with TIP TIG you would also reduce the annual argon TIG gas cost in the range of 50 to 70% , and also take approx. 15 – 30% of the weld wire costs. The TIP TIG equipment costs depending on the power sources available in the shop would be in the range between $50 to $80K. As you you can see with the added weld consumable savings, its easy to anticipate at least an annual TIG labor cost savings of 70% would be anticipated.
The above annual DC TIP TIG weld shop wages total is $292.000. The annual DC TIG weld shop wage $1,065.000.
A GTAW Weld Cost Question: Em, as weld deposition rates are a large factor in weld shop costs, can you provide more detailed info. on the typical average weld deposition rate capability with manual DCEN TIG welding?
Regular DC TIG Weld Cost Answer:
Welding a 3/16 horizontal fillet, the DC TIG manual welder on average would feed a common 3/32 steel or stainless TIG wire into the weld pool at approx. 8 inch minute, (20 cm/min). This wire feed rate delivers just less than 1 lb/hr with 60 minutes arc on time. Lets say the average arc on time per/hr for a TIG welder may be around 20 minutes delivering approx. 0.3 lb/hr.
If a TIG welder decided to try and feed a smaller 0.035 (1 mm) wire, with an 0.035 steel or stainless wire, the welder would require that the DC TIG welder continuously feed the 0.035 wire at around 70 inches per-min, (not going to happen with traditional TIG).
TIP TIG Weld Cost Answer: On the same weld, the TIP TIG welder would set an 0.035 wire feed rate of around 150 inch/min, approx 2.2 lb/hr, As TIP TIG increases the arc on time to lets say 30 minutes per-hr the TIP TIG welder is depositing 1.1 lb/hr, so you can see with this conservative TIP TIG setting the TIP TIG welder is putting in 200% more weld and depending on the weld application, the TIP TIG process will readily provide a 300 plus percent increase in weld than is possible with the DC TIG welder.
I HOPE YOU ARE NOW ALL WELL AWARE THAT TIP TIG IS UNTOUCHABLE FOR ALLOY WELDS, BUT WHAT ABOUT THE COST SAVINGS FOR A SIMPLE CARBON STEEL PIPES WELD APPLICATION?.
As reported by a TIP TIG user. Our customer ordered plain carbon steel pipe assemblies from the weld shop used in heating system. This was a first time that they had used TIP TIG for any welding application. The biggest pipe was 8 inch diam with a 1/4 wall.
With regular DC TIG it took around 90 minutes to complete the pipe welds from root to cap and this was done with 3-4 passes depending from the welding position. With TIP TIG the same pipe welds with made two weld passes and in 30 minutes. As for the weld quality, 100 % x-ray was used on the welds. With regular TIG this company would often find minor defects and with X-RAY evaluation pipe weld rework was common. In contrast with the TIP TIG welds there was absolutely nothing shown on the X-rays. The X-ray were taken with digital equipment so they were able to zoom in and check everything very precisely. So the weld shop attained far better quality, extensive increased production, and this was within the first two weeks of purchasing the TIP TIG equipment.
Note: Please keep in mind, that with all position code quality weld applications as in pipe and vessel plants will also employ Pulsed MIG welders. You may be surprised to know that the weld deposition rates for code quality vertical up and over head pulsed MIG welds are quite similar to the deposition rates attained by TIP TIG, however the pulsed MIG weld quality will be inferior with special concerns for the weld fusion, the weld heat, porosity and weld fume concerns. Of course for horizontal fillet welds the pulsed MIG process will enable dramatic deposition rate increase, but again with the quality, heat and fume concerns.
IMPROVED WELD CONTROL COMES WITH DRAMATICALLY REDUCING ALL POSITION WELDER SKILLS AND ALLOWING TWO HANDS ON THE TORCH:
If the above was welded with DC GTA, the welder would have one hand on the torch, the other hand to feed the wire, and maybe one foot on the amp control.
If the above was welded with pulsed MIG, apart from the inferior weld quality especially with the sluggish stainless, the MIG welder would have to deal with weld fumes and spatter.
- With TIP TIG code quality all position welds, and the rapid freeze characteristics influenced by the EN polarity, the weld pool is easy to control and the welder skills are dramatically reduced. Also one or two hands can be used to hold the TIP TIG torch and the TIP TIG welder does not require a foot amp control.
- Irrespective of a person’s background, the TIP TIG process is easy to learn in a few days, that is if the correct settings and best weld practices are taught, (available at this site). This is a process that will reduce the concerns for skilled welder shortages, and reducing welder skills will affect weld labor costs.
- Reducing welder skills also enables higher weld quality, especially when the weld shop employs more than one welder and wishes to produce uniform, consistent optimum manual weld quality.
- Don’t forget that the TIP TIG weld wire is continuously fed into the plasma arc sweet spot. This wire feed feature, drives consistent, uniform weld melt that enables consistent weld fusion, decreased weld porosity, and enables improved control of the weld travel rates.
- In contrast to a manual DC TIG weld, typically no more that two weld settings are required for the weld wire diameter utilized. And TIP TIG weld arc starts and stop parameters are automatically controlled, to a weld quality level that will never be available with any TIG, Pulsed MIG or Flux Cored weld.
- With TIG welds, there are often many weld arc start / stops influenced by the manual wire delivery that affect both weld quality and productivity, solution provided by TIP TIG.
- Instead of using DC TIG and then adding another weld process to complete the welds, such as TIG and Pulsed MIG, with the TIP TIG process, the weld shop requires one weld equipment package, one weld wire, one gas for any pipe root to fill, or for any all position welds on any metals, and on welds with any thickness. One process one skill set.
Of course many welds don’t require the TIP TIG process: If welds are made on parts in which “internal” code weld quality evaluation is not required, or on parts with mill scale, coatings and contaminates in the weld area, then MIG and flux cored would be a more appropriate weld process choices. However if they are not code quality welds and if weld spatter, weld cleaning or weld fumes is a concern, consider TIP TIG.
PIPE ROOT WELD OPTIONS: Three decades ago, I manged a pipe weld project, training Imperial Oil, (Exxon) union pipe welders, Tar Sands Alberta Canada. Left, Ed checking the MIG root weld issues generated with with different MIG weld transfer modes.
Imperial Oil was looking to create dramatic Nat Gas pipe line weld cost reductions, and I was contacted to first train the “we love our SMAW weld process” sub-contractor, manual pipe welders on how in the 5G pipe position, for pipe root welds to use the semi-automated Lincoln MIG STT process, (in reality a simple low pulsed MIG mode), and also the Miller RMD (reduced SC current) process. And for their shop welded rotated pipe joints, teach the welders the process controls – best weld practices with the conventional MIG Short Circuit mode.
After the 5G Exxon pipe welder root training, I provided the same welders gas shielded flux cored process control – best practice, 5G pipe fill pass training. At that time, the Oil & Nat Gas industry did not have an extraordinary pipe weld process such as TIP TIG which was all they would have required for root and fill passes. And its perhaps a reflection of the general weld engineering apathy found in the Oil – Nat Gas industry, that in 2020, ten years after I introduced TIP TIG to N.America and Australia, that most weld engineers and relevant managers in this industry, still know little about the TIP TIG process.
On a pipe projects like the above, if the welders used TIP TIG, they would have;
- only required one weld process for all root and fill passes,
- only required one gas,
- only required one weld wire,
- only required one weld procedure with two simple weld settings.
- have had the ability for zero weld rework.
- would have attained the highest possible impact properties, a necessary requirement for Alberta.
WELD REALITY: The most popular Semi-automated MIG process for Pipe Root Welds is MIG. First it was MIG Short Circuit, followed by MIG STT and MIG RMD, for the root, and then another process such as flux cored or pulsed MIG for the fill passes. The reality is no other arc weld process can compete with TIP TIG in terms of capability and quality on code quality welds.
Linclon MIG STT Left – Miller RMD right. Both attaining acceptable 5G root, vert down weld results. If I had to GMA a pipe root today I would use an OTC pulsed unit.
Ed Training Exxon / Imperial Oil pipe welders on the different MIG weld transfer modes available to weld Nat Gas Pipe. Pipe weld shops need to be aware that when they use MIG Short Circuit for rotated pipe root welds, or use MIG STT or MIG RMD for the all position pipe root welds, in contrast to TIP TIG they are using inferior arc weld processes that are not only sensitive to wire stick variations, but also sensitive to root weld gap and root alignment variations. That sensitivity is not part of the TIP TIG process
Pipe, plate, vessel, valve, tank welds when the best possible weld quality is required, from the root welds to the fill passes, TIP TIG would always provide all position fill weld passes with superior mechanical or corrosion weld / part properties, and all the QA department would have to do is document the passed welds.
What about Gas Shielded Flux Cored Welds? There are many reasons why an experienced weld engineer should be nervous about allowing gas shielded flux cored welds on code quality applications in which the internal quality of each weld is closely evaluated. And there are many reasons why the weld shop should not be surprised on any code quality all position welds, when the flux cored welds that are made by a highly skilled welders looks like this.
The Gas Shielded E71T-1 Flux Cored process does not need a welder to be responsible for generating weld defects.
If you are aware of the weld process controls and best weld practices associated with Gas Shielded Flux Cored, (as taught in my process control programs), you would know what was the prime cause of the common issue.
With code quality welds, and the traditional arc weld processes, such as flux cored, pulsed MIG and SMAW, there are many reasons beyond the welders control, why managers, engineers and supervisors cannot get a good nights sleep.
MOST EXCELLENT LOOKING MIG FILLET WELDS, WHEN MACRO EXAMINED, WOULD REVEAL MARGINAL SIDE WALL WELD FUSION
What makes TIP TIG a superior weld process than Pulsed MIG or Gas Shielded flux cored for vertical up and over head welds?
An easy way to explain why the Reverse Polarity MIG and Gas Shielded Flux Cored process will often leave welds with lack of weld fusion, especially with vertical up and overhead welds on parts > 5 mm thick. Both MIG and gas shielded flux cored arc temperatures are almost 50% of a DC TIG weld. And with the Reverse Electrode Positive MIG and flux cored welds in which most of the arc energy plasma is used to melt the continuous fed weld wires, they simply do not have the required weld energy for the welds the weld mass delivered, and the weld deposition rates delivered that influence the weld travel speeds generated which influence the weld solidification rates. The bottom line is MIG and flux cored cannot generate the weld fluidity that’s created by a DC Electrode Negative TIP TIG weld.
As for weld purity which influences weld porosity and oxidation buildup, both MIG and flux cored use reactive gases such as CO2 and Oxygen which add to the weld porosity formation. And when gas shielded Flux Cored is selected for code applications weld shops should be aware that with this process, there can never be a guarantee of not getting trapped weld slag, worm tracks influenced by moisture and excess porosity. When you add the common weld defects found with flux cored or MIG, along with the concentrated weld heat around the weld wire tip influenced by reverse polarity, you will have questionable weld quality results and also welds that have large weld heat affected zones. Therefore, when it comes to code welds, the semi-automated MIG and flux cored weld processes simply cannot compete with the semi-automated TIP TIG process.
Note: Be aware that the typical increase in weld deposition rates that are attained from TIP TIG, the weld shop, typically will provide all position TIP TIG travel rates that are similar to those attained with pulsed MIG process. |
FOR THOSE MOSTLY IN EUROPE, PLEASE NOTE THERE IS ENOUGH WELD PROCESS CONFUSION AROUND THE GLOBE. TIP TIG IS NOT A HOT WIRE PROCESS, OR A PROCESS PRIMARILY INFLUENCED BY AN AGITATED WELD.
Simple solutions are often the most effective inventions. It took almost 70 years before an Austrian engineer called Plasch, figured out the solution to make traditional TIG into an easy to use “semi-automated” or “automated” TIG process. It was an invention that got me so excited when I first saw it in Europe, in 2008, that when I should have been thinking about retirement, I bought this process to N. America and then with my business partner Tom O’Malley we introduced it to Australia.
The continuous fed TIP TIG weld wire is fed through a set of “patented wire feed drive rolls”, that through a mechanical action, the rolls go back and forth with rapid velocity. The drive roll action on the weld wire creates a continuous wire vibration, that when viewed, is similar to a plucked guitar string. The wire vibration enables rapid detachment of the agitated, fluid weld drop formed on the weld wire tip.
The TIP TIG process also utilizes a small HOT wire power source in which typically 80 to 120 amps is used solely to preheats the weld wire. This preheat decreases the time required for the wire to melt as it approaches the plasma. The patented TIP TIG wire feed, in combination with a suitable 300 to 500 amp DC or AC/DC TIG Power Source, plus the unique TIP TIG Torch and Hot Wire power source provide the TIP TIG process that enables;
So what does the TIP TIG Equipment enable for the Weld Shop?
- TIP TIG enables the use of common MIG wire diameters to be used, 0.035 and 0.045 most utilized.
- TIP TIG enables 200 to 400% more weld each hour than TIG.
- The hot wire AC power source preheats the TIP TIG weld wire (same as Hot Wire TIG) which reduces the energy required to melt the wire tip.
- The continuous fed weld TIP TIG wire in contrast to manual GTAW. delivers the wire to different plasma position that allows all of the plasma energy to cover the weld surface.
- TIP TIG creates a weld wire vibration that agitates the weld drops enabling rapid weld drop transfer.
- The small TIP TIG weld drops are fluid before entering the weld.
- The size of the small weld drops and the weld drop to plasma position reduces the chance of the drops and weld contaminating with the tungsten.
- The weld droplet agitation also creates a very slight agitation of the weld which in some cases can enables a slight increase in the weld solidification time.
- The increased weld wire deposition rates, enables increased weld current which further adds plasma energy to weld.
- The faster TIP TIG weld speeds with the Electrode Negative Polarity rapid weld heat conductivity into the part enables dramatic reductions in welded part heat, to a level never attained with any manual arc processes.
- The increased and uninterrupted TIP TIG plasma energy that creates a plasma that is more dense and wider than a TIG plasma enables improved electron transfer that decreases arc length sensitivity benefiting manual welds and enabling TIP TIG to be used with any automated equipment without purchasing automated arc length adjustment equipment.
- And for those weld shops thinking about purchasing exhaust equipment, they may want to reconsider if they use a weld process in which on clean metals it;s difficult to see the weld fumes.
- What happens with no wire vibration? Without the wire vibration, you have a Hot Wire Feed unit and you could not place the wire in the plasma position enabled by TIP TIG, a position that enables full plasma coverage over the weld. Without the wire vibration, the weld drops could grow larger in size, be more erratic, or detach at an irregular rate that would disrupt the weld.
- And for those individuals that call TIP TIG a Hot Wire process, the Hot Wire process has been available for many decades. and the bottom line is this. The Hot Wire process is a process in which typically the continous fed weld wire has to be fed behind the arc, and while well suited to automated GTAW welds often with automated arc length control equipment, is simple not capable of producing the MANUAL semi-automated welds produced by TIP TIG. Visit the Automated TIP TIG section for more info on Hot Wire Vs TIP TIG.
Anyone who welds alloys this thick should ask why is this 6 mm 316 stainless fillet weld gold in color?
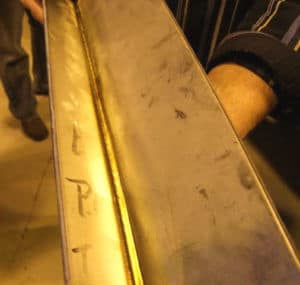
THE IMPORTANCE OF PRODUCING THE LOWEST POSSIBLE WELD JOULES:The worlds most widely used arc weld processes, MIG and Gas Shielded Flux Cored use Reverse Polarity with Electrode Positive. This is a polarity that concentrates the majority of the weld plasma heat in the upper portion of the plasma, around the continuous fed weld wire tip. This concentrates the energy in the upper portion of the plasma and this energy concentration can create large weld heat affected zones.
For almost 75 years, the traditional DC Electrode Negative TIG process which directs the majority of the TIG arc plasma energy towards the positive, large conductive mass of the parts welded has rarely been able to benefit from the DCEN weld polarity. The reason is that on most TIG welds for the high weld heat generated is simple, traditional DC TIG welds on most parts > 2 mm, typically generates very low weld deposition rates and very slow weld speeds that help retain the part heat.
Perhaps someone could inform the Aerospace, Defense, Power and Oil company managers and engineers, that since 2010, there has been less concern for the negative influence of welded heat on alloys and high strength steels and aluminum, the reason. the TIP TIG process dramatically reduces the weld joules.
From a chart I made in my TIP TIG self teach / training program. Compare the heat input your weld shops are using when they weld. Impact properties, ductility, cracking sensitivity, elasticity, fatigue, hardness, malleability, toughness, yield and corrosion properties. All metals including aluminum benefit from a weld process, that puts in the lowest welded part heat input, provides the widest possible welded joules range and the highest possible weld quality.
Note; Its one thing to change the weld dynamics of an arc weld process and create a unique TIG / MIG like process like Plasch did, and its another thing to eliminate the extensive arc weld process confusion that will likely prevail around the TIP TIG process for many years to come throughout the global weld industry. Its also another thing to have the process expertise to evaluate the often subtle arc, plasma and weld transfer characteristics, along with the practical weld application benefits attained with a process such as TIP TIG and how it competes on code weld application against DC/AC GTAW, Pulsed MIG and the Flux Cored arc weld process. This is what I do.
Note: Please be aware my MIG Process Controls – Best Practice self teach and training program simplified the MIG process into an easy to learn “Clock Method” that delivers optimum settings and best weld practices for any CV – Pulsed MIG, manual or Robot applications.
SURELY THE EXPERTISE OF THOSE THAT ARE PROVIDING THE WELD PROCESS ADVICE IS RELEVANT TO A COMPANY THAT PRIDES ITSELF ON ITS WELD PROCESS EXPERTISE : In this business when someone gives weld advice, it’s beneficial to know the background of the person providing that advice. I have written three books on Manual – Robot MIG – Flux Cored – Weld Process Controls – Best Weld Practices. I wrote the MIG – TIG – Flux Cored and Laser sections in the USA Machinery Handbook. I wrote the Laser – Plasma – Oxy Fuel (Thermal Sections) in American Society Metals Book. Ninth Edition. I had 35 articles published on Weld Process Controls. I was a key member that wrote the AWS MIG Gas Specifications. I have four weld patents and along the way I provided weld advice for the Mar’s Orion Spacecraft. I was the Weld Manager in a ship yard and the Robot Weld Manager for ABB North America. I was a GE Black Corporate Belt Weld Engineer, and along the way I assisted approx. 1000 companies in 13 countries with their manual, automated and robot weld issues.
Thanks Darren. Around 2009, during a visit to England to assist a weld client with their sub-sea Hot Wire TIG valve weld issues, I was discussing the Hot Wire limitations when I heard about an exiting new TIG process. I eventually located the unique TIP TIG process at a rural facility in Scotland, and thanks to a young man called Darren Matherson, I was invited to his facility. Watching Darren use the TIP TIG process weld 1/4 (6 mm) stainless parts, it took me no more than 10 minutes to figure out the importance of this process especially for those that do code quality welds in North America and as I had a son in Australia land i also got the rights to introduce it there.
Note: I would appreciate if you want to reprint any of the unique data that’s written at this site. that when you copy the data and print it, you add before the data that “the source of this data is Emily Craig tiptigwelding.com” And if you want weld personnel to use the best weld practices and quickly attain the maximum process potential, “without playing around” with the weld controls from TIP TIG, or the Manual & Robot MIG – and Flux Cored processes, please consider my weld process controls – best weld practice self teaching / training programs.
INEXPERIENCED WELD MANAGEMENT: So why do I waste my breath on criticizing weld shop management, and also criticize N.American Navy and Ship yard management and Defense Contractors? Well first I am a taxpayer, and the last place I want to see billions of tax dollars spent is on unnecessary weld rework and poor weld productivity. Second, I used to take pride in N. American engineering capability, and the reality in 2020, while the US Navy will spend billions of dollars annually on complex engineered applications, yet when it comes to “welding,” it’s obvious that with the Navy weld and fabrication managers, along with their Fortune 500 contractors, that there appears to be a general lack of weld process Ownership capability, along with a lack of weld process controls and best weld practice expertise. This expertise is their missing link and it’s necessary for any company to achieve weld quality / productivity optimization, especially with the three semi-automated arc weld processes.
WHILE ITS BEEN MY POINT OF VIEW SINCE THE 1980s , RECENTLY THE ASSISTANT SECRETARY OF THE NAVY PROVIDED HIS CONCERNS ABOUT COSTLY WELD AND FABRICATION ISSUES, HOWEVER MOST OF HIS DEFENSE CONTRACTORS SIMPLY DON’T KNOW HOW TO RESPOND
For those not interested in my opinions, or my focus on the general lack of weld best practices and process controls expertise in Defense and Aerospace companies, they may however want to be aware of the the words of a Mr. Geurts, the Assistant Secretary for Research, Development and Acquisition for the US Navy. Mr. Geurts is responsible for spending approx. 205 billion dollars in 2020. Mr. Geurts spoke at a Defense One Tech Summit. The following is not word for word, but almost.
Mr Geurts states, “the US Navy can’t build our future planned fleet and attain the 355-ship fleet goal required by our national strategy, unless it finds ways to dramatically reduce both the ships and submarine build and repair costs”. He continues. Today in North America, when we look at our general lack of industry and Navy management & engineering Process Ownership, we need to go way beyond labor costs as the root cause of our weld / fabrication demise. Perhaps we also should spend a little more effort to examine our Engineering, Fabrication Process Expertise.
Response from Em. What Mr. Geurts stated above in 2019, is what I have been saying in my articles, web site, books,work shops and also with my MIG – Flux Cored weld process control training resources for at least 30 years. Of course I love his frank logical engineering message, but also I hope Mr. Geurts recognizes that one the most resistant organizations in the industrial world that is resistant to weld process change would likely to be the NAVY, and perhaps the Navy could lead by example.
WITH DEFENSE CONTRACTORS, THERE IS ALWAYS HOPE.
A 2016. E-Mail to me from a foreman at General Dynamics, NASSCO (Electric Boat) shipbuilding. Dear Emily. Having instituted your Weld Process Control – Best Weld Practice Flux Cored and MIG training programs at our NASSCO GD facility, I wanted to let you know the following results. At this location we are recovering from extensive, costly weld performance by our NAVSEA qualified weld personnel on a major, US Navy CVN contract. I was hired in the middle of this contract and unfortunately, like many naval yards there was endless weld problems. I implemented your flux cored training program and we have greatly reduced our flux cored weld problems. With your MIG & flux cored process control programs, we finally were able to understand that our “NAVSEA approved weld procedures were not optimum”, we were recommending very low MIG – Flux Cored weld parameters (outside your optimum minimum recommended range). We are now using your recommended weld parameters and practices and are now engaged in changing both our flux cored and MIG weld procedures also to your recommendations. Regards and thanks again. Foreman NASSCO.
Remember as you read about TIP TIG at this site, that I made this process available in the USA and Canada in 2009. And ironically I started the TIP TIG bushiness in a building in the middle of the Philadelphia Naval Yard surrounded by Navy key decision makers who when invited to my GMAW – Flux Cored or TIP TIG work shops, showed no interest in what was going on less than a hundred yards from their offices.