Steels & Alloys
All Metals Benefit From TIP TIG Welds
Written by Em Craig. For 70 years, the weld industry has never had an arc weld process that deals with all the issues that result from the traditional arc weld processes, (issues not caused by welders) that can occur with manual and automated code quality welds. Compare the arc weld processes used in your weld shop with the TIP TIG features, that will benefit all metals;
NO MATTER WHAT THE METAL WELDED IS, THE PRIME PURPOSE OF THAT WELD IS TO ATTAIN CONSISTENT WELD FUSION:
IN CONTRAST TO THE SEMI-AUTOMATED MIG, AND GAS SHIELDED FLUX CORED, THE TIP TIG PROCESS PROVIDES HIGHER WELD ENERGY THAT BENEFITS ALL WELDS: TIP TIG is the only manual, Semi-automated arc weld process available that allows the welder to Set the Desired Weld Current for the Fixed Continuous Wire Feed Rate. With MIG and gas shielded flux cored, it’s the slope out put of the traditional CV MIG power source that determines the weld current provided. For example, if I was to use a CV MIG power source with an 0.035 ( 1 mm) MIG wire set at 250 inch, that wire feed rate would typically draw around 160 – 170 amps. In contrast, with a TIP TIG weld that enables a far greater arc temperature, again using an 0.035 (1 mm) wire, that’s fed set at 250 inch/min, the TIP TIG weld could readily be produced with 200 to 350 amps. Weld shops should also be aware that the TIP TIG always enables a superior ratio of arc energy produced, to the weld metal deposited. TIP TIG will always enable welds with the best possible weld fusion capability.
TIP TIG HAS THE POTENTIAL TO ALWAYS PRODUCE SUPERIOR WELD FUSION THAN DC/AC TIG WELDS: Every weld shop is aware that the highest steel and alloy weld quality for decades has been attained with DC GTAW (TIG). In contrast to DC and AC TIG, the TIP TIG process enables more deposition per-weld, this enables greater weld current to be used per-weld. Plus the unique TIP TIG weld wire to plasma delivery enables the full TIP TIG unimpeded arc plasma coverage over the weld surface. These process attributes enable a wider, more dense, higher energy plasma that with the continuous wire melt provides far superior uniform weld fusion capability with all metals. The highest possible TIP TIG arc energy levels will especially benefit sluggish metals such as stainless, duplex, inconel and other alloys. The bottom line is this weld process simply enables the best possible weld fusion with of course the lowest weld porosity.
THE TIP TIG DCEN POLARITY WITH THE SEMI-AUTOMATED WIRE FEED, BENEFITS ALL METALS. While MIG Short Circuit, Spray, Pulsed MIG and Gas Shielded Flux Cored use Reverse Polarity, a polarity in which the majority of the arc energy is maintained in the arc plasma at the tip of the continuous fed weld wire. The semi-automated TIP TIG process when used on all metals except aluminum, will use Straight (EN) Polarity. This polarity, enables rapid weld heat conductivity into the parts and this conductivity is further enhanced with the increased TIP TIG weld speeds. This capability which can reduce the weld joules by 30 – 60% can be especially beneficial from the welded part metallurgical perspective. And the high energy yet rapid freeze welds influence by the polarity enable remarkable all position weld attributes.
With welding any metals, in contrast to your MIG – FCAW or slow moving TIG welds expect with TIP TIG to generate welds with the highest mechanical and corrosion properties, and the least distortion or weld stresses. The unique low weld joules capability of TIP TIG is what enables many Titanium applications to be welded without a gas trail shield.
TIP TIG IS THE ONLY SEMI-AUTOMATED ARC WELD PROCESS THAT MAKES WELDS WITH AN INERT GAS. When the weld shop uses the semi-automated MIG and gas shielded flux cored process, the metals welded will be influenced by the REACTIVE CO2 or Oxygen in the gas mixes which stabilize the arcs and can add energy. In contrast, the semi-automated TIP TIG process uses inert argon and does not require gas mixes such as argon / helium. With the TIP TIG highest possible weld energy and welds made in an inert atmosphere, weld shops should expect on any metals that TIP TIG will always produce the cleanest possible welds that have the lowest weld porosity.
TIP TIG THE WELD BENEFITS ARE MANY, With TIP TIG, no weld spatter, no brushing or grinding. Reduced vee groove dimensions is enabled. Inter pass, pre-heat, post heat requirements can be reduced or eliminated. One easy to use, semi-automated or fully automated weld process that benefits all metals.
Note: The TIP TIG welder on the right is welding duplex fabrications used in ship construction. The weld benefits on this large duplex application are many and are discussed. However note the welder is using a weld shield that is supplying fresh air. To avoid the chrome concerns this company required welders to use these weld shields when using MIG and Gas Shielded Flux Cored. However as you can see, the duplex weld fumes are hardly visible with TIP TIG.
NOTE THE WELD BENEFITS MENTIONED HERE WILL APPLY TO ALL METALS. TO FIND THE UNIQUE DIFFERENCES BETWEEN TIP TIG - PULSED MIG - GTAW AND HOT WIRE TIG, PLEASE VISIT THE WELDING PROCESS SECTION.
FROM EM. MANAGERS, ENGINEERS AND SUPERVISORS THAT MAKE IMPORTANT WELD DECISIONS, YET DON’T UNDERSTAND THE WELD PROCESS PROCESS CAPABILITY, THE WELD PROCESS CONTROLS & BEST WELD PRACTICE REQUIREMENTS FOR WELD OPTIMIZATION ARE PERHAPS IN THE WRONG PROFESSION.
HOW IMPORTANT HAS THE TIP TIG WELD PROCESS BEEN FOR SPACEX?
AFTER STRUGGLING FOR A LONG PERIOD UP TO 2019, WITH THEIR STAINLESS WELD QUALITY (REVEALED IN DESTRUCTIVE TESTS) ON THEIR SPACE SHIP STAINLESS TANK WELDS, IT LOOKED LIKE NASA WOULD LOOK AT OTHER VENDORS TO BE A PRIMARY SUPPLY ROCKETS >2020.
FOR MANY YEARS. SPACEX USED A POOR WELD PROCESS TO MEET THE NASA WELD AND METAL TEST REQUIREMENTS. THE IRONY IS AT A WORK SHOP I PRESENTED, I INTRODUCED THE TIP TIG PROCESS TO SPACEX ENGINEERS BACK IN 2009.
FINALLY, IN 2019 – 2020 SPACEX ENGINEERS AND MANAGERS SELECTED THE TIP TIG PROCES. A PROCESS THAT QUICKLY ENABLED THEM TO PRODUCE THE STAINLESS WELD AND PART PROPERTIES THAT WOULD CONSISTENTLY PASS THE NASA DESTRUCTIVE WELD / METAL TEST REQUIREMENTS.
BY THE WAY, THE WELD QUALITY DISCUSSED HERE IS NOT A REFLECTION OF THE SPACEX WELDERS, I BELIVE ITS MORE OF AN INDICATION OF THE LACK OF FRONT OFFICE WELD PROCESS EXPERTISE THAT PREVAILED, WHICH IS NOT UNCOMMON IN THE AEROSPACE AND DEFENSE INDUSTRY.
Elon Musk (@elonmusk) Tweeted:
All METALS BENEFIT from TIP TIG. This unique semi-automated or automated arc weld process is capable of providing both the highest, manual or automated arc weld energy, with the lowest welded part heat input. For more than 60 years, no other arc weld process provided the these two important weld process attributes. Give some thought to what this means and give some thought to why most weld shops are oblivious to this 10 year old process. No weld rework. No grinding. Always attaining the highest possible mechanical and corrosion properties. No concerns with austenitic stainless for corrosion issues that result with carbide precipitation. And what about the elimination of distortion and weld stresses concerns?
All METALS BENEFIT with TIP TIG, as it’s the only semi-automated weld process the enables welds that are highly fluid, yet also have rapid freeze weld characteristics. This combination creates the easiest to use manual arc process with any all position welds.
All METALS BENEFIT when the welds are made as with TIP TIG. When using an Inert gas on welds that have high weld fluidity, and welds that have slight puddle agitation, this enables welds with the lowest weld oxidation with the lowest weld porosity.
All WELD APPLICATIONS BENEFIT with TIP as you will note in the photos and videos , with TIP TIG there typically will be no weld cleaning, no spatter or weld fume concerns. And on clean stainless, duplex or Inconel parts, the lowest Hex Chrome weld fumes will result with any semi-automated or automated TIP TIG welds.
Spacex Starship. At first. poor weld process selection and poor weld engineering.
As you read my comments about the weld management induced stainless weld issues generated at SpaceX, remember at the same time period, Elon Musk wearing his other work hat at Tesla, was again having problems with his robot welds on common metals. It’s not likely, that Elon or his Tesla / SpaceX managers and engineers in 2019 would recognize the relationship between the numerous arc weld problems that were being generated daily on Tesla cars, and on the SpaceX rockets.
Mr. Musk is an engineer, and is no different from many global engineers and managers that are supposed to be responsible for the Weld Process Ownership, yet in reality lack the required weld process controls / best practice expertise. Many managers in the aerospace, defense, power and Oil industries are not aware of the importance of Process Control expertise, and it’s logical therefore they won’t demand it from themselves or from those they employ to be responsible for the welds.
Weld Process Controls – Best Weld Practices are topics I have simplifies and focused on for 40 years. I provide the WPC self teach . training resources in the training section at this and my weldreality.com web sites. Remember these are two subjects are not taught at most of the global universities and colleges that provide mechanical and weld engineering degrees. However they should be important subjects that any weld professional should embrace.
Finally in 2020 after approx. 10 years they figured out the weld process of choice.
Note the TIP TIG blue weld units at SpaceX.
As mentioned, I established the TIP TIG process in the USA around 2009 with my business partner Tom O’Malley and we started a company called TIP TIG USA. With time, extensive difficulty and costs that neither of us could afford, we got this weld process established into the N American weld industry, an industry which we were both aware is typically highly resistant to weld process changes. The reality is the N American weld industry in general is an industry in which weld process technology that was not introduced by Lincoln, ESAB or Miller was often poorly received.
Note: At my first TIP TIG workshop I presented in Philadelphia in 2009, I presented in contrast to GMA, FCA and GTA, all the TIP TIG process feature benefits and provided actual weld demonstrations that proved the TIP TIG weld / part metallurgical benefits especially on STAINLESS.
A MESSAGE OF CONGRATULATIONS TO SPACEX. Elon when we get past your weld issues, your 2020 manned flight was magnificent to behold and the reusable rockets are amazing to behold. If I may offer a piece of free weld advice. I would suggest that when you hire someone at Spacex to manage and supervise welding and fabrication, during the interview, rather than on focusing on what school the engineer graduated from, you may want look for someone with at least 20 – 30 years of diversified weld shop floor management experience. Someone who has a resume that mentions weld process controls and best weld practices. Someone with a broad weld application and metals background, Someone who can reduce your costly weld rework and weld liability risks, Someone who takes complete weld process ownership and can train the workforce, the QA, and front office weld decision makers in the requirements for process optimization.
And last Elon, as I am simply an underpaid, poorly understood weld engineer, so as thanks for me introducing TIP TIG to N, America, a Tesla car would be appreciated, and if that’s too much, you could send or a Hall Mark Card and that would be appreciated. Regards Emily Craig. 2020.
Stainless TIP TIG Welds
Every industry that welds gauge stainless or for that matter any metals, should with a video like this really get exited. When your weld shop makes a stainless weld like this, will the welder produce a weld with, no Oxidation, no Distortion, no weld Fumes, no Cleaning, no spatter, with a high weld speed?
THE WELD BENEFITS BEING ATTAINED ON THIS STAINLESS GAUGE FILLET WELD WOULD NOT POSSIBLE IF THE WELD SHOP USES PULSED MIG OR TIG.
As you watch the weld energy generated on this low amp weld, remember that most stainless, Inconel and Duplex and other alloys tend to produce sluggish welds, which reduce weld fusion capability and add to weld porosity potential. Take a look at the weld speed attained along this 15 inch sample.
Aluminum TIP TIG Welds
Carbon Steel Welds With TIP TIG
While MIG and flux-cored will be the most common arc weld processes utilized for carbon steel welds, TIP TIG should be considered when code weld quality applications come up mainly when internal weld quality is evaluated with NDT. In contrast to the TIG – MIG – FCA processes, TIP TIG is easier to use for all position carbon steel pipe welds. TIP TIG also provides the capability to weld both the root and fill passes with higher weld quality capability than any arc weld process. TIP TIG will allow weld shops to reduce Vee or J-grooves dramatically. So why bother TIG or SMAW welding the root, and then using Pulsed MIG or Flux Cored for the fill passes, when TIP TIG will do the whole job, require less weld skills and without concern for weld rework. As for high strength steels or armor applications and welds with impact concerns, it’s impossible for any arc weld process to attain superior mechanical properties or to outperform TIP TIG as it produces the lowest welded part heat input. Also with the lowest part heat, traditional pre-heat, interpass temperatures and post-heat will typically be reduced or eliminated.
Duplex Steel Welds With TIP TIG
Duplex is a 50/50 mix of austenite and delta-ferrite and provides much higher strength than austenitic stainless, yet has similar weldability characteristics as Stainless. TIP TIG overcomes sluggish weld concerns associated with duplex and stainless and enables the lowest part distortion. As for the Hex Chrome weld fume issues on most clean welded parts, you won’t even see weld fumes. To control and balance the duplex – ferrite percentages, weld, and part, heat regulation is essential. Weld shops should be aware that TIP TIG is the only manual arc weld process that can “consistently” provide the “widest possible weld joules range” from the lowest possible weld joules to the highest joules. When welding chrome-nickel alloys or carbon steels, TIP TIG enables groove dimension reductions and provides a weld and part quality simply never attainable with TIG – Pulsed MIG and Flux Cored welds.
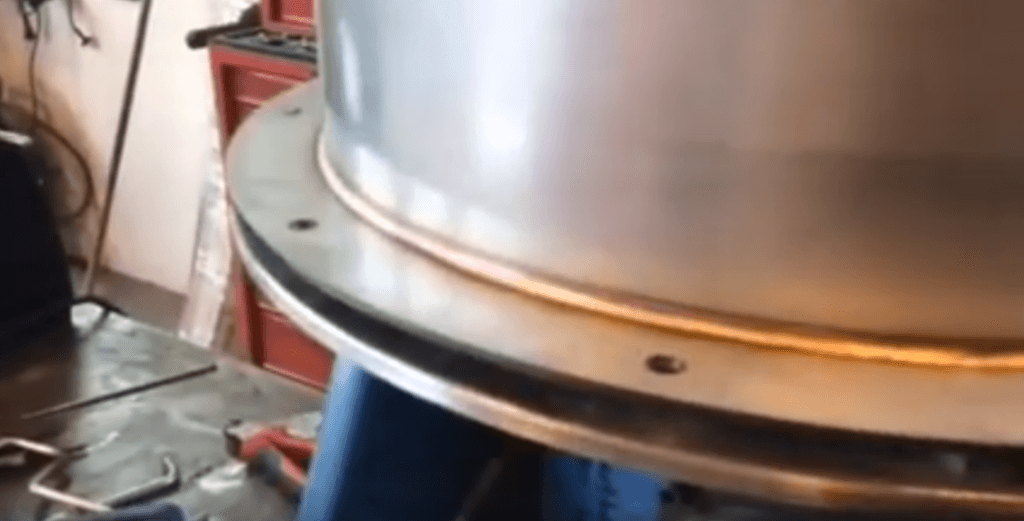
Titanium Welds With TIP TIG
Anyone who welds titanium is aware of the weld heat concerns with atmospheric t oxygen and nitrogen corrupting the titanium weld or HAZ as the weld cools. Oxidation influence can make the titanium welds and parts brittle and prone to cracking or premature fracture. To attain the highest manual arc weld quality, the slow-moving (high weld heat input) DC TIG has for decades been the weld process choice, and to minimize the titanium weld and parts oxide reactions, a cumbersome argon gas trailing shield is usually attached to the welder’s TIG torch. With TIP TIG, you have two prime weld benefits that eliminate most concerns when welding titanium. [1] DCEN TIP TIG can weld titanium parts with the weld speeds associated with MIG welds. That increased TIG weld speed with the DC Electrode Negative and the resulting rapid weld heat conduction with many titanium welds, can result in low weld and part heat in which oxidation can not occur and a gas trailing shield is not required. [2] TIP TIG is unique in that it also provides a slight weld agitation with the highest weld energy / fluidity which minimizes the potential for weld porosity that can weaken the titanium weld.
Inconel Alloy Welds With TIP TIG
Stellite Welds With TIP TIG
Hastelloy Welds With TIP TIG
Copper Nickel Welds With TIP TIG
9% Nickel Welds With TIP TIG
TIP TIG and China's largest 9% Nickel LNG Tanks.
When I bought TIP TIG to North America and started TIP TIG USA in 2009 with my partner Tom, I placed an ad in the Weld Journal about a TIP TIG workshop I was providing in Philadelphia. Some of the seminar participants were a group of engineers from CNOOC, which is one of the largest oil companies in China. At that time, CNOOC was searching for the world’s best weld process for its manual and automated subsea pipe welds made on high strength steel pipes that were ID clad with Inconel. My partner Tom and I spent about 60 hours training the CNOOC engineers on how to best control and use the TIP TIG process. CNOOC quickly adopted TIP TIG in China and used it in place of GTAW, pulsed MIG, and Flux Cored for most of their code pipe welds.